
Overview of Wire Saw Machine Parts
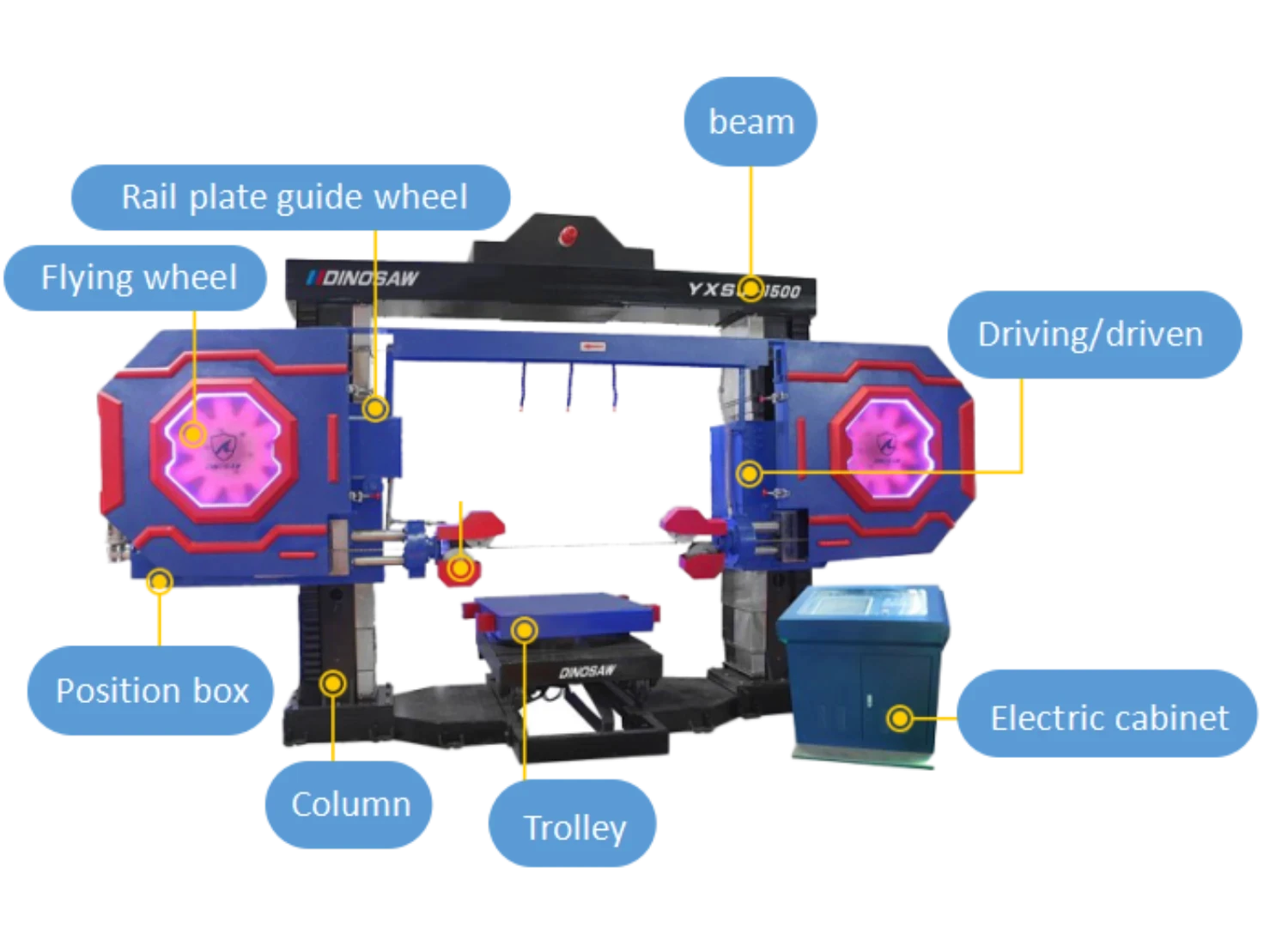
Wire Saw Machine Maintenance area 1. Positioning box
1.1 Guide wheel box
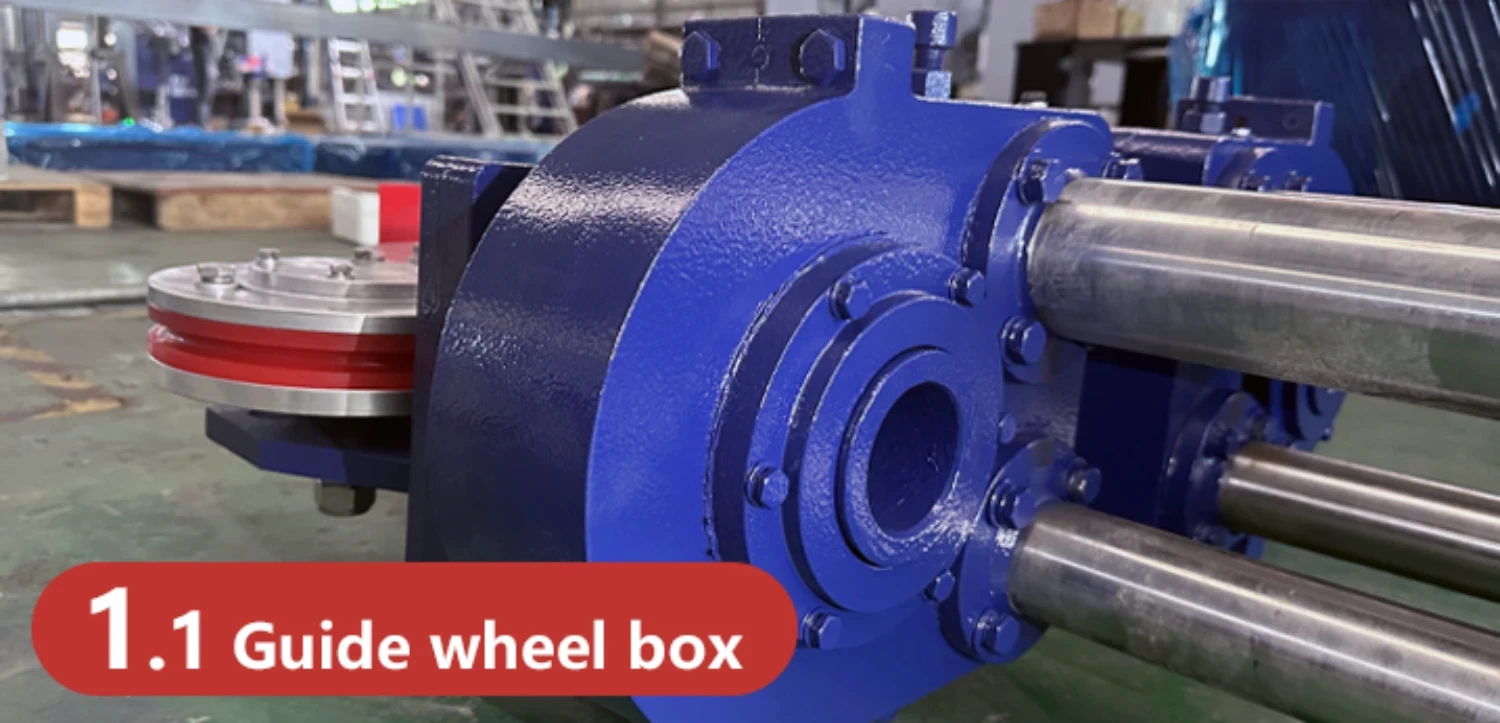
Maintenance frequency:3 months
Maintenance method:Clean mud & dust, add grease(Auto)
Maintenance reason(Detailed description):When the diamond wire rotates, water and mud will be brought into the guide wheel box and adhered to the gears. These water and mud will harden after drying, causing