Last Updated:
2025-01-15
Last Updated:
2025-01-15
Open Hours:
8:30am-20:30pm
Whatsapp:
Open Hours:
8:30am-20:30pm
Whatsapp:

Tailored Machines for Surface and Edge Polishing
Dinosaw offers a comprehensive range of grinding and polishing machines, featuring automatic and manual options for surface and edge processing. From high-volume production lines to compact, cost-effective models, these machines cater to materials such as marble, quartz,sintered stone, mental and glass. Applications include edge grinding, slabs polishing,surface leveling, and decorative finishing for architectural and industrial projects.

steel

Granite

Marble

limestone

concrete

aluminum
Last Updated:
2025-04-15

Tailored Machines for Surface and Edge Polishing
Dinosaw offers a comprehensive range of grinding and polishing machines, featuring automatic and manual options for surface and edge processing. From high-volume production lines to compact, cost-effective models, these machines cater to materials such as marble, quartz,sintered stone, mental and glass. Applications include edge grinding, slabs polishing,surface leveling, and decorative finishing for architectural and industrial projects.

steel

Granite

Marble

limestone

concrete

aluminum
Last Updated:
2025-04-15
Automatic Polishing Machine
The Automatic Polishing Machine is a versatile and high-performance machine designed for polishing both flat surfaces and edges. It supports a wide range of materials, including granite, marble, quartz, limestone, porcelain, glass, and metals like stainless steel and aluminum.Equipped with advanced multi-head configurations and automated control systems, this machine can handle surface polishing tasks for slabs, countertops, and wall panels, as well as edge polishing for trims, borders, and steps. Additionally, it is capable of shaping and polishing curved surfaces, such as arc panels, and removing rust from metal surfaces, ensuring smooth finishes and enhanced material quality.Widely used in stone processing factories, metal workshops, and glassworks, the Automatic Polishing Machine delivers consistent, high-quality results while reducing labor costs and increasing productivity. Its adaptability and precision make it an essential choice for businesses seeking reliable solutions for surface and edge finishing.
What is Grinding and Polishing Machine?
Grinding and polishing machines include automatic and manual models for surface and edge polishing.
Automatic Machines: Designed for hard materials like glass, metals, and quartz, ideal for industrial-scale production.Manual Machines: Suitable for detailed and smaller-scale processing tasks.
Materials Processed:Glass and Ceramics: Glass, porcelain slabs.Natural Stones: Marble, granite, sandstone, and limestone.Composites: Sintered stone, terrazzo, EPS.Metals (Automatic Only): Aluminum, stainless steel.
Applications Include:Glass: Edge grinding, surface polishing.Stones: Countertops, tabletops, decorative slabs, and edge finishing.Metals: Surface rust removal and polishing.Composites: Architectural panels, furniture, and decorative elements.
Manual Polishing Machine
The Manual Polishing Machine is a compact and portable machine ideal for smaller-scale polishing tasks. Designed for natural stones such as granite, marble, and limestone, it is capable of polishing surfaces, edges, and shaping edges for decorative applications.This machine is commonly used for polishing countertops, edge trims, and custom designs. Its flexibility and user-friendly operation make it suitable for small workshops or on-site projects requiring fine adjustments and customization.While limited to stone materials, the Manual Polishing Machine provides an affordable and efficient solution for achieving high-quality finishes. Its reliability and versatility make it a practical tool for professionals in the stone processing industry.

The most popular related processing cases
You Can Refer To

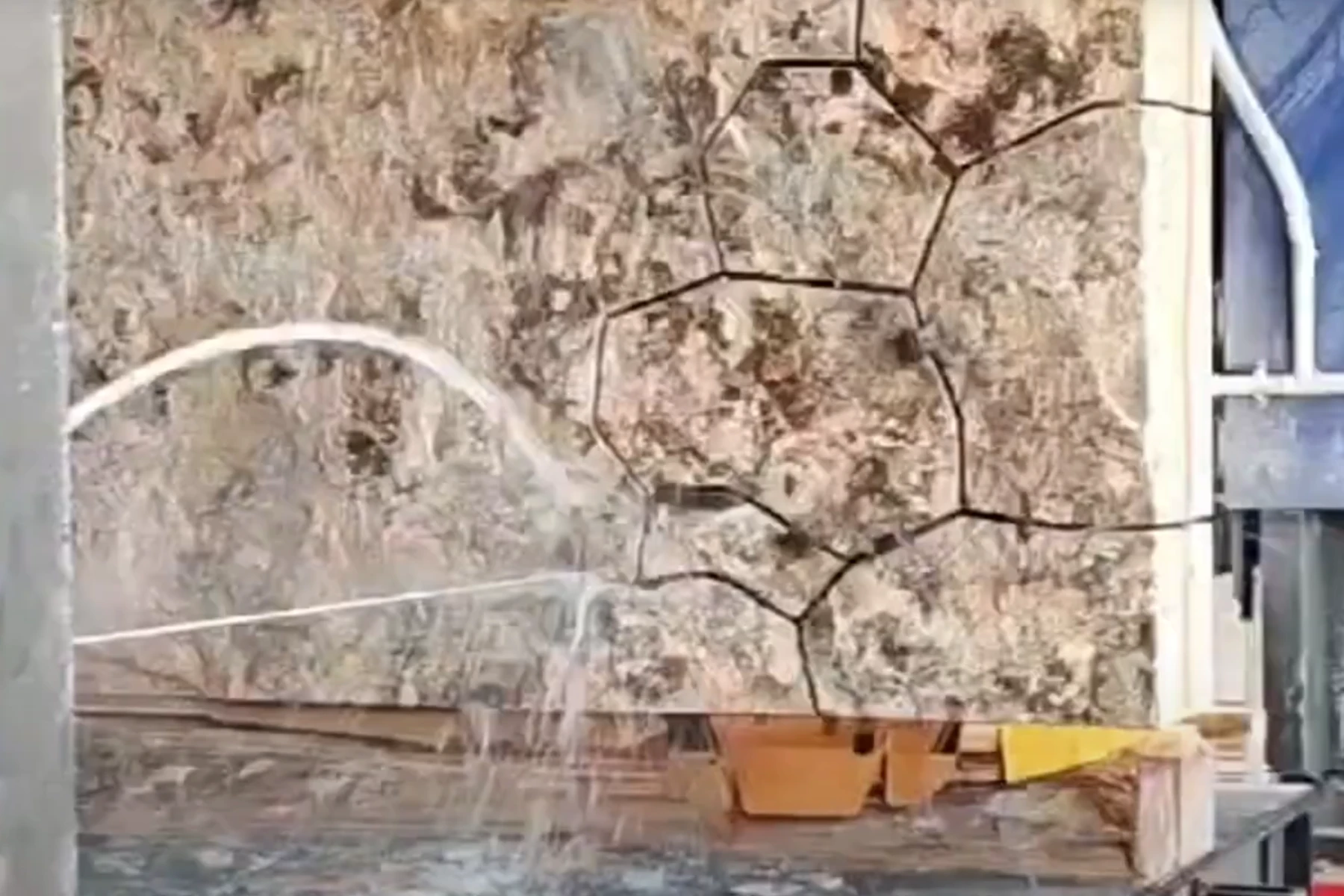
Granite Mosaic Cutting Case - CNC Wire Saw Machine Supports Quanzhou Factory

