
Introduction: The Importance of Choosing the Right Stone Cutting Machine
In the stone fabrication industry, whether you are a stone fabricator, a stone factory, or a stone manufacturer, selecting the appropriate stone cutting machine is one of the most important decisions you’ll make. The right machine not only impacts the quality and efficiency of your cutting processes but also determines the overall productivity and profitability of your business.
Overview of the Stone Industry
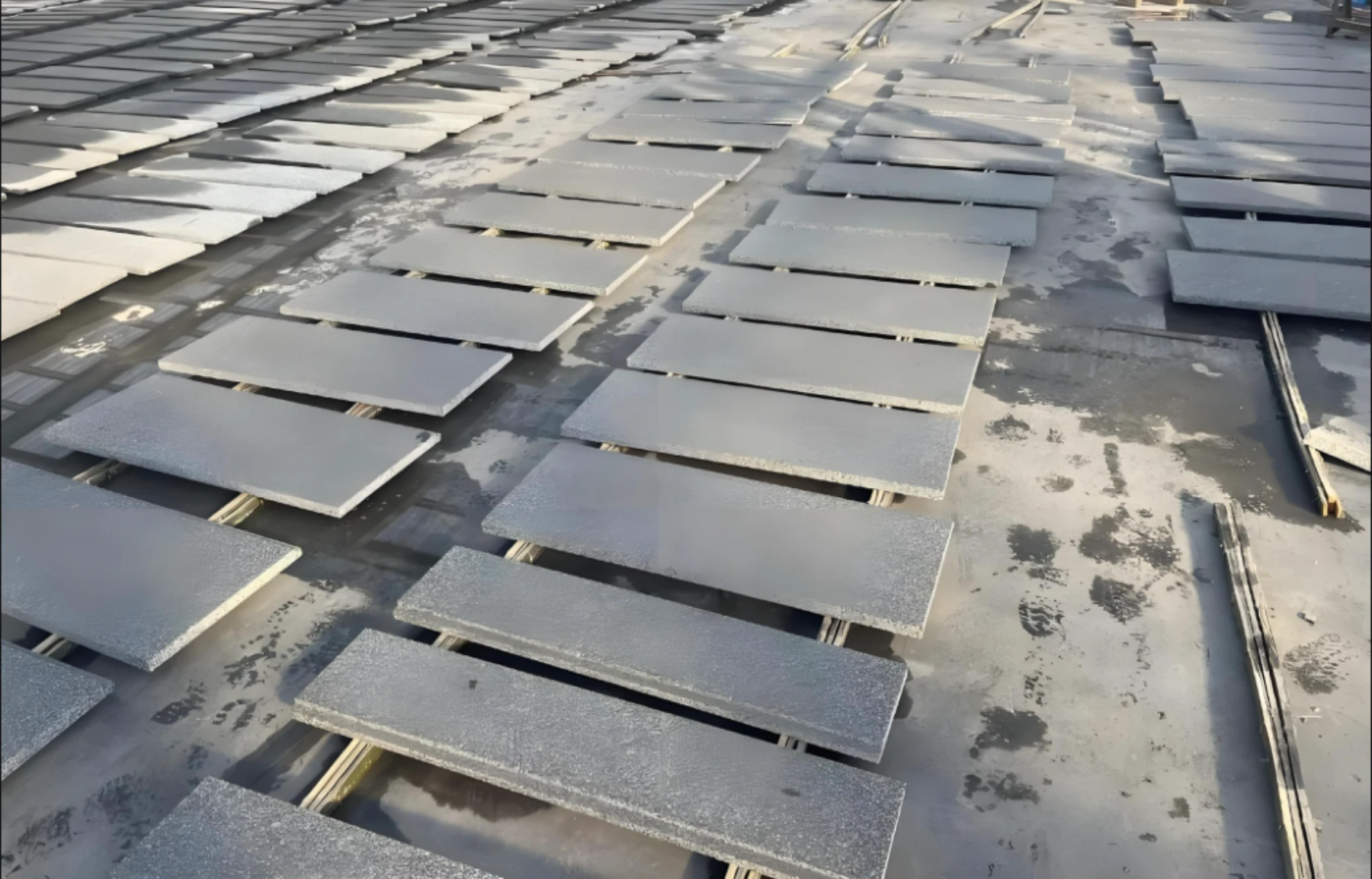
Stone fabrication, manufacturing, and processing are specialized industries where various types of stones—such as granite, marble, quartz, and limestone—are cut, shaped, and finished for use in construction, interior design, and art. Stone fabricators, manufacturers, and factories all have different requirements based on their scope of work, from countertops and flooring to facades and sculptures.
Why Choosing the Right Stone Cutting Machine Matters
The choice of a stone cutting machine has a direct impact on:
Productivity: The right machine ensures high efficiency, reducing downtime and speeding up the production process.
Quality: Precision cutting ensures the integrity of the stone and the final product. Poor cutting can lead to imperfections that compromise both aesthetics and strength.
Cost Efficiency: The wrong machine may lead to increased operational costs due to inefficient processes, higher energy usage, and more frequent maintenance.
Longevity of Equipment: Properly chosen equipment will require less maintenance, reducing overall repair costs and extending the lifespan of the machine.
Whether you're a small stone fabrication shop or a large-scale stone manufacturer, the right stone cutting machine is essential to your success. This guide will help you evaluate your specific needs and make an informed decision based on the machine types available, their capabilities, and the demands of your stone fabrication or manufacturing business.
Introduction to Common Stone Cutting Machines
The most commonly used stone cutting machines in the industry include:
CNC Diamond Wire Saw Cutting Machine: Ideal for intricate, precise cuts with high versatility and minimal material wastage.
Bridge Saw: A staple in many shops and factories, great for straight cuts and large slabs.
Waterjet Cutting Machine: Excellent for highly detailed designs and multi-material cuts, ideal for intricate stone patterns or mixed-material projects.
Manual Cutting Machines: Simple, affordable, and best for smaller, less complex jobs that require manual intervention.
Each of these machines has its strengths and weaknesses. Understanding these will allow you to choose the best one based on your business’s specific cutting needs.
The purpose of this article is to provide a step-by-step guide to selecting the right stone cutting machine for your stone fabrication shop, stone factory, or stone manufacturing business. This guide will help you understand how to match the capabilities of the various machines with the materials you cut, the precision needed, the volume of production, and other critical factors like maintenance, efficiency, and costs.