the gears to gradually tighten, and finally cause the AB guide wheels to stuck.
1.2 Screw rod(middle)
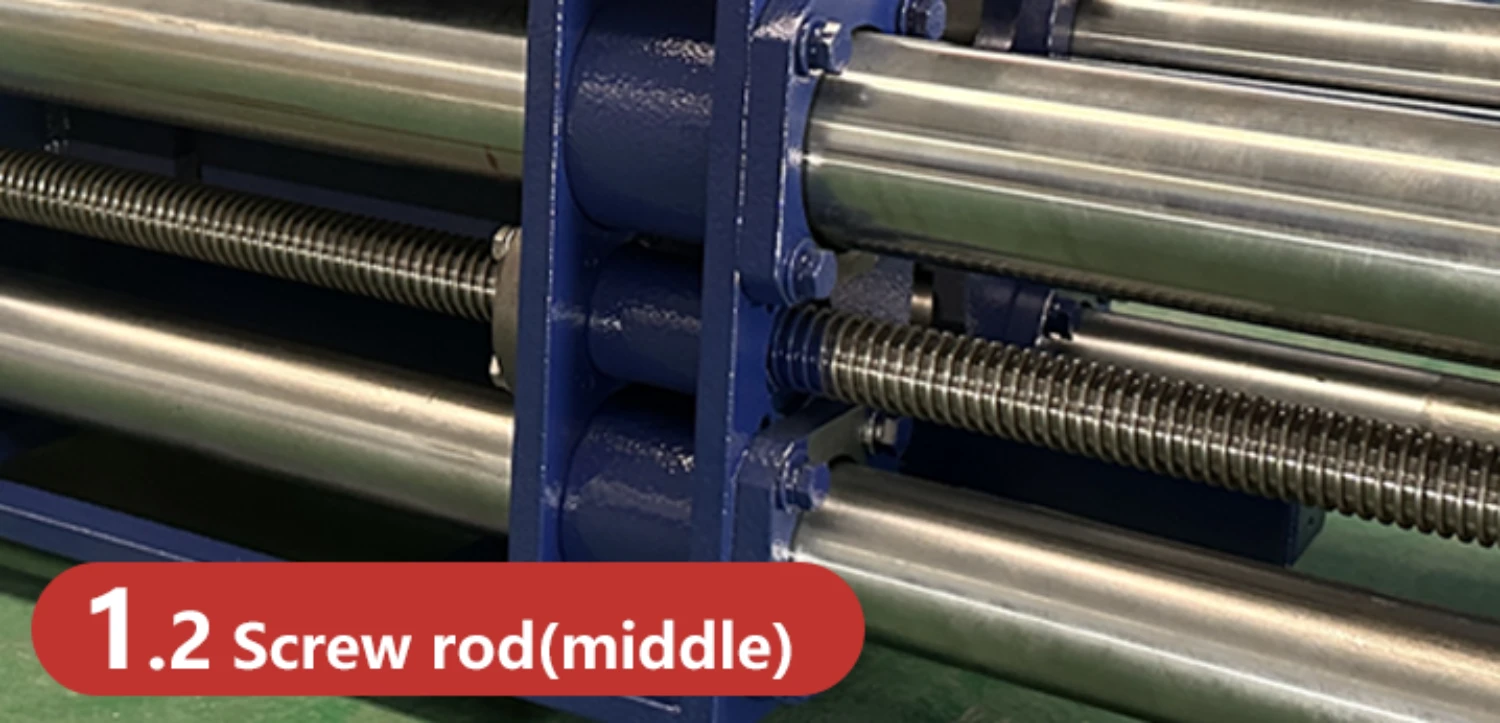
Maintenance frequency:1 month
Maintenance method:Clean mud & dust, add grease
Maintenance reason(Detailed description):
When the diamond wire rotates, water and mud will be brought to the screw rod, stone & sand will gradually tighten the screw rod after hardening, eventually causing the screw rod to get stuck and causing serious losses.