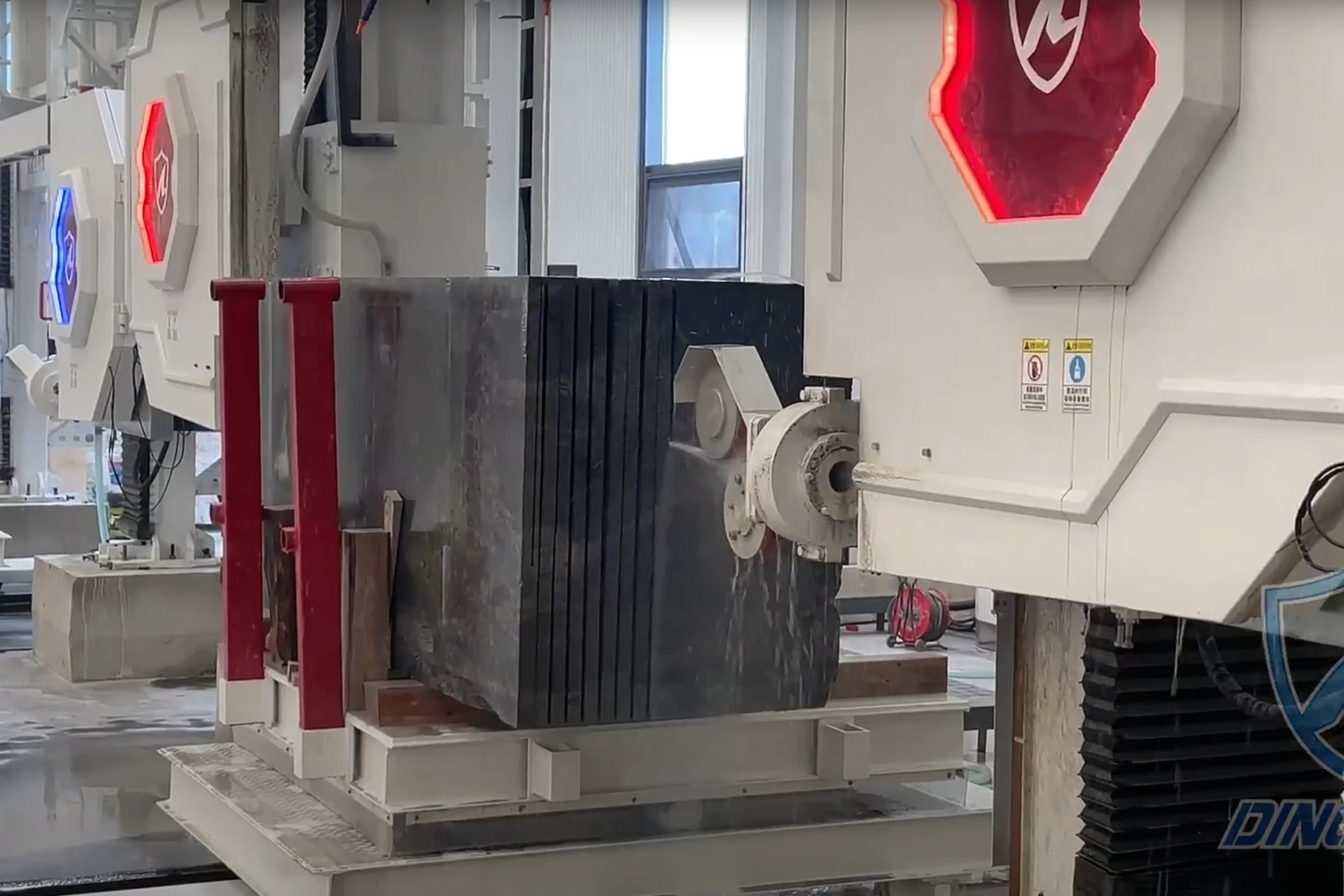
Marble Block Slab Cutting Case - CNC Wire Saw Machine Supports Spanish Factory

