
What is Abrasive Water Jet Cutting?
Abrasive water jet cutting is a versatile cold-cutting technology that combines high-pressure water with abrasive particles to precisely cut through virtually any material without heat damage. Using pressures up to 90,000 PSI and abrasives like garnet, this process preserves material integrity while cutting everything from metals and stone to composites.
✅More info of Abrasive Water Jet
How Does Abrasive Water Jet Cutting Work?

High-Pressure Pump | Abrasive Delivery | Cutting Head | Material Cutting |
---|---|---|---|
Creates water pressure | Meters garnet particles into water stream | Contains jewel orifice and mixing tube | Jet strikes at 900+ mph, causing erosion |
What Can Abrasive Water Jet Cutting Do?
Abrasive water jet cutting's unique capabilities have led to its adoption across diverse industries where precision, material integrity, and versatility are critical requirements.
✈️ Aerospace & Defense |
| ||
---|---|---|---|
🏗️ Stone & Architecture |
| ||
🏭 Metal Fabrication |
| ||
⚕️ Medical Devices |
| ||
🔌 Electronics |
| ||
🚗 Automotive |
|
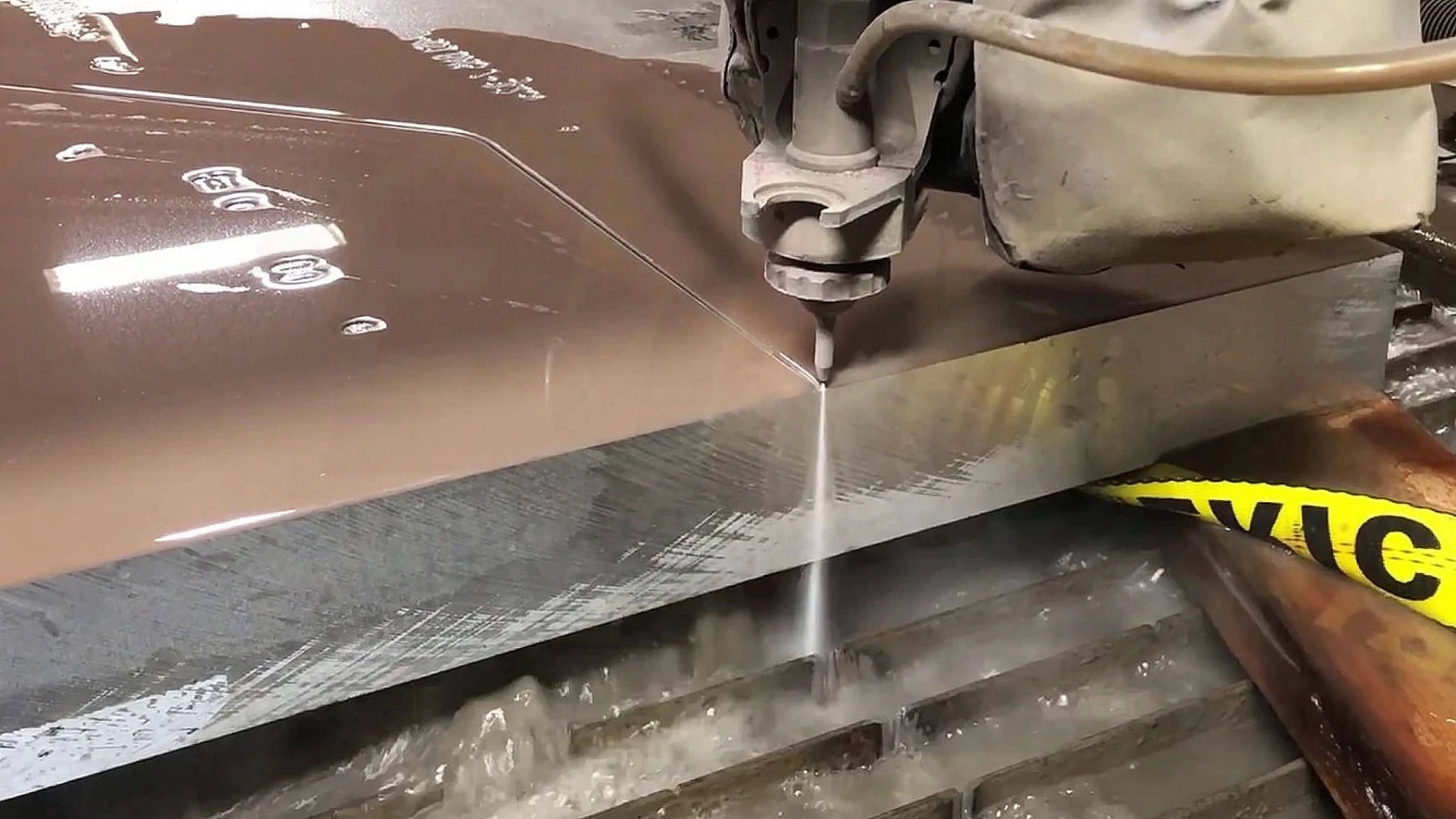
What Are the Benefits of Abrasive Water Jet Cutting?