1.3 Polished rod
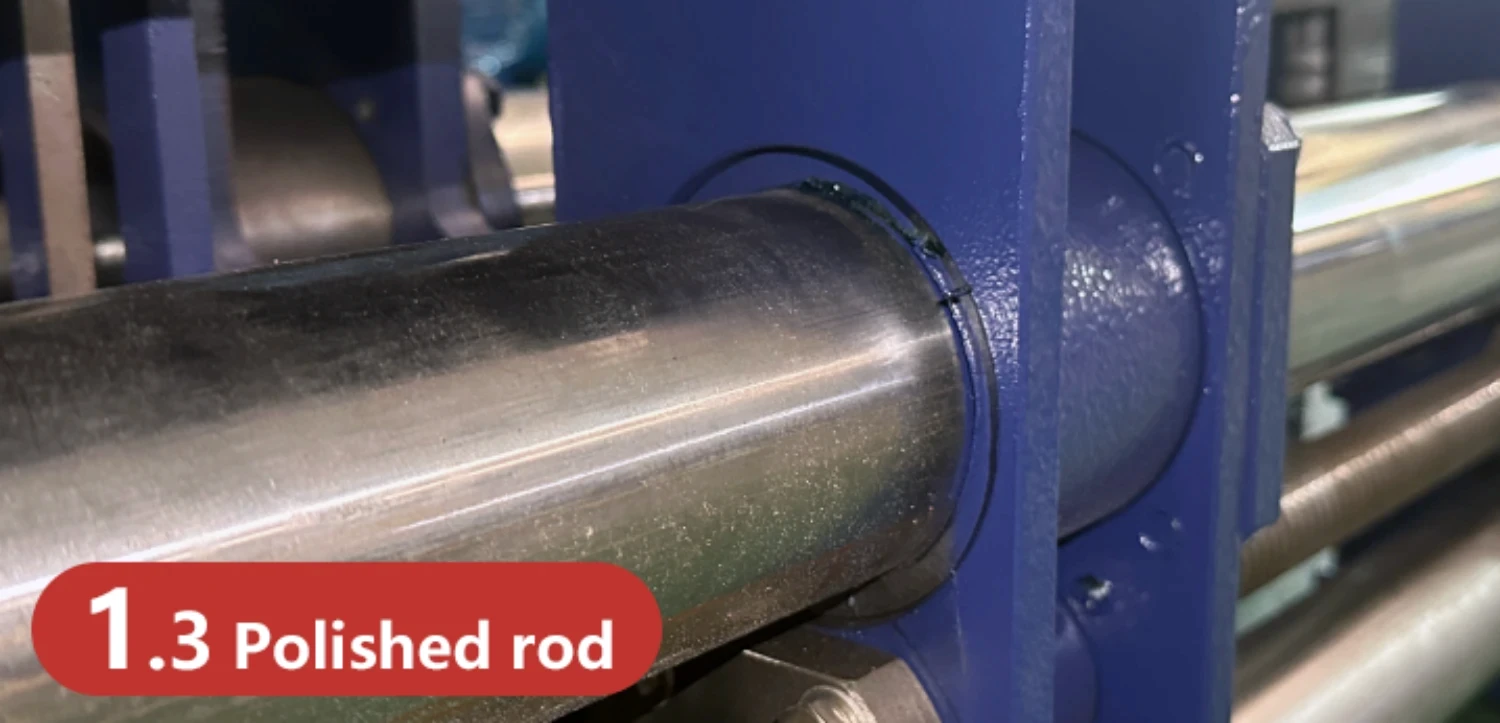
Maintenance frequency:day
Maintenance method:Clean mud & dust, add engine oil
Maintenance reason(Detailed description):When the diamond wire rotates, water will be splashed on the connection between the polished rod and the bearing, which will easily cause the plane bearing to rust, furthermore cause the polished rod to be stuck and cannot stretch.
1.4 Decelerator

Maintenance frequency:3 months
Maintenance method:Add engine oil
Maintenance reason(Detailed description):When the decelerator is running, it may continue to consume engine oil. If oil contains impurities and deterioration is used, the lubrication degree will reduce, and the friction and wear of gears will be increased, which will lead to the problems of gear teeth hitting and inaccurate operation.