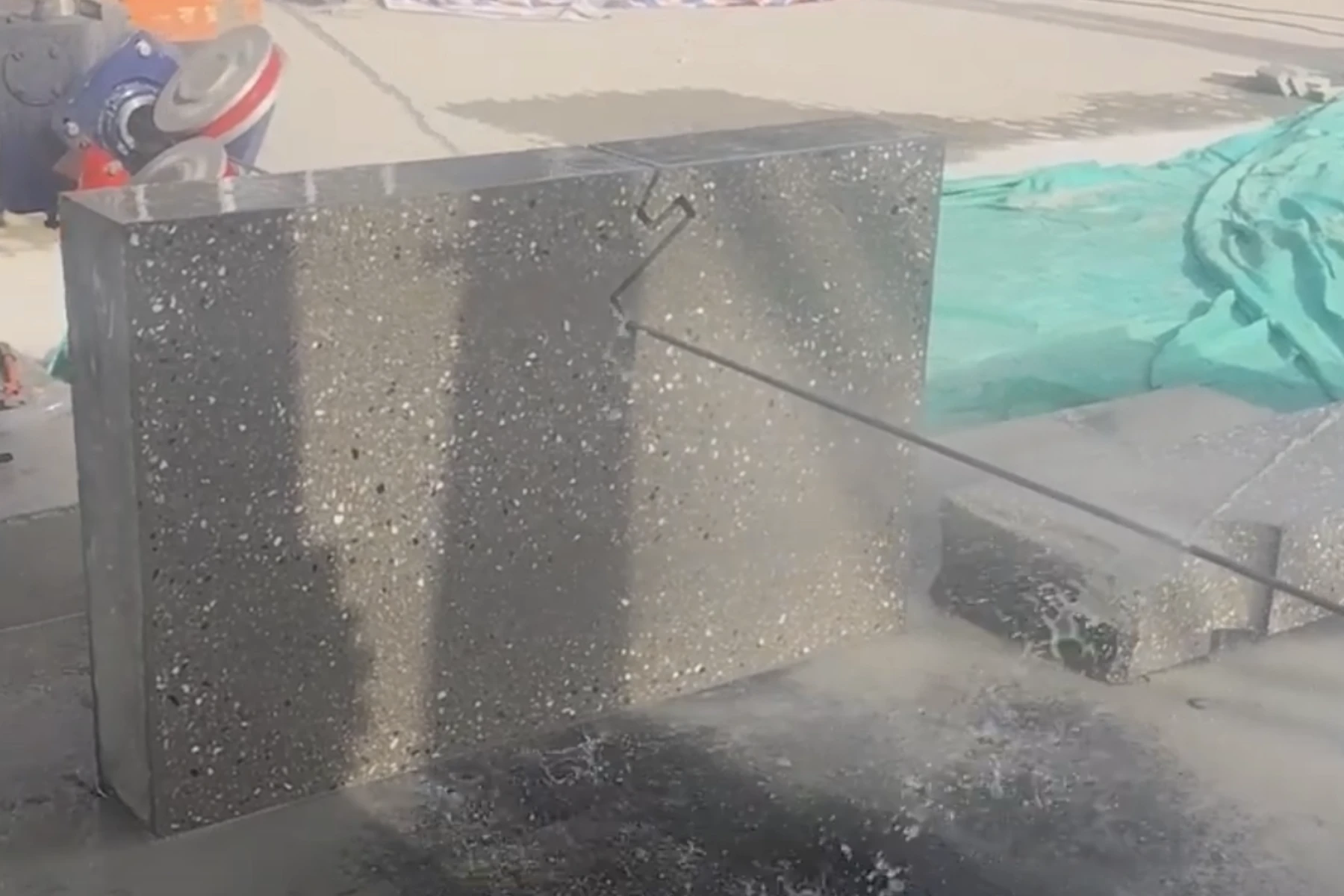
Cement Product Cutting Case - CNC Wire Saw Machine Supports Spanish Factory

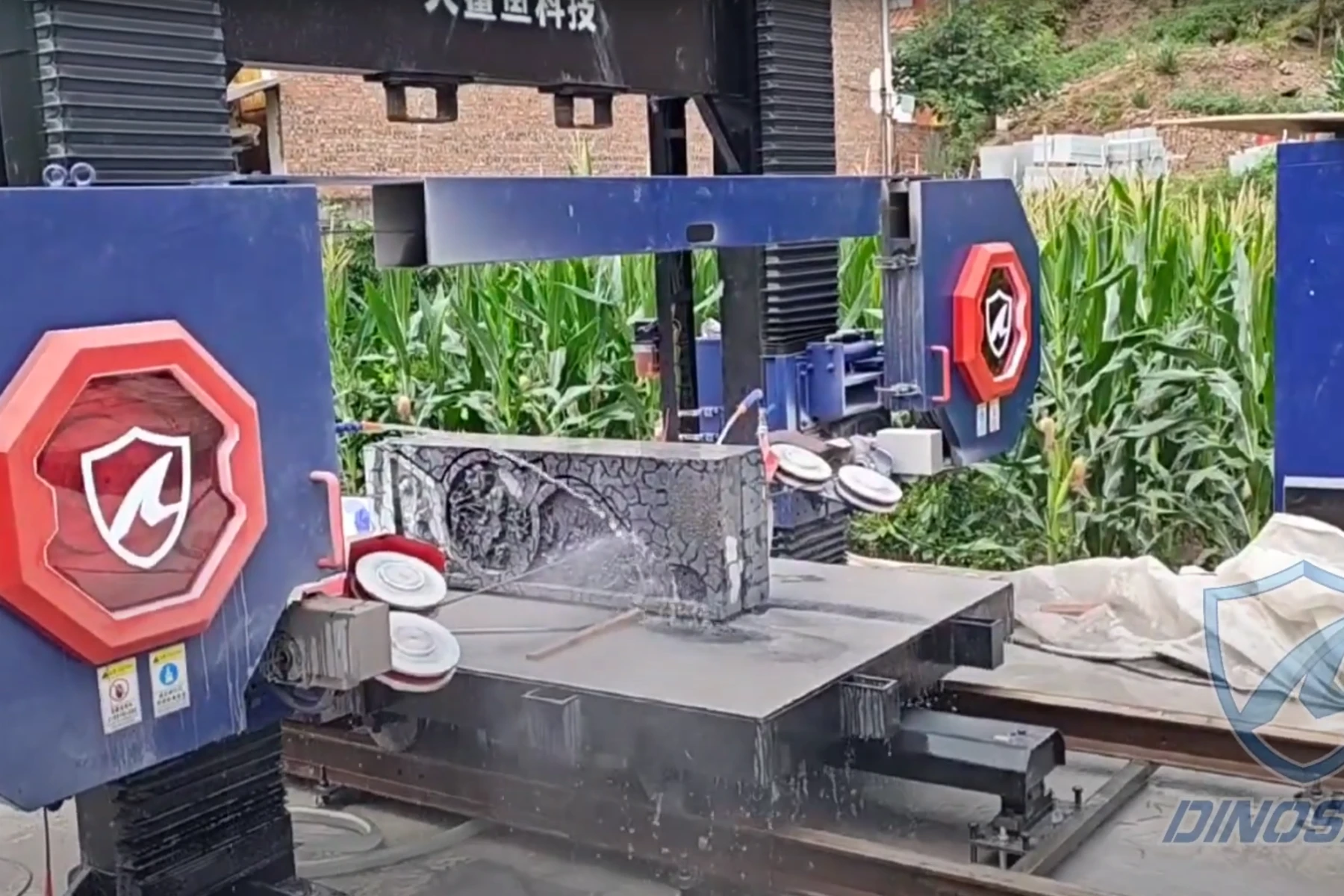
Granite Tombstone Case - CNC Wire Saw Machine Supports Chongqing Factory
More