Factors to Consider When Choosing a Stone Cutting Machine
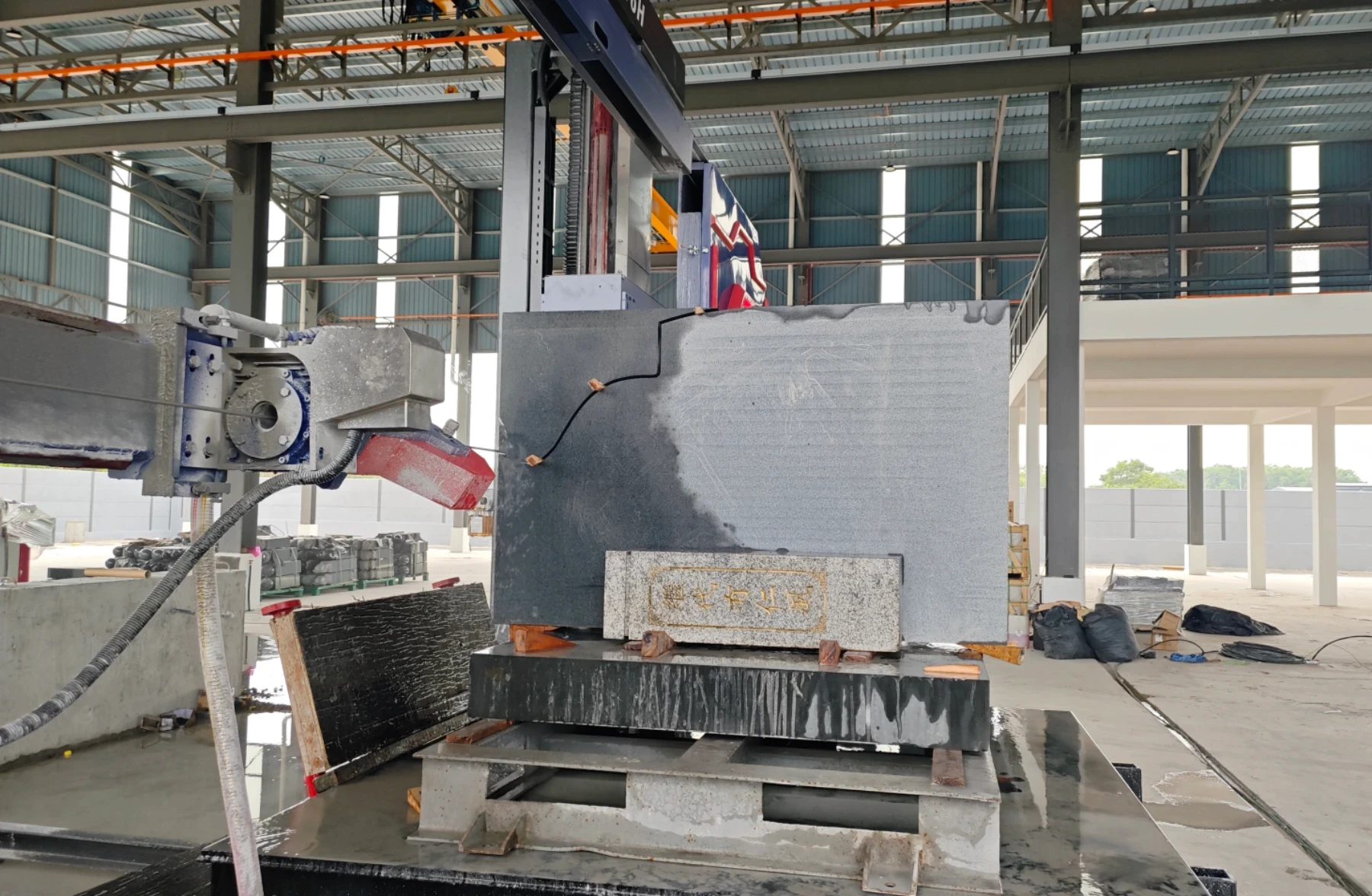
Choosing the right stone cutting machine is not just about selecting the most advanced model; it's about aligning the machine's features with your specific business needs. Here are the key factors you should consider when selecting a stone cutting machine for your stone fabrication shop, stone factory, or stone manufacturing business.
Type of Stone and Material Requirements
Different stones have different properties, and the material type you work with will significantly influence your choice of cutting machine. Here’s a breakdown of what to consider:
Granite: Requires a robust and powerful machine, as it is dense and hard. Bridge saws and CNC diamond wire saw cutting machines are commonly used for granite due to their strength and precision.
Marble: Softer than granite, but still requires accurate cutting. Waterjet cutting machines can be ideal for cutting marble with intricate designs, while bridge saws work well for larger, straight cuts.
Limestone and Sandstone: These materials are generally softer and easier to cut. Manual cutting machines or less powerful bridge saws might suffice for such stones.
Composite Stones (e.g., Quartz): These require precision and are typically best processed with machines that can handle consistent, clean cuts—CNC diamond wire saws and waterjet cutting machines are ideal.
Cutting Precision and Complexity
Depending on the end product you are producing, the precision of your cuts will be a major factor in choosing a machine.
Standard Cuts: If your business primarily deals with basic straight cuts (e.g., countertops, flooring), a bridge saw will often suffice. These machines are reliable and efficient for large slabs with minimal complexity.
Intricate Cuts and Detailed Work: For complicated shapes, such as curves or angles, or when precision is paramount (for sculptures or high-end designs), machines like the CNC diamond wire saw or waterjet cutting machine are better suited. These machines offer high precision and flexibility, and can handle more intricate designs.
Angle Cuts and Beveling: If you need to perform tasks like beveling or chamfering, specialized bridge saws with angle adjustment or manual cutting machines might be needed.
Product Size and Dimensions
The size of the products you are creating will influence the type of cutting machine required. For instance:
Large Slabs: If your projects involve cutting large stone slabs, like those used for countertops or facades, a bridge saw or CNC diamond wire saw is ideal due to their ability to handle large materials.
Smaller Pieces: For smaller stone products or more intricate cuts, manual cutting machines or waterjet cutting machines may be sufficient.
Thickness of Stone: If you’re working with particularly thick stones (over 3-4 inches), ensure your cutting machine can handle such dimensions without compromising the quality of the cut.
Speed and Efficiency
The efficiency of your cutting machine can directly impact your production speed and costs. Different machines offer varying levels of speed:
Bridge Saws: These are efficient at cutting straight lines and are excellent for mass production where speed is crucial. However, they may be less efficient for more complex cuts.