1.5 Guide wheel(not include rubber ring)
1.6 Position box whole set
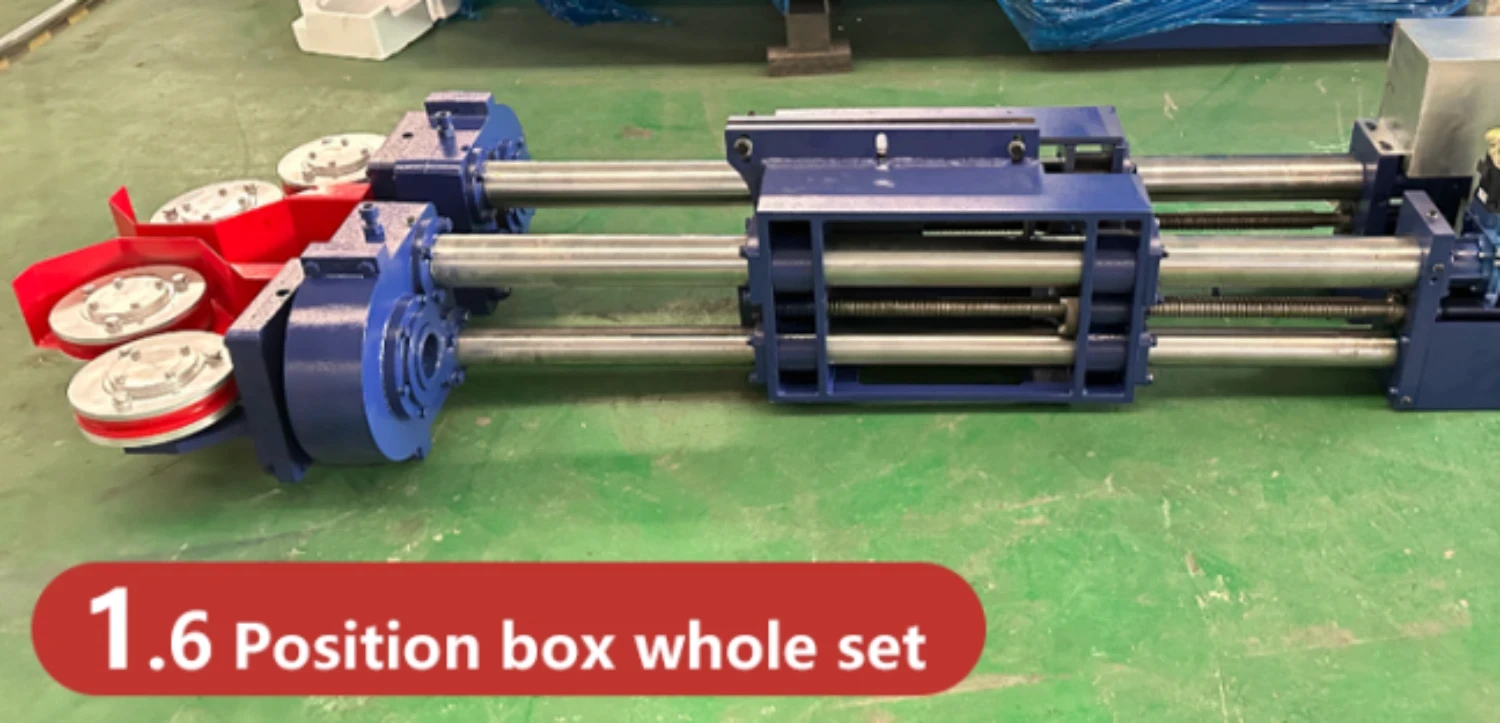
Maintenance frequency:3 months
Maintenance method:Calibration center distance
Maintenance reason(Detailed description):After continuous high-intensity operation of the positioning box, each component may deteriorate, which will affect the cutting accuracy. In order to ensure that the cutting accuracy is controlled within 1 mm, it is necessary to conduct a complete inspection and debugging of the entire set of positioning boxes on a regular basis.
Wire Saw Machine Maintenance area 2. Cross beam/column
2.1 Driven shaft-bearings
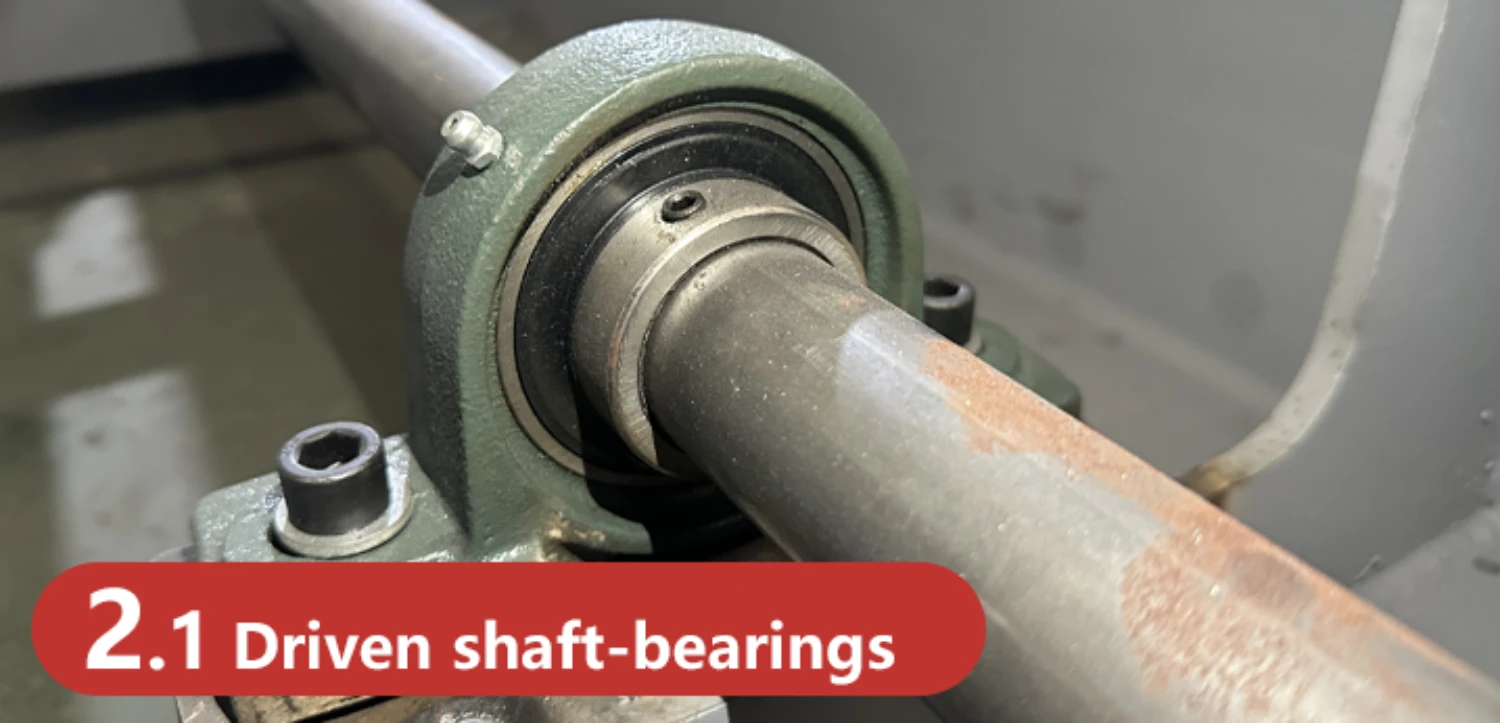
Maintenance frequency:3-6 months
Maintenance method:Tighten the screws and add grease
Maintenance reason(Detailed description):During machine operation, due to water vapor penetration and long-term lack of maintenance, problems such as screw loosing and rust may occur. Especially the bearings on machine top are often difficult to find in time. It will lead to increased transmission torque and increased load on the motor, which will affect machine performance.