Worth-reading articles on
industrial processing Machinery Cases
The practical videos On
How to install, use, and maintain industrial
Your Guide to Choosing the Best Grinding and Polishing Machine
Grinding and polishing machines are essential tools for refining surfaces and edges across a wide range of materials. Whether achieving a mirror finish on countertops or shaping decorative edges, selecting the right machine ensures precision, efficiency, and versatility.
With Dinosaw’s advanced solutions, you’ll find automatic polishing machines for industrial-scale tasks and manual polishing machines for flexible, custom applications. This guide will help you choose the perfect machine for your needs.
What Are Grinding and Polishing Machines?
Grinding and polishing machines are specialized tools designed for surface and edge finishing. These machines perform diverse tasks, such as achieving smooth, glossy finishes on surfaces, crafting custom edge profiles like bullnose or ogee, and enhancing the aesthetics of architectural and decorative items.
Dinosaw offers two primary machine types. Automatic polishing machines are ideal for high-volume, consistent processing, while manual polishing machines are perfect for small-batch and customized tasks.
Types of Grinding and Polishing Machines
Automatic Polishing Machines
Designed for industrial applications, automatic polishing machines ensure consistent quality and high efficiency. Features include CNC and PLC control systems for automation, multi-head configurations for simultaneous processing, and customizable settings for speed and pressure.
These machines are compatible with materials like marble, granite, glass, sintered stone, and metals such as aluminum and stainless steel. Applications include polishing countertops, refining decorative edges, and producing high-end furniture components.
Manual Polishing Machines
Compact and versatile, manual polishing machines are suited for detailed projects or workshops. They feature lightweight designs for portability, flexibility for unique finishes, and intuitive controls for efficient operation.
They are compatible with materials like sandstone, acrylic, and reinforced plastics, making them ideal for small-scale production, artisan crafts, and edge shaping for residential or commercial installations.
Edge Profiles and Applications
Grinding and polishing machines are essential for shaping edges with precision. Common edge profiles include straight edges for modern designs, beveled edges for subtle slants, bullnose edges for smooth, rounded finishes, and ogee edges for elegant architectural components. Custom shapes can also be crafted for unique furniture or artistic projects.
Steps to Purchasing Your Ideal Grinding and Polishing Machine
Define your objectives by identifying the materials you’ll process, determining whether your focus is on surface polishing or edge shaping, and assessing your production scale.
Explore Dinosaw’s machine options to compare automatic machines for industrial efficiency and manual machines for flexibility. Review specifications such as supported edge profiles, material compatibility, and maintenance costs.
Consult Dinosaw experts to discuss your production needs, receive tailored recommendations, and explore customization options for specific edge-shaping capabilities.
Plan your budget and ROI by evaluating machine costs against long-term savings from improved efficiency and reduced labor. Include additional expenses like setup and training.
Request demonstrations to see the machine in action, test edge-shaping capabilities, and review polished samples for quality.
Finalize customization and installation by tailoring the machine to your factory’s dimensions, scheduling professional setup, and planning regular maintenance for long-term performance.
Why Choose Dinosaw Grinding and Polishing Machines?
Dinosaw machines are trusted worldwide for their precision engineering, enabling intricate edge profiles and complex finishes. Their material flexibility allows for processing a wide range of materials, and customization options ensure the machines align with unique project needs. Built for durability in demanding environments, Dinosaw machines are supported globally with after-sales services to maintain operational reliability.
Conclusion
Dinosaw’s grinding and polishing machines offer unmatched versatility for achieving smooth surfaces and intricate edges. Whether you need high-volume industrial solutions or compact, flexible tools for custom projects, Dinosaw’s advanced technology and expert support deliver exceptional results.
Contact Dinosaw today to explore the ideal machine for your needs!

Automatic Polishing Machine
The Automatic Polishing Machine is a versatile and high-performance machine designed for polishing both flat surfaces and edges. It supports a wide range of materials, including granite, marble, quartz, limestone, porcelain, glass, and metals like stainless steel and aluminum.Equipped with advanced multi-head configurations and automated control systems, this machine can handle surface polishing tasks for slabs, countertops, and wall panels, as well as edge polishing for trims, borders, and steps. Additionally, it is capable of shaping and polishing curved surfaces, such as arc panels, and removing rust from metal surfaces, ensuring smooth finishes and enhanced material quality.Widely used in stone processing factories, metal workshops, and glassworks, the Automatic Polishing Machine delivers consistent, high-quality results while reducing labor costs and increasing productivity. Its adaptability and precision make it an essential choice for businesses seeking reliable solutions for surface and edge finishing.
What is Grinding and Polishing Machine?
Grinding and polishing machines include automatic and manual models for surface and edge polishing.
Automatic Machines: Designed for hard materials like glass, metals, and quartz, ideal for industrial-scale production.Manual Machines: Suitable for detailed and smaller-scale processing tasks.
Materials Processed:Glass and Ceramics: Glass, porcelain slabs.Natural Stones: Marble, granite, sandstone, and limestone.Composites: Sintered stone, terrazzo, EPS.Metals (Automatic Only): Aluminum, stainless steel.
Applications Include:Glass: Edge grinding, surface polishing.Stones: Countertops, tabletops, decorative slabs, and edge finishing.Metals: Surface rust removal and polishing.Composites: Architectural panels, furniture, and decorative elements.
Manual Polishing Machine
The Manual Polishing Machine is a compact and portable machine ideal for smaller-scale polishing tasks. Designed for natural stones such as granite, marble, and limestone, it is capable of polishing surfaces, edges, and shaping edges for decorative applications.This machine is commonly used for polishing countertops, edge trims, and custom designs. Its flexibility and user-friendly operation make it suitable for small workshops or on-site projects requiring fine adjustments and customization.While limited to stone materials, the Manual Polishing Machine provides an affordable and efficient solution for achieving high-quality finishes. Its reliability and versatility make it a practical tool for professionals in the stone processing industry.