CNC Diamond Wire Saw: While typically slower than bridge saws, CNC diamond wire saws offer precision and flexibility for intricate designs, which can save time in the long run when working on detailed projects.
Waterjet Cutting Machines: Waterjets are efficient for intricate and detailed cuts but might be slower compared to other machines when working on larger or less complex cuts.
Speed and efficiency should align with your production demands. Consider how often you need to process large volumes of material versus highly detailed work.
Ease of Operation and Automation
Manual vs. Automated Machines: Manual cutting machines offer hands-on control but require more skilled labor and are slower. They are best suited for small-scale operations or businesses that don't deal with high volumes. Automated machines, like the CNC diamond wire saw or bridge saw, offer higher speed and efficiency, requiring less labor and allowing for consistent, repeatable cuts.
CNC Systems: Machines with CNC capabilities, especially those equipped with self-developed CNC systems (like those offered by DINOSAW), can simplify operations. With user-friendly interfaces that don’t require the learning of complex G-codes, operators can get started in just a few minutes, significantly improving workflow and reducing the learning curve.
Maintenance Requirements
Ease of Maintenance: Machines with fewer moving parts and simpler components tend to be easier to maintain. Bridge saws often require less maintenance than high-tech systems like waterjet cutters, which involve more complex components.
Availability of Parts: Consider the availability of spare parts and technical support when selecting a machine. Machines from reputable manufacturers like DINOSAW often come with long-term support, including a network of spare parts and experienced technicians for servicing the equipment.
Longevity and Durability: Machines with solid construction and robust components tend to last longer. For example, CNC diamond wire saws and waterjet cutting machines are more durable than manual cutting machines, but they might require more regular upkeep due to their complexity.
Environmental Impact
Consider the environmental impact of your machine. Some machines, like the waterjet cutting machine, use water to cut, reducing dust and fumes. However, you’ll need to manage water disposal and recycling. On the other hand, CNC diamond wire saws and bridge saws might produce more dust, but you can mitigate this with proper ventilation and dust-collection systems.
Customization and Additional Features by DINOSAW
At DINOSAW, we understand that every stone cutting project has its unique challenges. That’s why we offer customization options tailored to meet specific requirements. For example:
Dust Collection Systems: If your workshop produces high amounts of dust during the cutting process, we offer advanced dust collection solutions to keep your workspace clean and compliant with safety regulations.
Dry Cutting Requirements: For businesses that require dry cutting to meet environmental or operational needs, we offer customized machines designed to minimize water usage while maintaining performance.
Tailored Solutions: Based on your cutting demands and environmental protection requirements, we can work with you to integrate additional features like automated feeding systems, specialized cutting heads, or custom CNC programming options.
These custom solutions ensure that the machine you choose is fully aligned with your operational and environmental needs.
Cost and Budget
The cost of the machine is always a critical factor. Machines like manual cutting machines are less expensive but might be limited in functionality and speed. On the other hand, machines like waterjet cutters and CNC diamond wire saws come with higher initial costs but offer better precision, flexibility, and efficiency in the long term.
Ultimately, the right choice for your business will depend on balancing your budget with the functionality required to meet your business goals.
Types of Stone Cutting Machines: Which One Fits Your Needs?
When choosing a stone cutting machine for your stone fabrication shop, stone factory, or stone manufacturing business, it's crucial to understand the different types of machines available and how their features align with your production needs. Below, we will discuss the main types of stone cutting machines offered by DINOSAW and how each one serves specific purposes in the stone processing industry.
CNC Diamond Wire Saw Cutting Machine
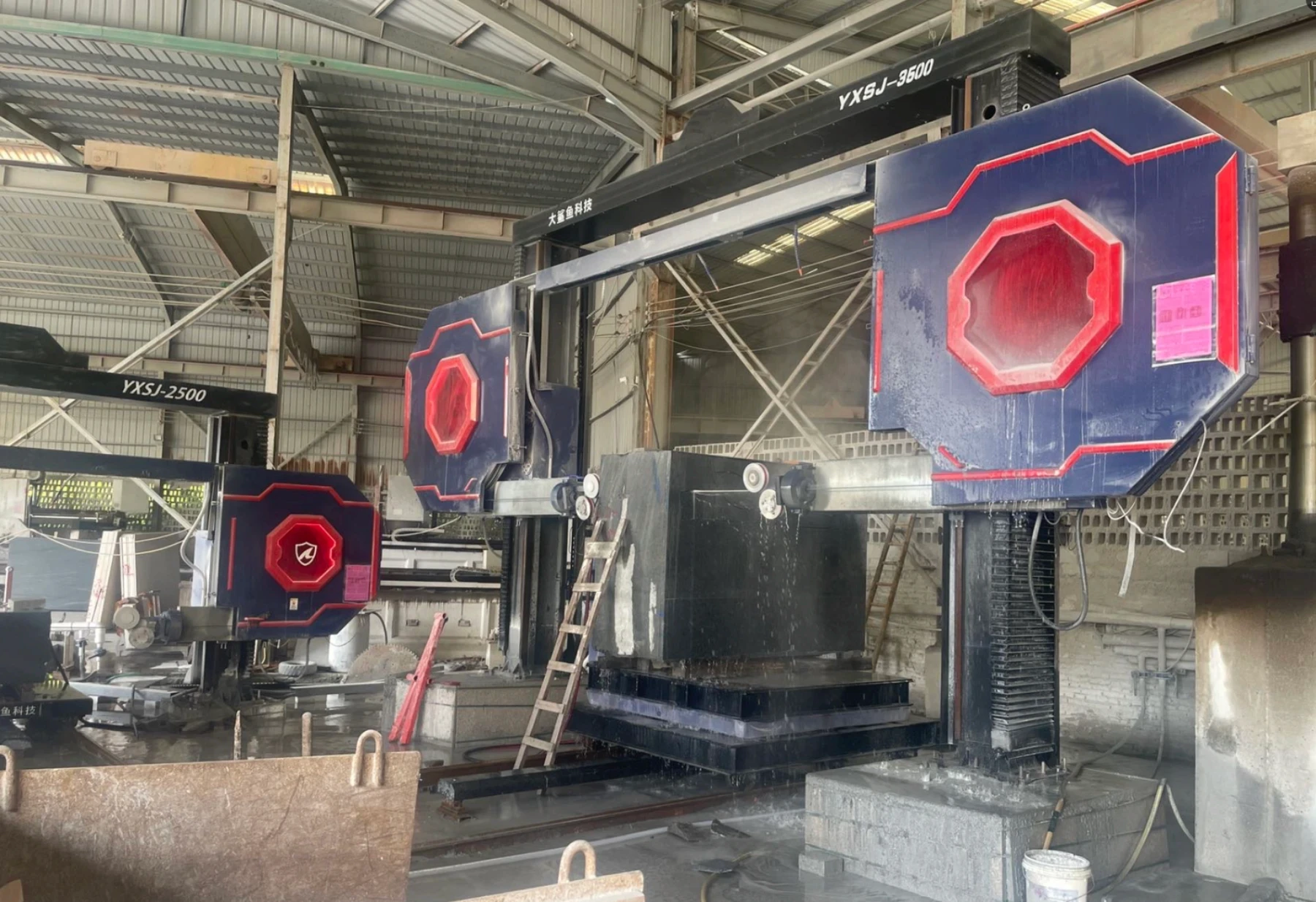
Recommended models:CNC Diamond Wire Saw Cutting Machine Pro
CNC diamond wire saws are perfect for businesses that require precise, intricate, and detailed cuts. These machines use a rotating diamond-coated wire to cut through the stone. The flexibility and precision of CNC technology make these machines ideal for:
Intricate Shapes and Designs: When working with complex shapes such as curves, angles, or custom patterns, the CNC diamond wire saw allows for high precision and intricate cutting that other machines can't achieve.