2.2 Driving/driven box
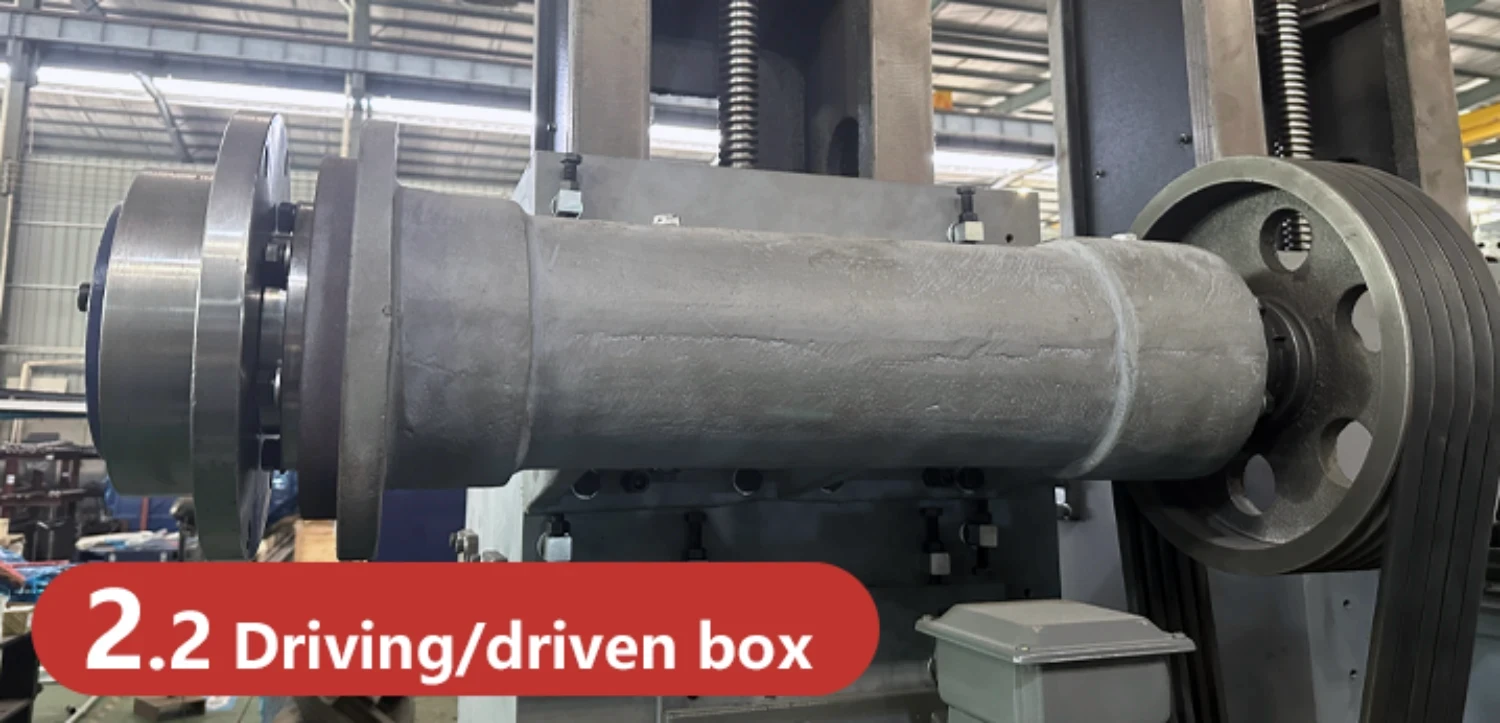
Maintenance frequency:3-6 months
Maintenance method:Gear oil/engine oil adding
Maintenance reason(Detailed description):The main shaft box is a complex and important part. If suitable gear oil is not added regularly, it will lead to function deterioration of main shaft box starting/braking/shifting/reversing and the increase of the motor load, which will affect machine performance.