The most popular related processing cases
You Can Refer To

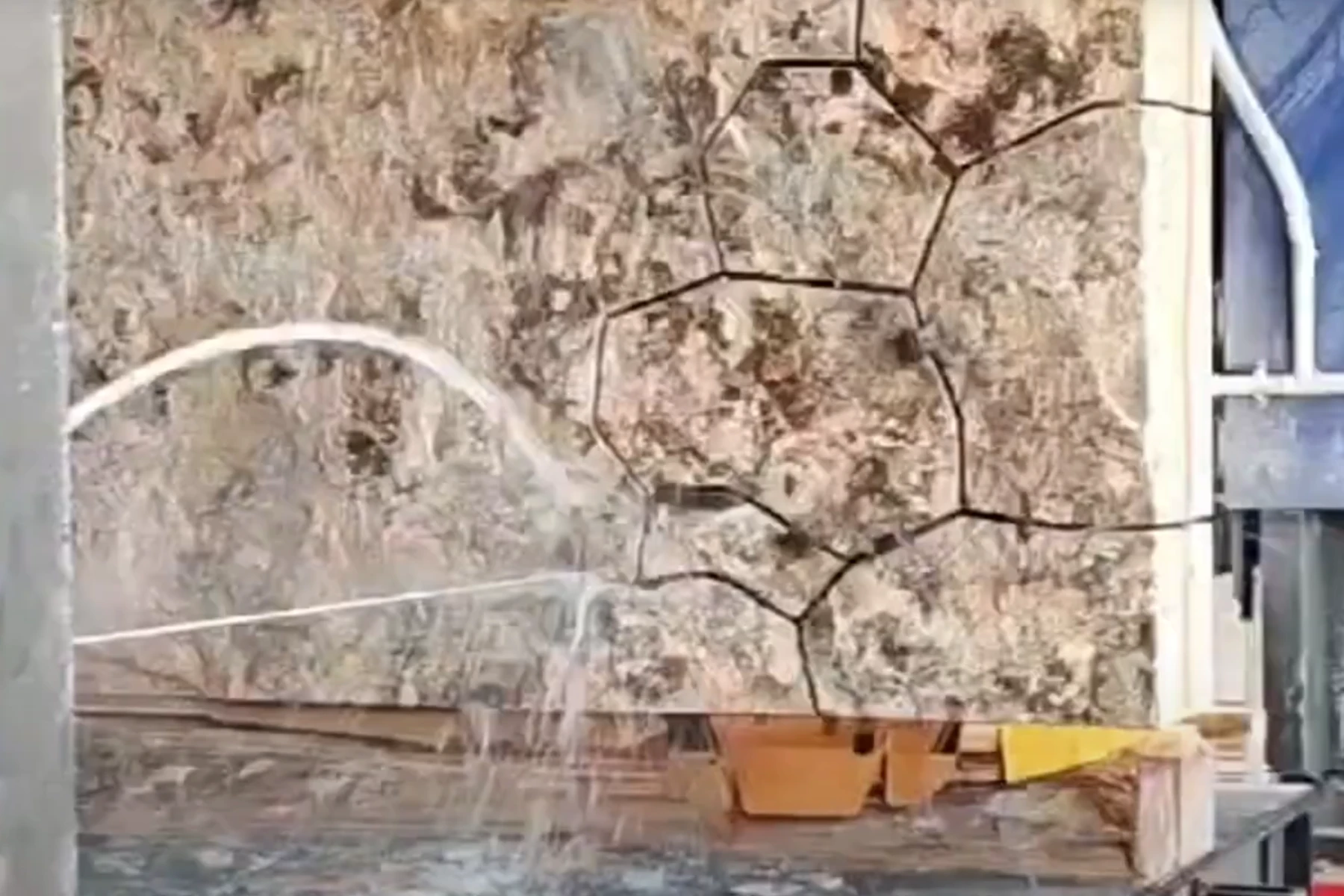
Granite Mosaic Cutting Case - CNC Wire Saw Machine Supports Quanzhou Factory

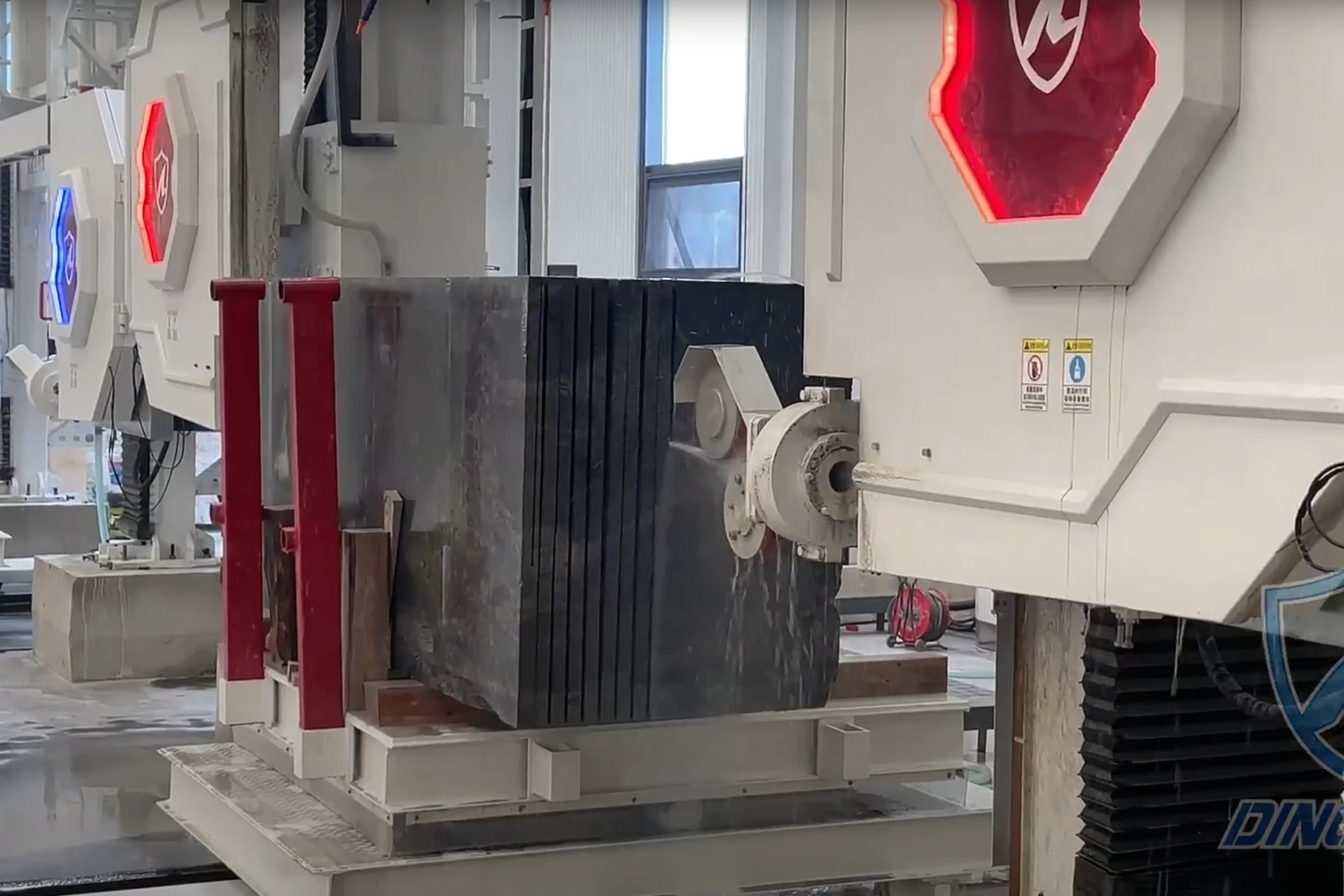
Marble Block Slab Cutting Case - CNC Wire Saw Machine Supports Spanish Factory