Thin Cuts: This machine can cut through very thin slabs without causing breakage, which is essential for materials like marble and some composites.
Multi-Functionality: The CNC system allows users to easily program and repeat patterns, making this machine suitable for high-volume production of standardized shapes or customized designs.
Examples: CNC diamond wire saws are ideal for cutting complex shapes such as gravestones, landscape stones, or other intricate stone designs.
Key Features:
High precision and flexibility for intricate cuts.
Ability to cut very thin slabs.
CNC control system for easy programming.
Ideal For: Precision, detailed cuts, and custom designs.
Bridge Saw
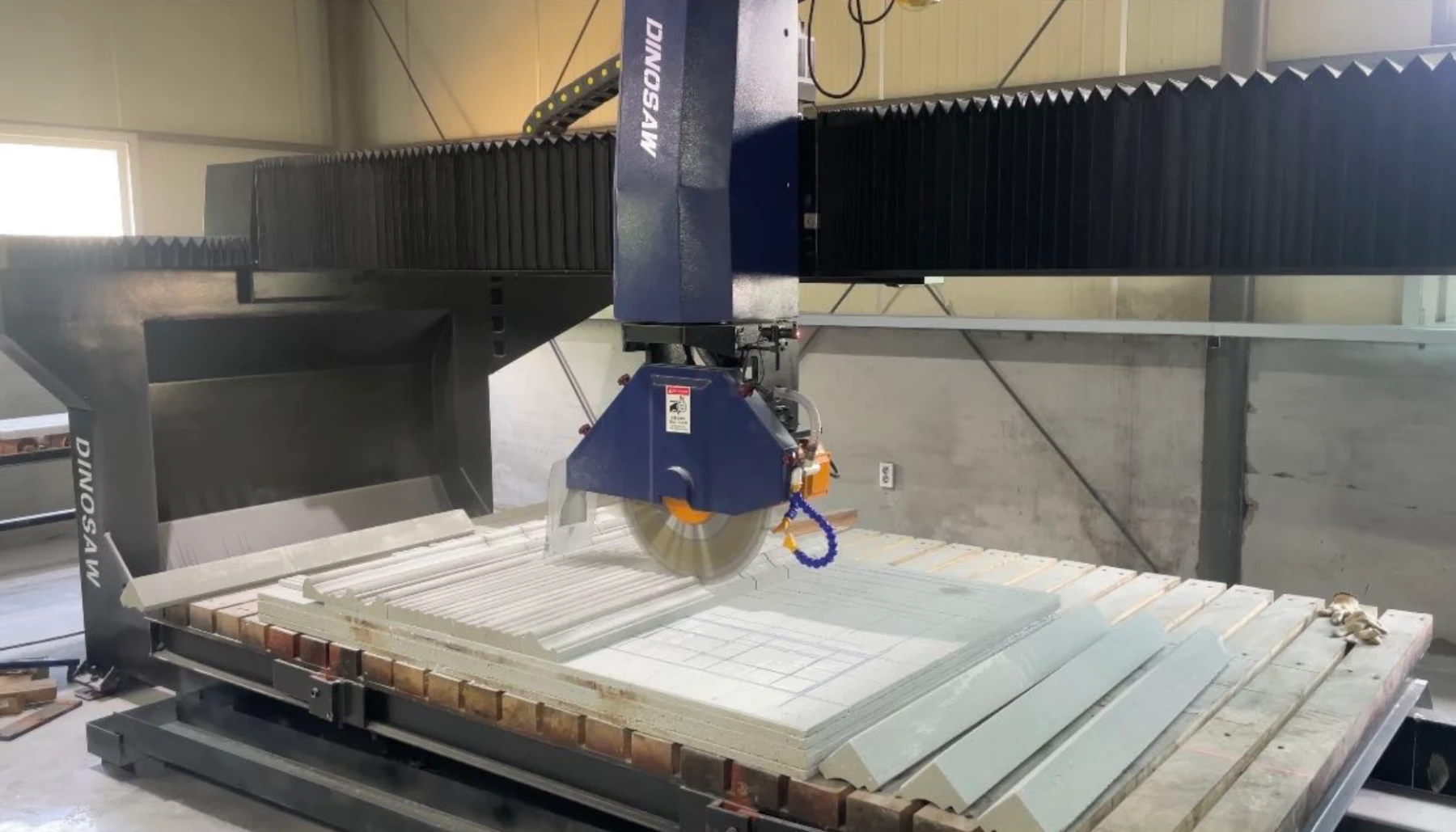
Recommended models:5 axis Bridge Saw
Bridge saws are one of the most common types of stone cutting machines used in stone fabrication. These machines are designed for straight cuts and are capable of handling larger, more rigid stone slabs. Bridge saws have a diamond blade that moves in a straight line to perform cuts across large stone surfaces.
Heavy Duty Cutting: Bridge saws are best suited for cutting large stone slabs, such as granite or quartz, and are capable of handling thick and heavy materials.
High-Speed Cutting: These machines are often faster than wire saws, making them ideal for businesses that need to cut large quantities of stone quickly.
Angle Adjustments: Many modern bridge saws come with adjustable heads, allowing them to perform angle cuts, beveling, and chamfering with high precision.