2.3 Decelerator
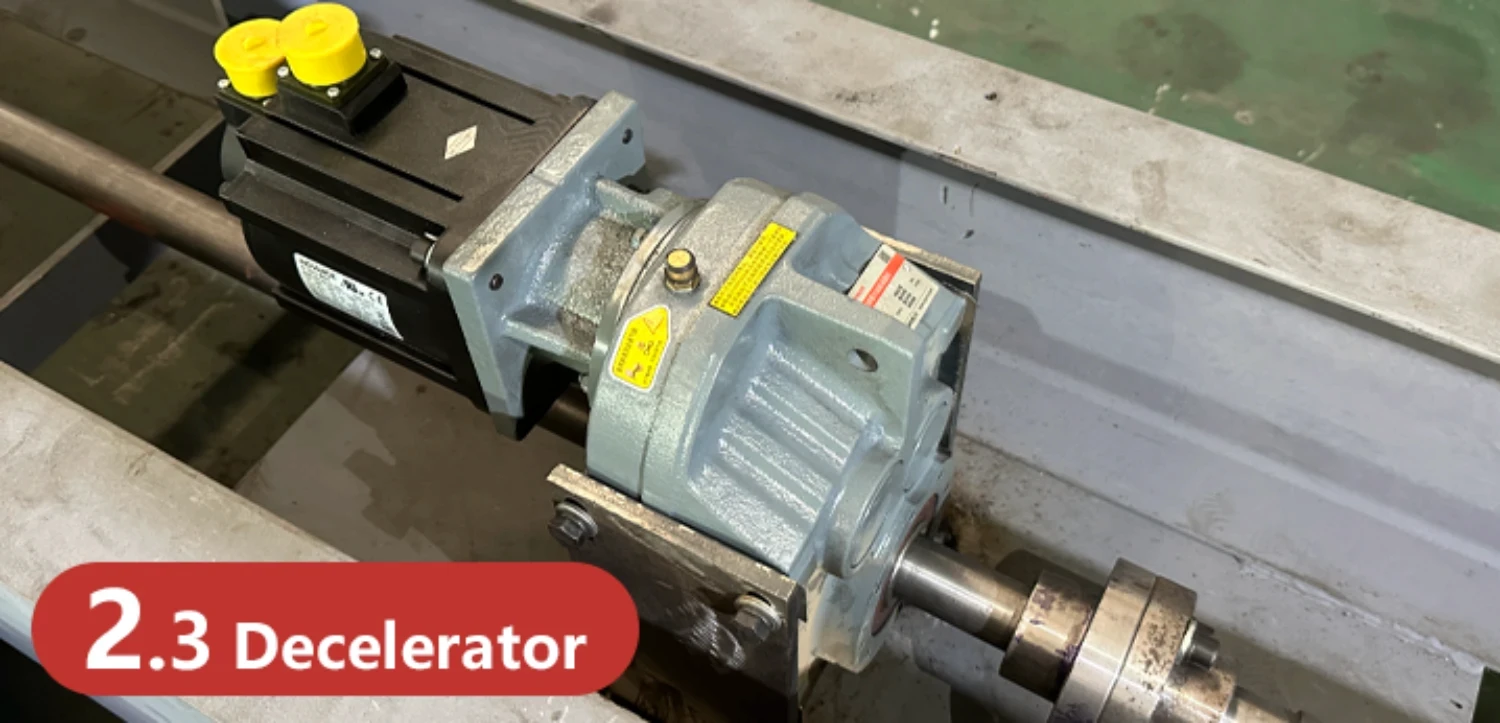
Maintenance frequency:3-6 months
Maintenance method:Grease adding
Maintenance reason(Detailed description):When the decelerator is running, it may continue to consume engine oil or suffer impurity pollution or oil deterioration, which reduces lubrication degree, furthermore it will causes problems of gear teeth hitting and inaccurate running.
2.4 Bevel gear seat
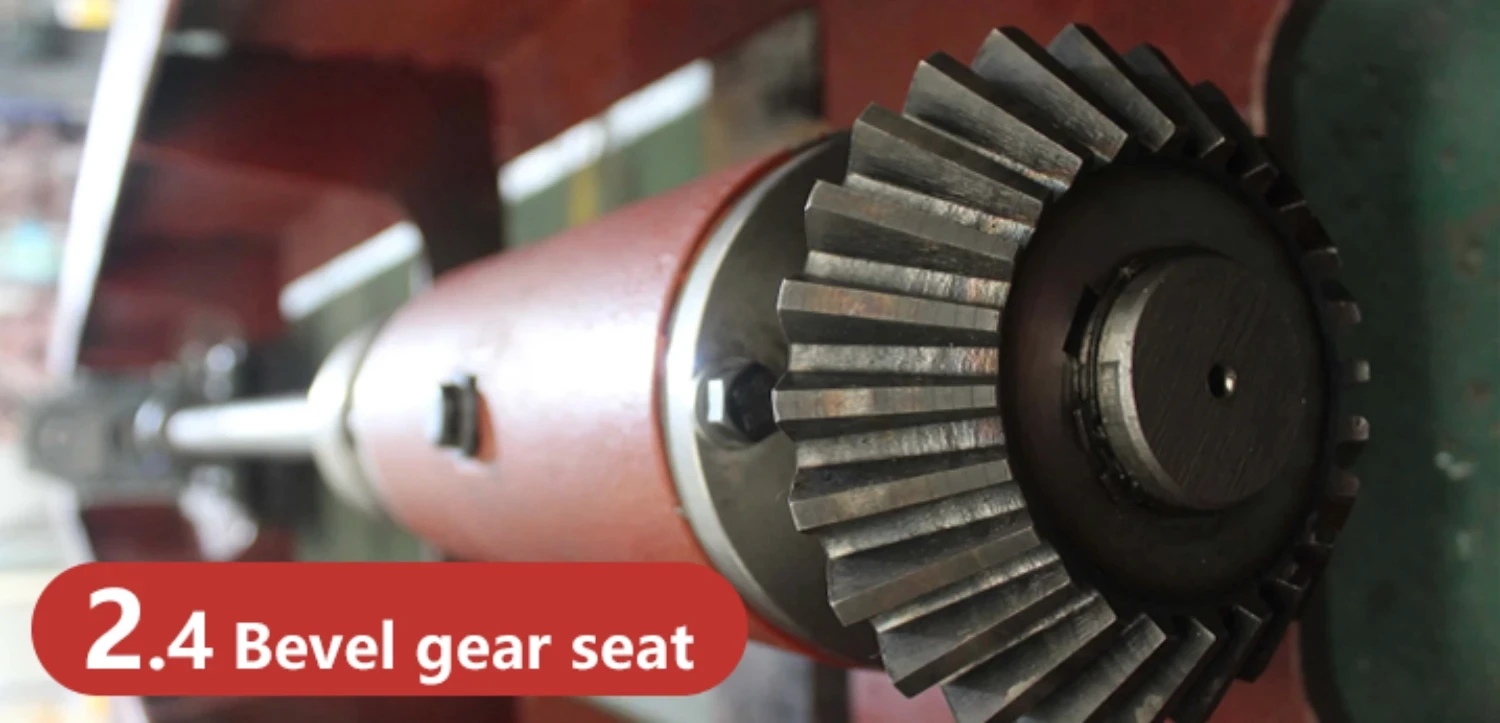
Maintenance frequency:3 months
Maintenance method:Adjust gap, add grease
Maintenance reason(Detailed description):During the operation of the bevel gear seat, the continuous consumption of engine oil or the mixing of impurities in enginee oil will lead to a decrease in lubrication degree and an increase in gap deviation, which is likely to cause gear teeth hitting.