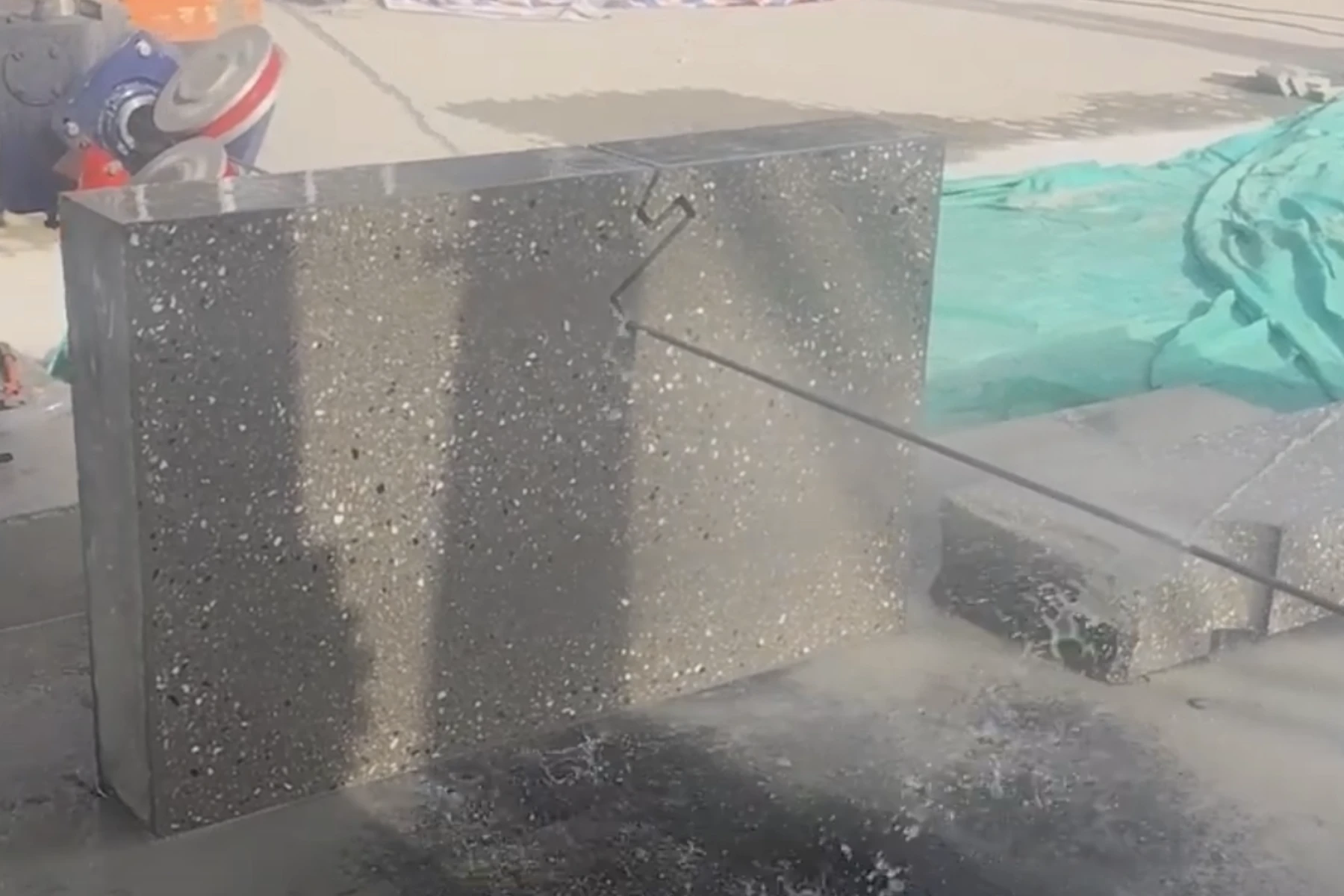
Cement Product Cutting Case - CNC Wire Saw Machine Supports Spanish Factory