Curved and Circular Cuts: Some bridge saws are equipped with additional features that allow for curved cuts and arc cuts, making them versatile for various applications like countertops, water troughs, and washbasins.
Simple Hole Drilling: Certain models even come with an engraving head, which allows the user to perform basic drilling operations, ideal for cutting features like holes or small indentations.
Key Features:
High-speed, straight-line cutting for large slabs.
Adjustable blade for angle cuts, beveling, and chamfering.
Ability to perform curved, circular, and arc cuts.
Capability to drill simple holes or perform engraving.
Ideal For: Cutting large stone slabs like granite, quartz, and marble in straight lines and angles, as well as making curved cuts, beveling, and simple hole drilling for products like water sinks or countertops.
Waterjet Cutting Machine
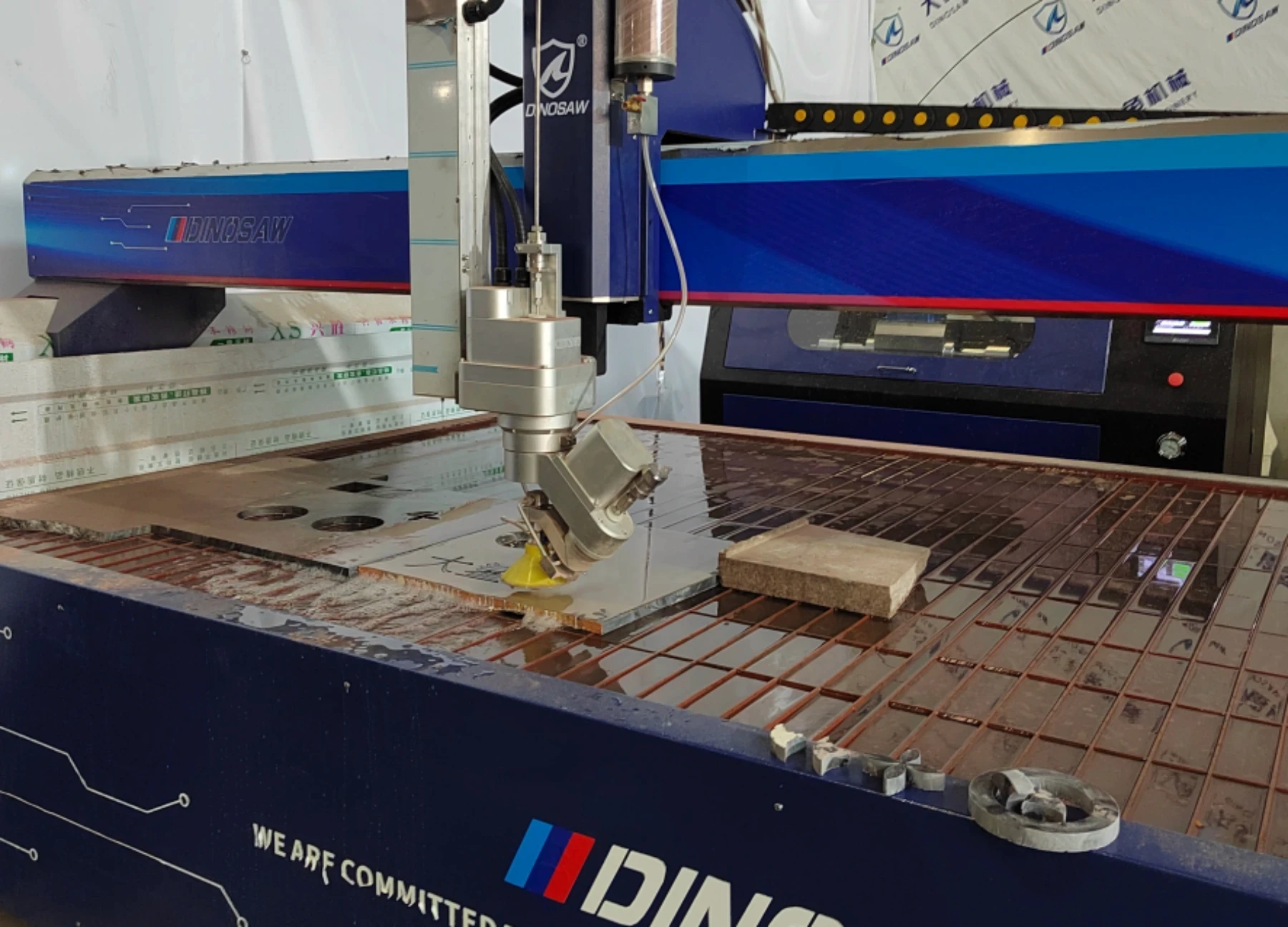
Recommended models:Waterjet cutting machine
Waterjet cutting machines use high-pressure water mixed with abrasive particles to slice through stone with incredible precision. These machines are highly versatile and capable of performing a range of complex cuts.
Precision and Detail: Waterjet machines are perfect for cutting detailed designs, curves, or highly customized shapes in materials such as marble, granite, or even engineered stone.
Minimal Waste: Waterjet cutting produces a small kerf (cut width), which reduces material wastage.
No Heat Affected Zone (HAZ): Unlike other cutting methods, waterjet cutting does not produce heat, which prevents any deformation or thermal damage to the stone.
Complex Patterns: The precision of waterjets makes them ideal for cutting intricate patterns, tile mosaics, or backlit stone panels.
Common Applications: Waterjet cutting is widely used for tile inlay designs, countertops, and cutting complex patterns for decorative purposes in the stone industry.
Key Features:
Precision cutting without heat distortion.
Capable of cutting intricate shapes and patterns.
Reduces material wastage.
Ideal for tile inlay, countertop designs, and complex patterns.
Ideal For: Cutting intricate designs, complex shapes, and detailed patterns, with minimal material waste, especially in applications like mosaic tiles, backlit stone panels, and customized countertop designs.