2.5 Lifting screw nut
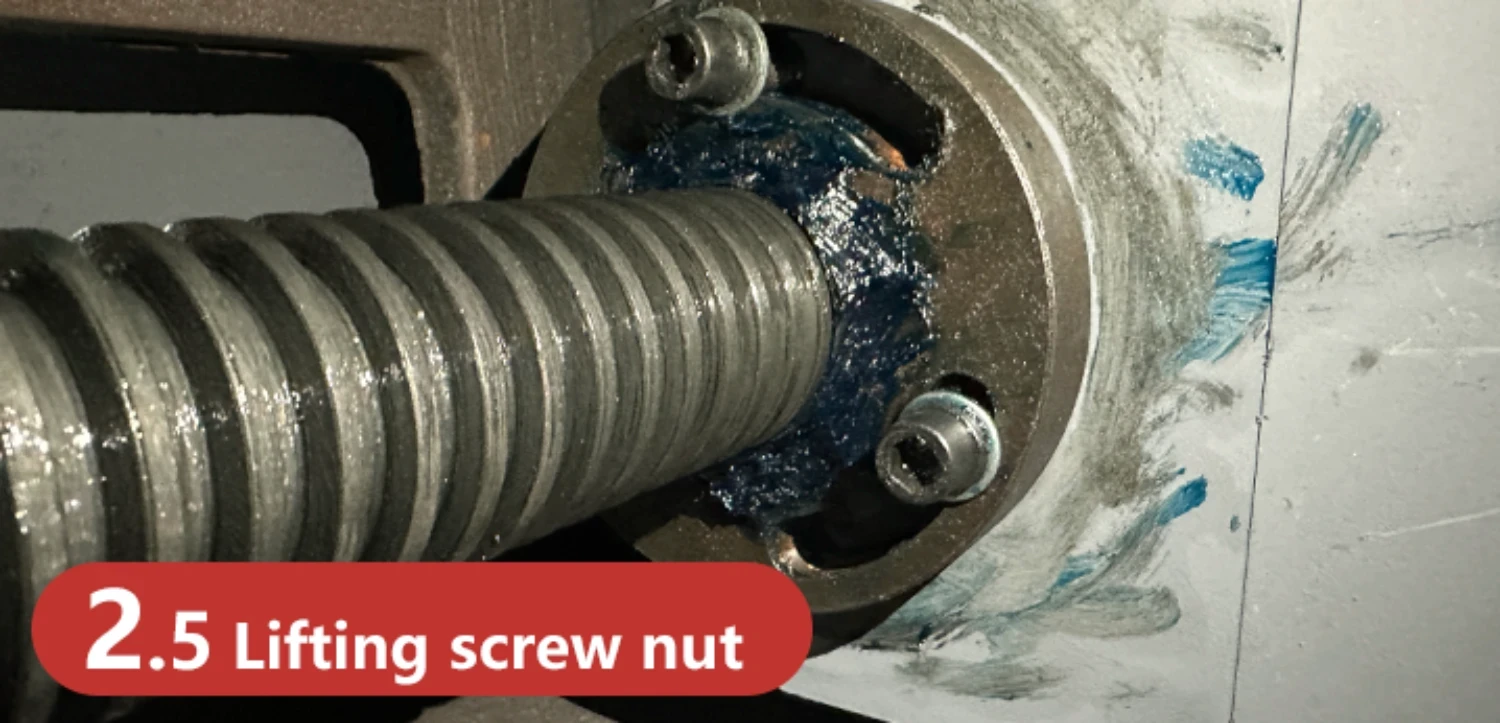
Maintenance frequency:3 months
Maintenance method:Adjust gap, add grease
Maintenance reason(Detailed description):The lifting screw rod will consume grease during long-term running, reducing the lubrication effect. At the same time, since the space where the lifting screw rod is located is relatively sealed, impurities are easy to accumulate in the gap between t nut and screw, which may cause problems such as screw rod trigger an alarm from the servo. In severe cases, the screw rod may be deformed.