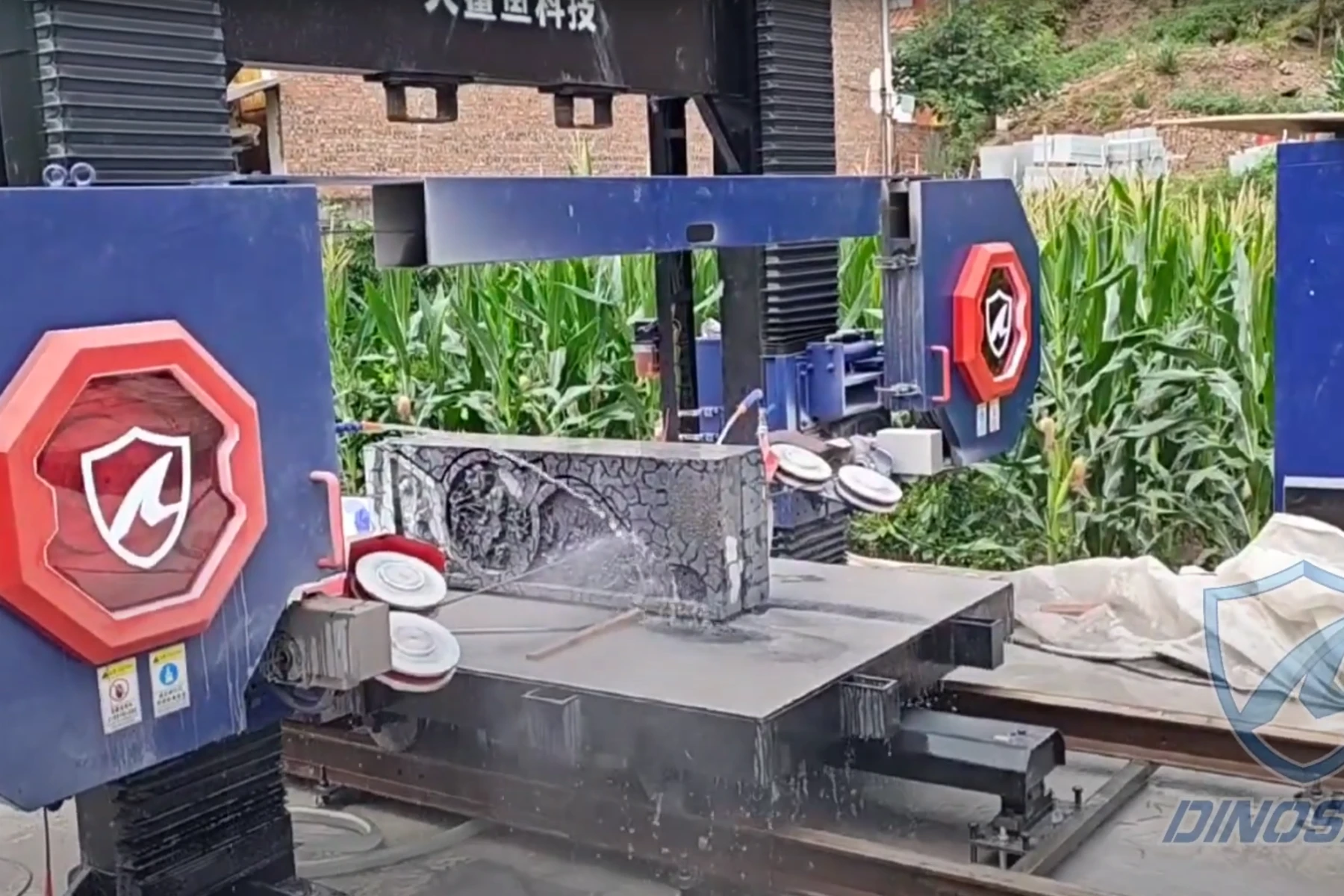
Granite Tombstone Case - CNC Wire Saw Machine Supports Chongqing Factory
More

Worth-reading articles on
industrial processing Machinery Cases
The practical videos On
How to install, use, and maintain industrial
Your Guide to Choosing the Best Grinding and Polishing Machine
Grinding and polishing machines are essential tools for refining surfaces and edges across a wide range of materials. Whether achieving a mirror finish on countertops or shaping decorative edges, selecting the right machine ensures precision, efficiency, and versatility.
With Dinosaw’s advanced solutions, you’ll find automatic polishing machines for industrial-scale tasks and manual polishing machines for flexible, custom applications. This guide will help you choose the perfect machine for your needs.
What Are Grinding and Polishing Machines?
Grinding and polishing machines are specialized tools designed for surface and edge finishing. These machines perform diverse tasks, such as achieving smooth, glossy finishes on surfaces, crafting custom edge profiles like bullnose or ogee, and enhancing the aesthetics of architectural and decorative items.
Dinosaw offers two primary machine types. Automatic polishing machines are ideal for high-volume, consistent processing, while manual polishing machines are perfect for small-batch and customized tasks.
Types of Grinding and Polishing Machines
Automatic Polishing Machines
Designed for industrial applications, automatic polishing machines ensure consistent quality and high efficiency. Features include CNC and PLC control systems for automation, multi-head configurations for simultaneous processing, and customizable settings for speed and pressure.
These machines are compatible with materials like marble, granite, glass, sintered stone, and metals such as aluminum and stainless steel. Applications include polishing countertops, refining decorative edges, and producing high-end furniture components.
Manual Polishing Machines
Compact and versatile, manual polishing machines are suited for detailed projects or workshops. They feature lightweight designs for portability, flexibility for unique finishes, and intuitive controls for efficient operation.
They are compatible with materials like sandstone, acrylic, and reinforced plastics, making them ideal for small-scale production, artisan crafts, and edge shaping for residential or commercial installations.
Edge Profiles and Applications
Grinding and polishing machines are essential for shaping edges with precision. Common edge profiles include straight edges for modern designs, beveled edges for subtle slants, bullnose edges for smooth, rounded finishes, and ogee edges for elegant architectural components. Custom shapes can also be crafted for unique furniture or artistic projects.
Steps to Purchasing Your Ideal Grinding and Polishing Machine
Define your objectives by identifying the materials you’ll process, determining whether your focus is on surface polishing or edge shaping, and assessing your production scale.
Explore Dinosaw’s machine options to compare automatic machines for industrial efficiency and manual machines for flexibility. Review specifications such as supported edge profiles, material compatibility, and maintenance costs.
Consult Dinosaw experts to discuss your production needs, receive tailored recommendations, and explore customization options for specific edge-shaping capabilities.
Plan your budget and ROI by evaluating machine costs against long-term savings from improved efficiency and reduced labor. Include additional expenses like setup and training.
Request demonstrations to see the machine in action, test edge-shaping capabilities, and review polished samples for quality.
Finalize customization and installation by tailoring the machine to your factory’s dimensions, scheduling professional setup, and planning regular maintenance for long-term performance.
Why Choose Dinosaw Grinding and Polishing Machines?
Dinosaw machines are trusted worldwide for their precision engineering, enabling intricate edge profiles and complex finishes. Their material flexibility allows for processing a wide range of materials, and customization options ensure the machines align with unique project needs. Built for durability in demanding environments, Dinosaw machines are supported globally with after-sales services to maintain operational reliability.
Conclusion
Dinosaw’s grinding and polishing machines offer unmatched versatility for achieving smooth surfaces and intricate edges. Whether you need high-volume industrial solutions or compact, flexible tools for custom projects, Dinosaw’s advanced technology and expert support deliver exceptional results.
Contact Dinosaw today to explore the ideal machine for your needs!