Manual Stone Cutting Machine
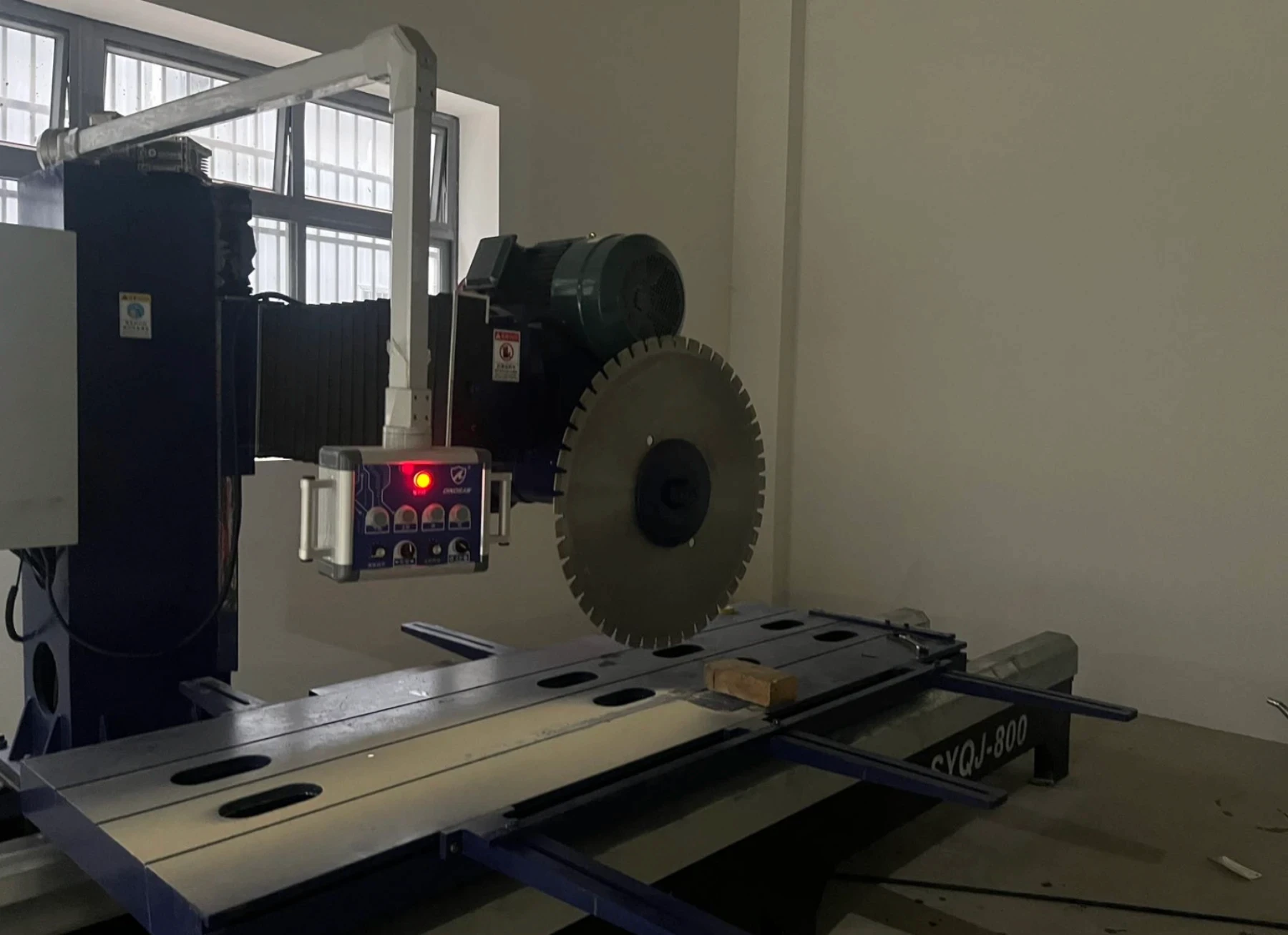
Recommended models:Manual Stone Cutting Machine
Manual cutting machines are simpler tools that require more operator skill to cut stone. These machines are typically used for smaller-scale operations or in environments where cutting is less frequent or needs to be done in a more controlled, hands-on manner.
Not Portable, but Compact: Manual cutting machines are not typically portable, but they are often smaller in size, making them more suitable for small shops or spaces with limited room.
Affordable Option: These machines are the most affordable option, making them a great choice for small-scale operations or businesses with limited budgets.
Precision Dependent on Skill: While not as precise as automated machines, manual cutting machines can still produce accurate cuts, but their precision depends on the operator’s skill.
Limited Cutting Angles: Manual cutting machines are limited to vertical cuts and 45-degree cuts, making them best for small-scale stone slabs or edge work like chamfering.
Key Features:
Low-cost option for small-scale jobs.
Requires more operator skill.
Smaller and more compact for limited spaces.
Limited to vertical and 45-degree cutting.
Ideal For: Smaller operations or businesses with limited budgets, and for cutting stone in compact spaces, such as cutting small slabs or chamfering edges.
Key Differences for Stone Cutting Machine Applications
Diamond Wire Saw: Best for cutting large, thick stone materials and for 3D shaping. The wire saw can cut through thicker and more complex stone shapes like gravestones, landscape stones, and other sculptural pieces. However, it is not suitable for flat cutting like countertops or tabletop pieces.
Bridge Saw: Excellent for straight-line cutting, but also capable of making angled cuts, bevels, and curved shapes. Ideal for tasks like cutting countertops, wash basins, sink cutouts, and other flat surface cutting tasks where speed and efficiency are required.
Waterjet Cutter: Ideal for detailed, intricate designs and cuts where precision is essential. Waterjets are often used in decorative stonework like mosaic patterns, backlit panels, or cutting complex shapes like floor tiles.
Manual Cutter: Most suitable for small-scale production or entry-level cutting tasks like chamfering edges or cutting small slabs, especially for businesses on a budget.