Abrasive water jet cutting offers significant advantages over conventional cutting methods, making it the preferred choice for applications where precision, versatility, and material integrity are paramount.
❄️ Cold Cutting Process | Generates no heat during operation, preserving the structural integrity and material properties of heat-sensitive materials | ||
---|---|---|---|
📏 Exceptional Precision | Achieves tolerances as tight as ±0.003" (0.075mm) with narrow kerf | ||
🔄 Material Versatility | Cuts virtually any material from soft foam to hardened steel | ||
⚡ Production Efficiency | Eliminates secondary finishing operations like deburring or edge grinding | ||
🌿 Environmental Benefits | Produces no hazardous waste, toxic fumes, or airborne dust | ||
🧩 Design Flexibility | Enables complex geometries and intricate details impossible with conventional cutting methods |
How Does Abrasive Water Jet Compare to Other Cutting Methods?
Abrasive water jet cutting offers distinct advantages and limitations compared to other traditional and modern cutting technologies. Understanding these differences helps determine the most suitable method for your specific applications.
Feature | Abrasive Waterjet | Laser Cutting | Plasma Cutting | CNC Milling |
---|---|---|---|---|
Heat Affected Zone | None | Minimal | Significant | Minimal (heat from friction) |
Material Thickness | Up to 12" (300mm) | Up to 1" (25mm) for metals | Up to 6" (150mm) | Unlimited (multiple passes) |
Cutting Speed | Slow to moderate | Fast for thin materials | Very fast | Moderate |