CONTINUOUSLY IMPROVE PRODUCTIVITY FOR USER
Customer first | Teamwork | Embrace change | Integrity | Passion | Commitment
CONTINUOUSLY IMPROVE PRODUCTIVITY FOR USER
Customer first | Teamwork | Embrace change | Integrity | Passion | Commitment

Last Updated:
2025-04-15
Tailored Machines for Surface and Edge Polishing
Dinosaw offers a comprehensive range of grinding and polishing machines, featuring automatic and manual options for surface and edge processing. From high-volume production lines to compact, cost-effective models, these machines cater to materials such as marble, quartz,sintered stone, mental and glass. Applications include edge grinding, slabs polishing,surface leveling, and decorative finishing for architectural and industrial projects.

steel

Granite

Marble

limestone

concrete

aluminum
CONTINUOUSLY IMPROVE PRODUCTIVITY FOR USER
Customer first | Teamwork | Embrace change | Integrity | Passion | Commitment
CONTINUOUSLY IMPROVE PRODUCTIVITY FOR USER
Customer first | Teamwork | Embrace change | Integrity | Passion | Commitment
Automatic Polishing Machine
The Automatic Polishing Machine is a versatile and high-performance machine designed for polishing both flat surfaces and edges. It supports a wide range of materials, including granite, marble, quartz, limestone, porcelain, glass, and metals like stainless steel and aluminum.
Equipped with advanced multi-head configurations and automated control systems, this machine can handle surface polishing tasks for slabs, countertops, and wall panels, as well as edge polishing for trims, borders, and steps. Additionally, it is capable of shaping and polishing curved surfaces, such as arc panels, and removing rust from metal surfaces, ensuring smooth finishes and enhanced material quality.
Widely used in stone processing factories, metal workshops, and glassworks, the Automatic Polishing Machine delivers consistent, high-quality results while reducing labor costs and increasing productivity. Its adaptability and precision make it an essential choice for businesses seeking reliable solutions for surface and edge finishing.
Manual Polishing Machine
The Manual Polishing Machine is a compact and portable machine ideal for smaller-scale polishing tasks. Designed for natural stones such as granite, marble, and limestone, it is capable of polishing surfaces, edges, and shaping edges for decorative applications.
This machine is commonly used for polishing countertops, edge trims, and custom designs. Its flexibility and user-friendly operation make it suitable for small workshops or on-site projects requiring fine adjustments and customization.
While limited to stone materials, the Manual Polishing Machine provides an affordable and efficient solution for achieving high-quality finishes. Its reliability and versatility make it a practical tool for professionals in the stone processing industry.
What is Grinding and Polishing Machine?
Grinding and polishing machines include automatic and manual models for surface and edge polishing.
Automatic Machines: Designed for hard materials like glass, metals, and quartz, ideal for industrial-scale production.Manual Machines: Suitable for detailed and smaller-scale processing tasks.
Materials Processed:Glass and Ceramics: Glass, porcelain slabs.Natural Stones: Marble, granite, sandstone, and limestone.Composites: Sintered stone, terrazzo, EPS.Metals (Automatic Only): Aluminum, stainless steel.
Applications Include:Glass: Edge grinding, surface polishing.Stones: Countertops, tabletops, decorative slabs, and edge finishing.Metals: Surface rust removal and polishing.Composites: Architectural panels, furniture, and decorative elements.

The most popular related processing cases
You Can Refer To
The practical videos on
How to install, use, and maintain industrial

Worth-reading articles on
industrial processing Machinery Cases
Your Guide to Choosing the Best Grinding and Polishing Machine

Grinding and polishing machines are essential tools for refining surfaces and edges across a wide range of materials. Whether achieving a mirror finish on countertops or shaping decorative edges, selecting the right machine ensures precision, efficiency, and versatility.
With Dinosaw’s advanced solutions, you’ll find automatic polishing machines for industrial-scale tasks and manual polishing machines for flexible, custom applications. This guide will help you choose the perfect machine for your needs.
What Are Grinding and Polishing Machines?
Grinding and polishing machines are specialized tools designed for surface and edge finishing. These machines perform diverse tasks, such as achieving smooth, glossy finishes on surfaces, crafting custom edge profiles like bullnose or ogee, and enhancing the aesthetics of architectural and decorative items.
Dinosaw offers two primary machine types. Automatic polishing machines are ideal for high-volume, consistent processing, while manual polishing machines are perfect for small-batch and customized tasks.
Types of Grinding and Polishing Machines
Automatic Polishing Machines
Designed for industrial applications, automatic polishing machines ensure consistent quality and high efficiency. Features include CNC and PLC control systems for automation, multi-head configurations for simultaneous processing, and customizable settings for speed and pressure.
These machines are compatible with materials like marble, granite, glass, sintered stone, and metals such as aluminum and stainless steel. Applications include polishing countertops, refining decorative edges, and producing high-end furniture components.
Manual Polishing Machines
Compact and versatile, manual polishing machines are suited for detailed projects or workshops. They feature lightweight designs for portability, flexibility for unique finishes, and intuitive controls for efficient operation.
They are compatible with materials like sandstone, acrylic, and reinforced plastics, making them ideal for small-scale production, artisan crafts, and edge shaping for residential or commercial installations.
Edge Profiles and Applications
Grinding and polishing machines are essential for shaping edges with precision. Common edge profiles include straight edges for modern designs, beveled edges for subtle slants, bullnose edges for smooth, rounded finishes, and ogee edges for elegant architectural components. Custom shapes can also be crafted for unique furniture or artistic projects.
Steps to Purchasing Your Ideal Grinding and Polishing Machine
Define your objectives by identifying the materials you’ll process, determining whether your focus is on surface polishing or edge shaping, and assessing your production scale.
Explore Dinosaw’s machine options to compare automatic machines for industrial efficiency and manual machines for flexibility. Review specifications such as supported edge profiles, material compatibility, and maintenance costs.
Consult Dinosaw experts to discuss your production needs, receive tailored recommendations, and explore customization options for specific edge-shaping capabilities.
Plan your budget and ROI by evaluating machine costs against long-term savings from improved efficiency and reduced labor. Include additional expenses like setup and training.
Request demonstrations to see the machine in action, test edge-shaping capabilities, and review polished samples for quality.
Finalize customization and installation by tailoring the machine to your factory’s dimensions, scheduling professional setup, and planning regular maintenance for long-term performance.
Why Choose Dinosaw Grinding and Polishing Machines?
Dinosaw machines are trusted worldwide for their precision engineering, enabling intricate edge profiles and complex finishes. Their material flexibility allows for processing a wide range of materials, and customization options ensure the machines align with unique project needs. Built for durability in demanding environments, Dinosaw machines are supported globally with after-sales services to maintain operational reliability.
Conclusion
Dinosaw’s grinding and polishing machines offer unmatched versatility for achieving smooth surfaces and intricate edges. Whether you need high-volume industrial solutions or compact, flexible tools for custom projects, Dinosaw’s advanced technology and expert support deliver exceptional results.
Contact Dinosaw today to explore the ideal machine for your needs!
CONTINUOUSLY IMPROVE PRODUCTIVITY FOR USER
Customer first | Teamwork | Embrace change | Integrity | Passion | Commitment