Choosing the Right Stone Cutting Machine for Your Needs
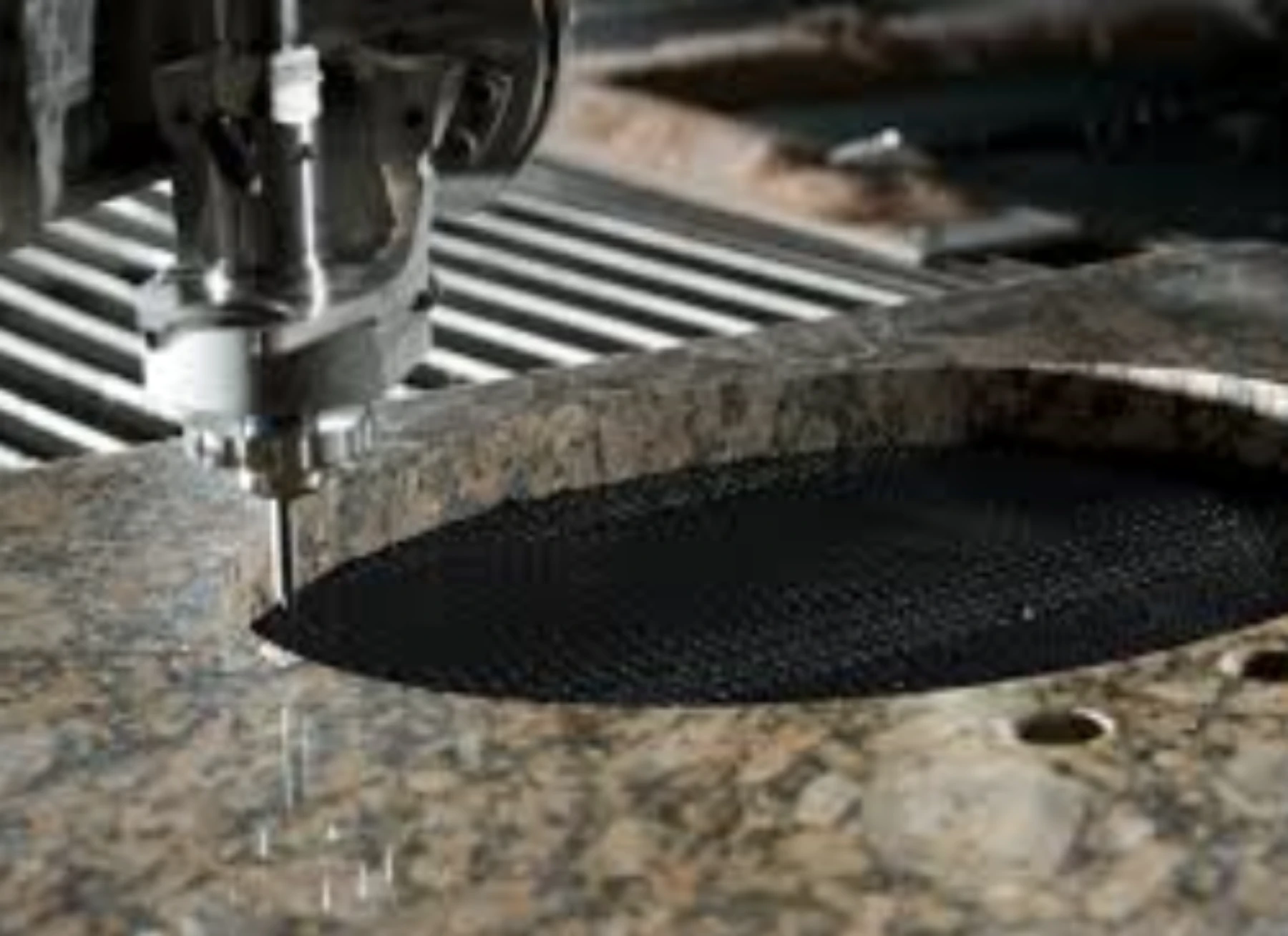
When selecting the appropriate stone cutting machine for your stone factory, stone manufacturer, or stone fabricator, it's essential to match the machine's features and capabilities with your specific needs and business requirements. Here are the most important factors to consider:
Production Volume and Efficiency
If your business handles large quantities of stone on a daily basis, efficiency will be a primary concern. Machines like bridge saws are designed for high-speed cutting and are perfect for businesses that need to cut large slabs in straight lines quickly and efficiently. For more complex cutting tasks, such as intricate designs or custom patterns, a waterjet cutter or CNC diamond wire saw might be the best choice, offering high precision and customizability.
High-Volume Cutting: Bridge saws are your go-to machines, delivering high-speed, efficient cuts with minimal downtime.
Precision and Detail: For businesses that require cutting intricate shapes or custom designs, CNC diamond wire saws or waterjets are more suitable, though they come with a higher initial investment.
Cutting Complexity and Functionality
Another critical factor in choosing the right stone cutting machine is the complexity of the cuts required for your projects. If you're regularly cutting simple shapes or straight lines, then a bridge saw will serve you well. For intricate patterns, mosaics, or custom shapes, you should consider machines like waterjets or CNC wire saws, which are capable of handling more detailed work.
Straight Cuts & Angles: Bridge saws are optimal for this type of cutting, especially for granite countertops and flooring slabs.
Custom & Intricate Shapes: If your work requires cutting custom patterns or 3D sculptures, a CNC diamond wire saw or waterjet is more appropriate.
Material Types and Thickness
Different stone cutting machines handle materials of varying thicknesses and durabilities. For example, if your business cuts large slabs of granite, marble, or engineered stone, you'll want a machine that can handle thick, dense materials. CNC diamond wire saws are ideal for these materials, as they can cut through thick stones with ease, while a bridge saw will excel with materials that require more straightforward cutting.
Thick and Dense Materials: CNC diamond wire saws are ideal for cutting through thick granite or heavy stones like landscape stones and sculptural designs.
Thinner Slabs: Bridge saws are more efficient for cutting through thinner slabs or for more common tasks like countertops and backsplashes.
Precision vs. Speed
The balance between precision and speed will heavily influence your choice. If precision is more important (for highly detailed designs, custom patterns, or cuts requiring accuracy), waterjet cutting or a CNC diamond wire saw will be the better options. However, if speed and efficiency are critical (such as in cutting large volumes of standard slabs), then a bridge saw may be the right choice.
High Precision, Complex Cuts: Waterjet cutting machines and CNC diamond wire saws will provide high levels of detail and accuracy.
Speed and Efficiency: Bridge saws excel in high-speed cutting of large slabs, perfect for bulk cutting tasks with basic shapes.
Maintenance and Operating Costs
All machines require some level of maintenance, but it's essential to consider the overall maintenance requirements and operating costs when choosing a machine. Manual cutting machines are the simplest and least costly in terms of upkeep. However, more advanced machines like CNC diamond wire saws or waterjet cutters will require more technical expertise and maintenance, but they provide more functionality and long-term cost savings in terms of productivity and efficiency.
Low Maintenance & Cost: Manual cutters and bridge saws are easier to maintain and have lower operating costs.
Higher Initial Investment & Maintenance: CNC diamond wire saws and waterjet cutters may require more attention but will offer greater long-term returns in terms of functionality and capabilities.
Space and Environmental Considerations
The space available in your stone factory will also influence your decision. Some machines are larger and require more space, such as bridge saws, while others are more compact. For example, manual cutting machines are relatively small and can be more easily integrated into tight spaces, but waterjets and CNC saws may require more room and a stable environment.