Material Versatility | Nearly all materials | Limited with reflective/transparent materials | Conductive metals only | Most materials except very brittle |
Surface Finish | Good to excellent, smooth | Excellent, may need minimal finishing | Rough, requires finishing | Excellent, depends on tooling |
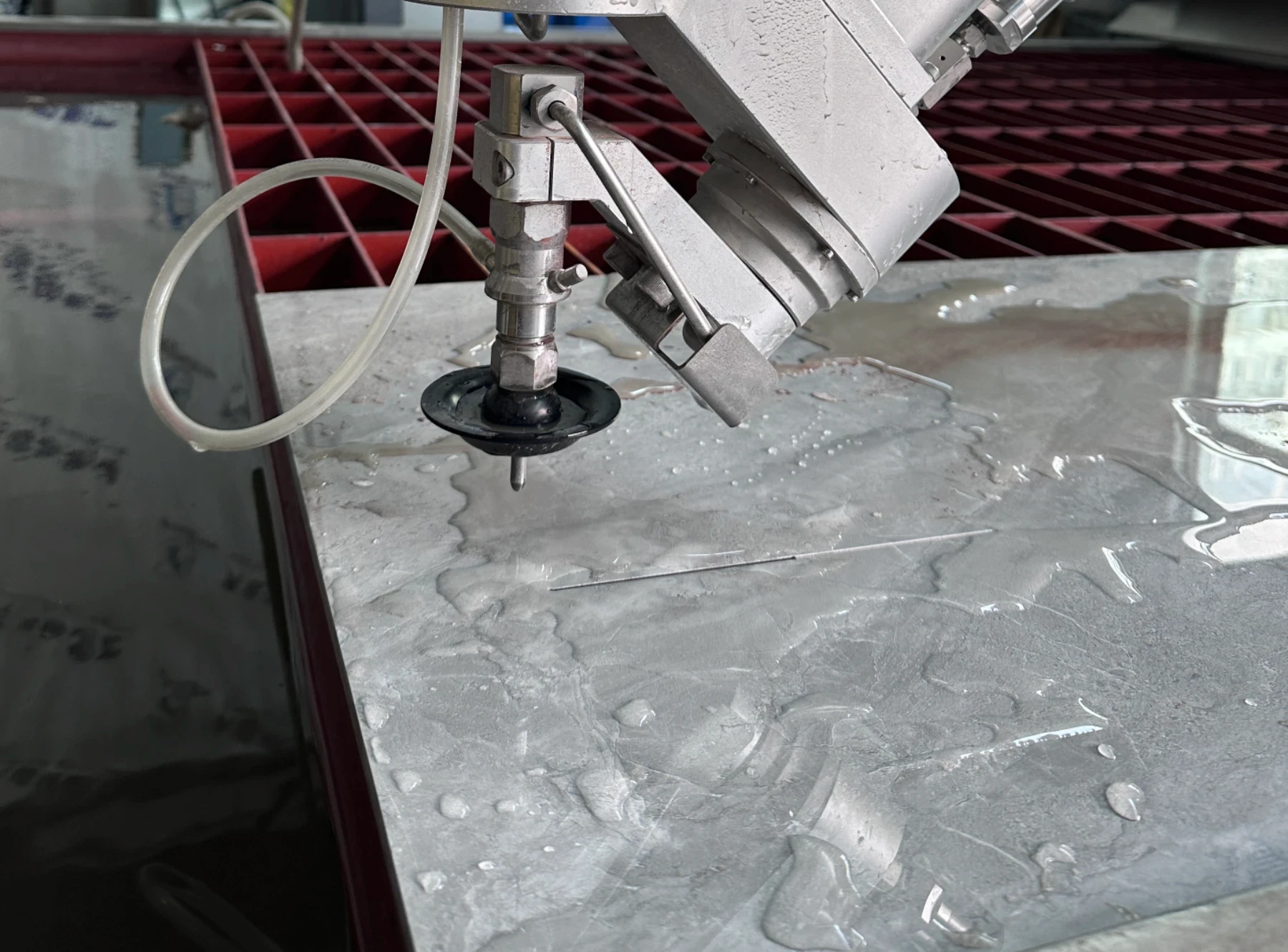
What's the Difference Between Abrasive and Pure Water Jet Cutting?
Understanding the differences between abrasive and pure water jet cutting is essential for selecting the right process for your specific application needs.
Feature | Pure Water Jet | Abrasive Water Jet | ||
---|---|---|---|---|
Cutting Mechanism | Water pressure alone | Water pressure + abrasive particles | ||
Suitable Materials | Soft materials (foam, rubber, food, paper) | Hard materials (metals, stone, glass, ceramics) | ||
Cutting Power | Lower (limited to materials under 1" thick) | Higher (can cut materials up to 12" thick) | ||
Precision | Very high (±0.001" tolerance) | High (±0.003 - 0.005" tolerance) | ||
Operating Cost | Lower (no abrasive consumption) | Higher (requires abrasive media) |
Which Abrasives Are Best for Water Jet Cutting?
The choice of abrasive significantly impacts cutting performance, surface finish quality, and operating costs.
Common Abrasive Materials | Particle Size Impact |
---|---|
|
|
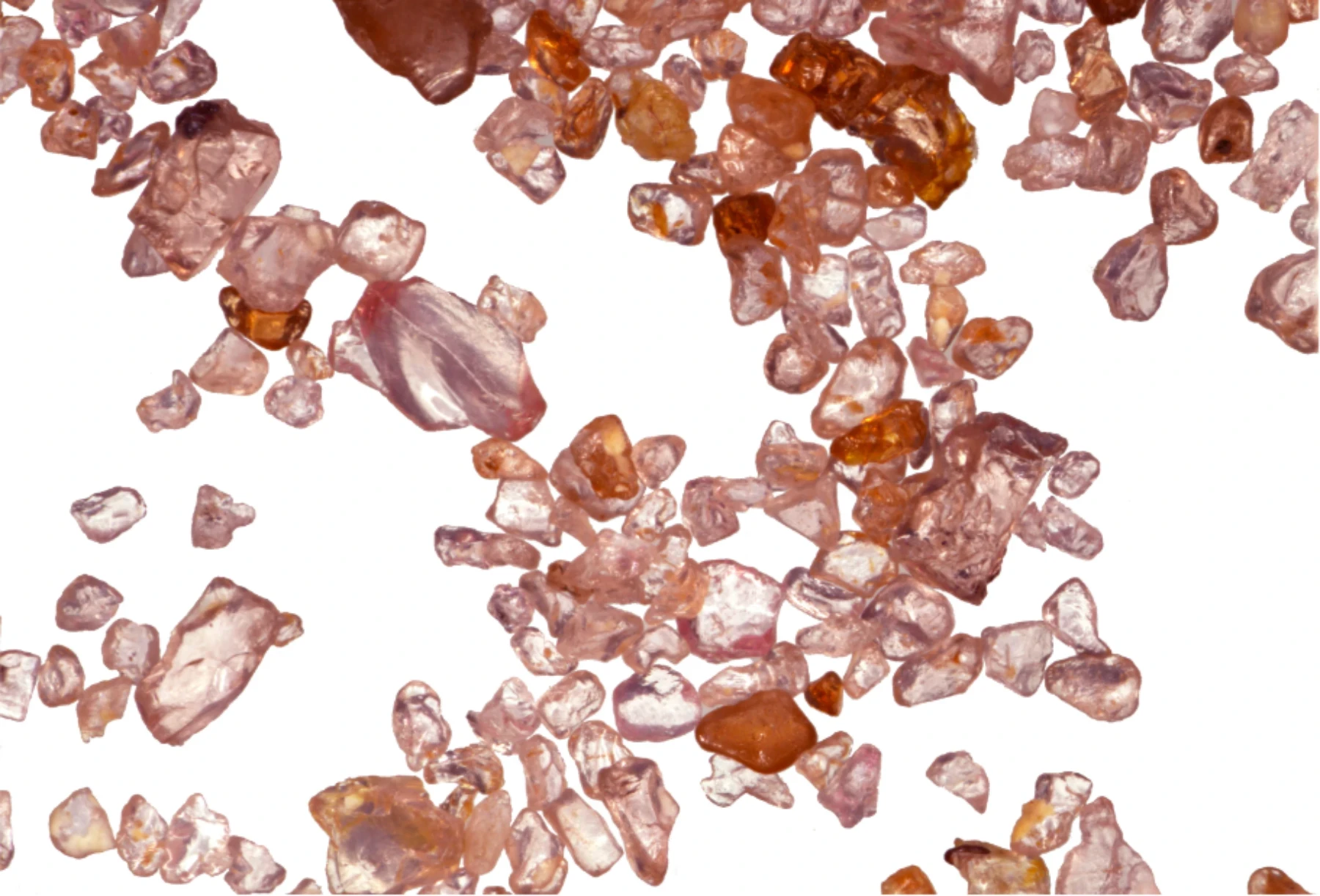
What Should You Consider When Choosing Abrasive Water Jet Equipment?
When selecting abrasive water jet technology, consider both equipment capabilities and potential challenges to ensure optimal performance for your specific applications:
🔧 Pump Systems |
| ||
---|---|---|---|
📊 Control Systems |