Additionally, machines like waterjets require water supply systems and specialized drainage, while bridge saws and CNC machines require proper dust and debris management to maintain an optimal working environment.
Space Limitations: Manual cutters or compact bridge saws can fit into smaller spaces, making them more suitable for smaller workshops.
Environmental Impact: Waterjets produce less dust, but they require water management systems. Bridge saws and manual cutters generate dust, so a dust collection system will be essential for both safety and cleanliness.
Conclusion: Choosing the Right Stone Cutting Machine
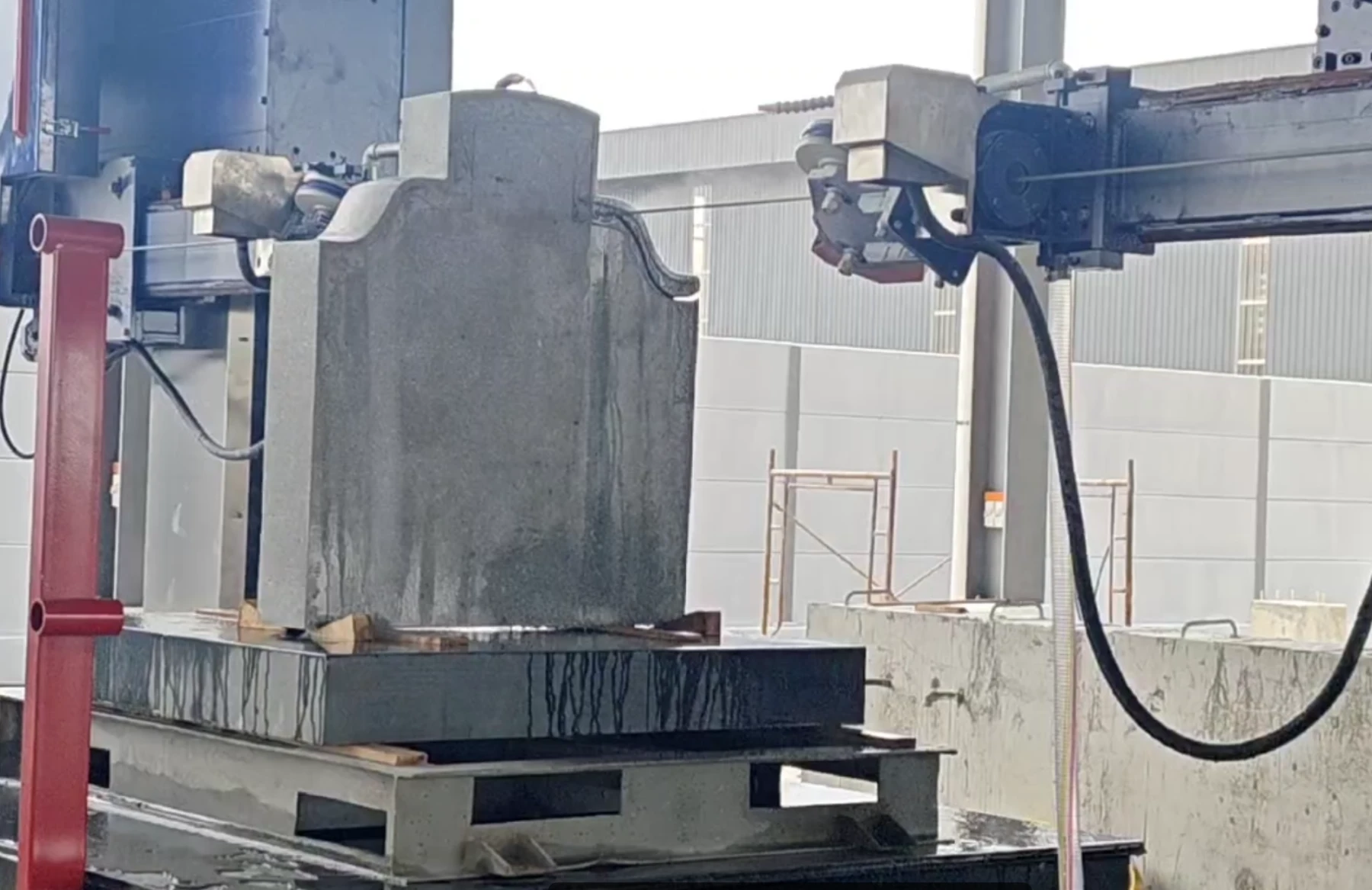
Selecting the right stone cutting machine is crucial for enhancing both the efficiency and quality of your stone processing operations. The ideal machine depends on factors such as the types of materials you process, the complexity of your cuts, production volume, and, of course, your budget. Understanding these variables and matching them to the capabilities of various machines will set your business on a path to higher productivity and better profitability.
Here’s a quick recap of the key considerations:
Understand Your Specific Needs: What types of stones do you cut? Do you need complex shapes or precision? Do you need features like waterjet cutting or CNC control for more customized pieces? Identifying the products you create most often helps narrow down the options.
Match Machine Types to Your Operations: Whether it’s a bridge saw, CNC diamond wire saw, waterjet cutter, or manual cutting machine, each machine offers different advantages. Consider factors like cutting speed, precision, maintenance requirements, and ease of use when selecting.
Balance Between Cost and Performance: It’s easy to get drawn into a machine’s advanced features, but you need to ensure the cost aligns with your budget and expected return on investment (ROI). Consider both initial costs and ongoing operational costs, including maintenance, spare parts, and energy consumption.
Evaluate Financing and Support: If budget is a concern, financing and leasing options may provide a way to access higher-end machines. In addition, selecting a manufacturer or distributor that offers training, technical support, and after-sales service can ensure smooth operations and minimize downtime.
By making an informed decision, you can ensure that your investment in a stone cutting machine enhances the efficiency, accuracy, and scalability of your production process, driving long-term business success.
FAQs
What are the key differences between a CNC diamond wire saw and a bridge saw?
A CNC diamond wire saw is designed for cutting more complex shapes and larger, thicker stone materials, often used for intricate designs, monuments, and sculptures. A bridge saw, on the other hand, excels at cutting straight lines, angles, and slabbing stone, typically used in tile cutting and countertops.
How do I know if I need a waterjet cutting machine?
A waterjet cutting machine is ideal for cutting highly intricate designs and can cut through materials of varying thicknesses, including stone, metal, and glass. If your projects require detailed, customized patterns or thin, precise cuts, a waterjet is an excellent option.
Can I use a manual stone cutting machine for large-scale production?
While manual cutting machines are ideal for smaller operations or individual