| ||
💰 Cost Management | Abrasives typically account for 50-70% of operating costs. Consider recycling systems that can reduce expenses by up to 50%, according to industry research. | ||
⏳ Performance Considerations | For thin materials, cutting speeds are slower than thermal methods. Research indicates speed decreases with material thickness. Balance production requirements with machine capabilities. | ||
🔄 Cutting Quality | Water jets naturally create a V-shaped kerf that widens toward the exit side. Advanced systems feature dynamic compensation that minimizes taper, resulting in straighter edges and tighter tolerances. |
Understanding both technical capabilities and operational challenges helps organizations maximize their investment in abrasive water jet technology. DINOSAW experts can help evaluate your specific cutting needs and recommend optimal configurations.
Ready to Explore Abrasive Water Jet Cutting?
Conclusion & Next Steps
Abrasive water jet cutting offers unmatched versatility for processing diverse materials without heat distortion. Its ability to maintain material integrity while achieving high precision makes it invaluable across numerous industries.
Key Takeaways
Cold cutting process preserves material properties and prevents thermal distortion.
Exceptional versatility handles materials from soft rubber to hardened steel and stone.
Precise cutting capabilities with minimal kerf width and tight tolerances.
Environmentally friendly process with no toxic fumes or hazardous waste.
Contact DINOSAW's experts today for personalized advice, sample cuts, and equipment recommendations.
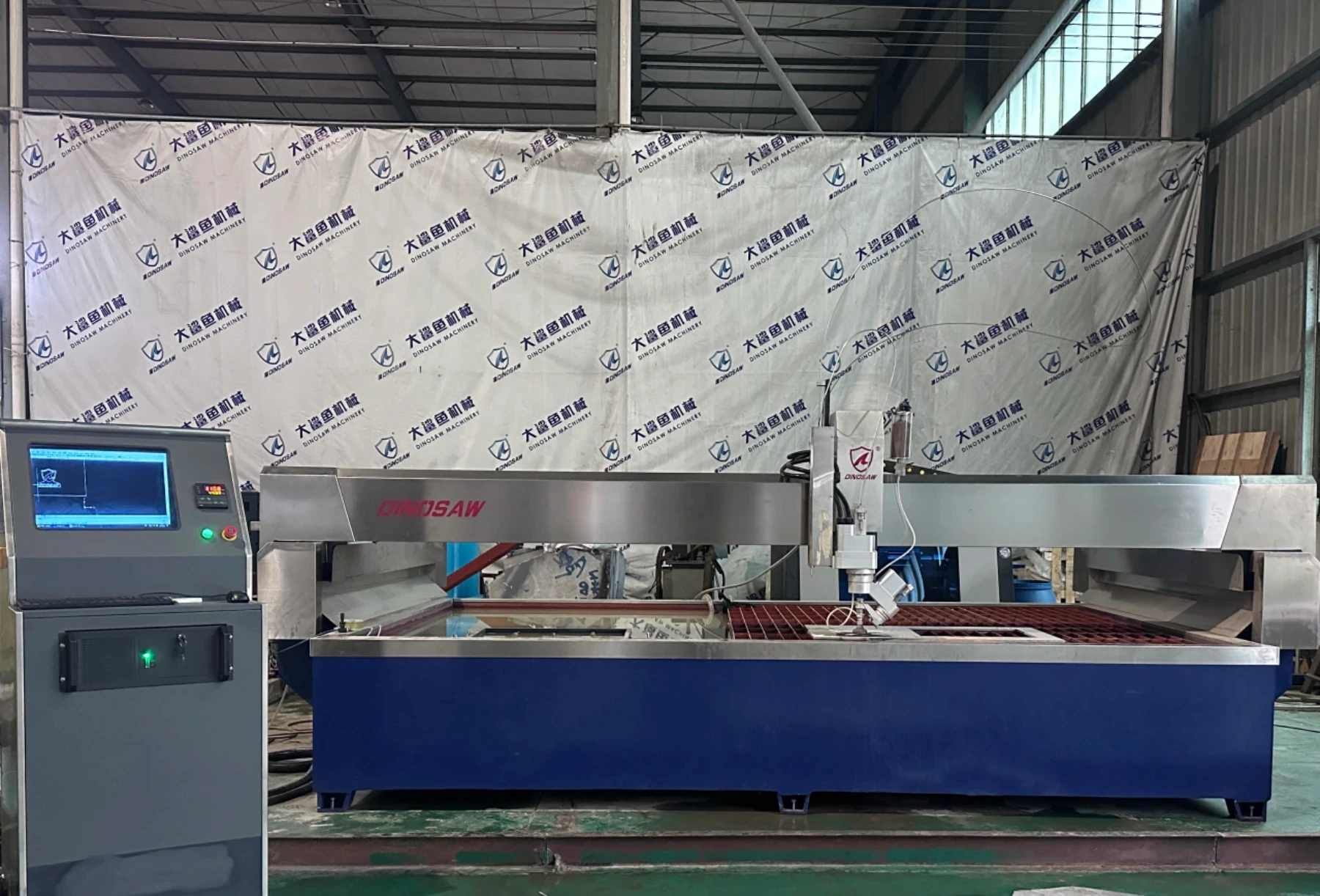
Frequently Asked Questions
What materials can abrasive water jet cutting handle?
Abrasive water jet cutting can process a wide range of materials, including metals (steel, aluminum, titanium), stone (marble, granite), glass, ceramics, composites (carbon fiber, fiberglass), and more.
How does abrasive water jet cutting differ from pure water jet cutting?
Pure water jet cutting uses only high-pressure water and is ideal for soft materials like foam, rubber, and food products. Abrasive water jet cutting incorporates abrasive particles like garnet, enabling it to cut harder and thicker materials with precision.
Why is garnet the most popular abrasive for water jet cutting?
Garnet is preferred for its optimal hardness, sharp edges, and recyclability. It offers a balance of cutting speed, edge quality, and low wear on equipment, making it cost-effective and efficient.
Is abrasive water jet cutting environmentally friendly?
Yes, it is an eco-friendly process that generates minimal waste, uses recyclable abrasives, and produces no harmful emissions or heat-affected zones.
What should I consider when buying an abrasive water jet machine?
Key factors include the machine’s capabilities (e.g., multi-axis cutting), the quality and availability of abrasives, after-sales support, and the reputation of the manufacturer, such as DINOSAW.