2.6 Lubrication device
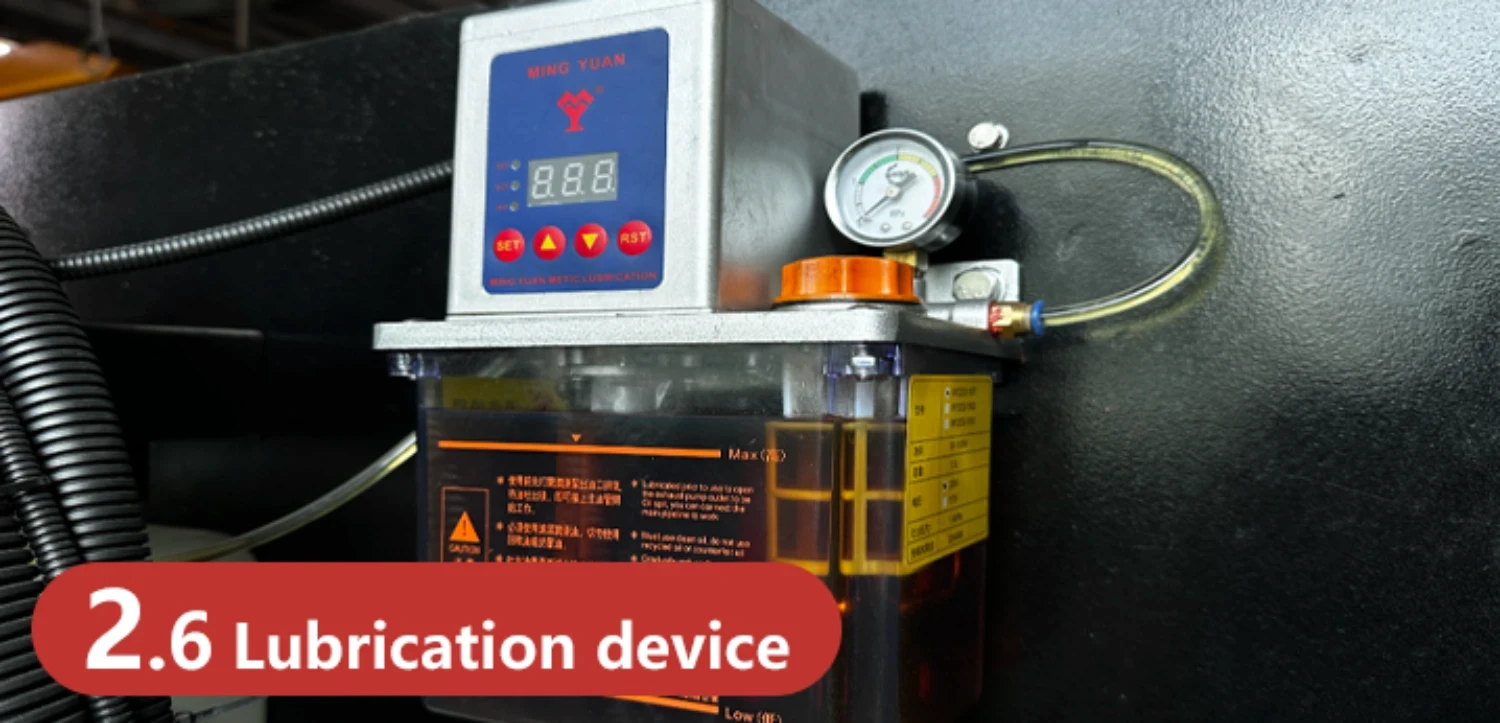
Maintenance method:Check oil pipe, oil circuit regulation flow, refueling (timing)
Wire Saw Machine Maintenance area 3. Trolley
3.1 Roller wheel
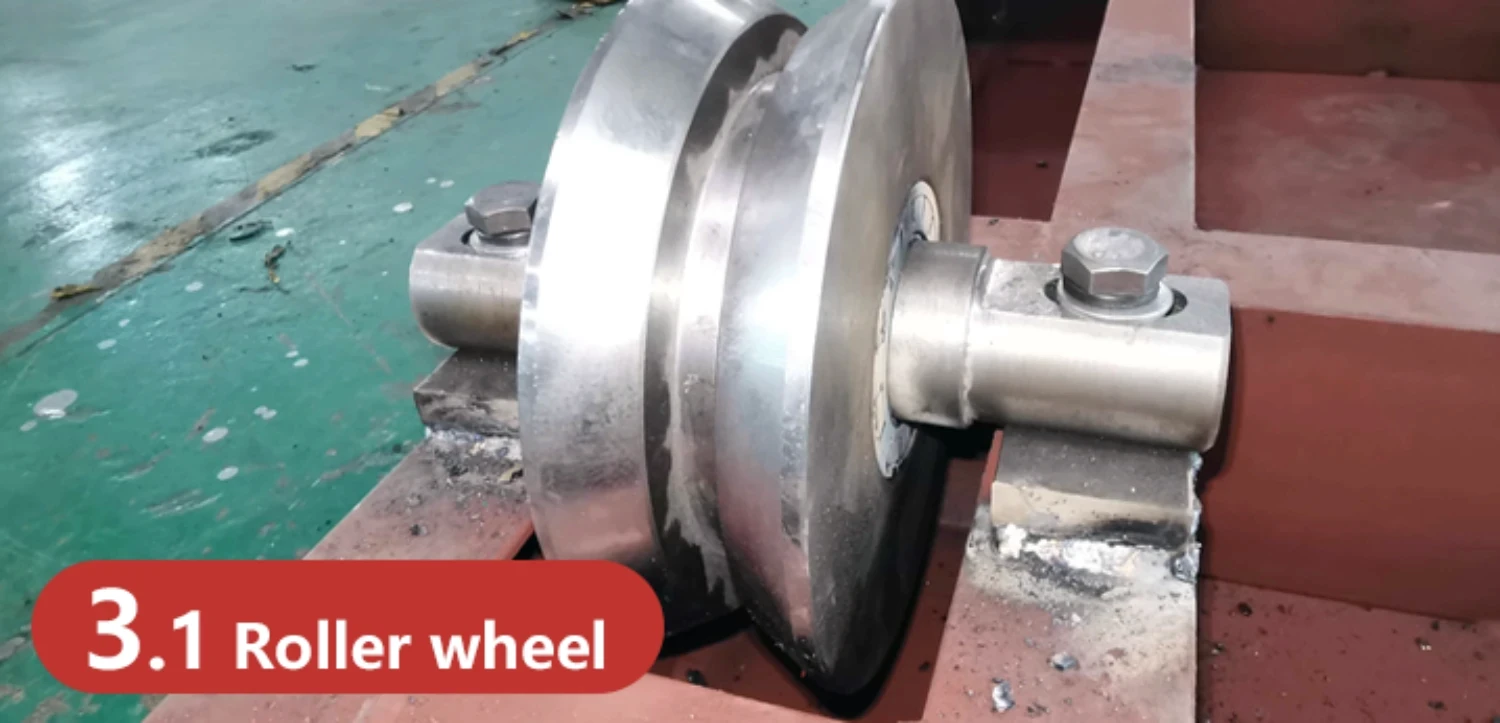
Maintenance frequency:3 months
Maintenance method:Bearing rust removal
Maintenance reason(Detailed description):Because the trolley is close to ground and is easily affected by water immersion, so the bearings, screw nuts and positioning seats in the trolley rollers are prone to rust. Meanwhile the trolley running will increase the load on the motor, and the forced operation may cause damage to the screw nuts and trigger an alarm from the servo.
3.2 Screw rod position seat
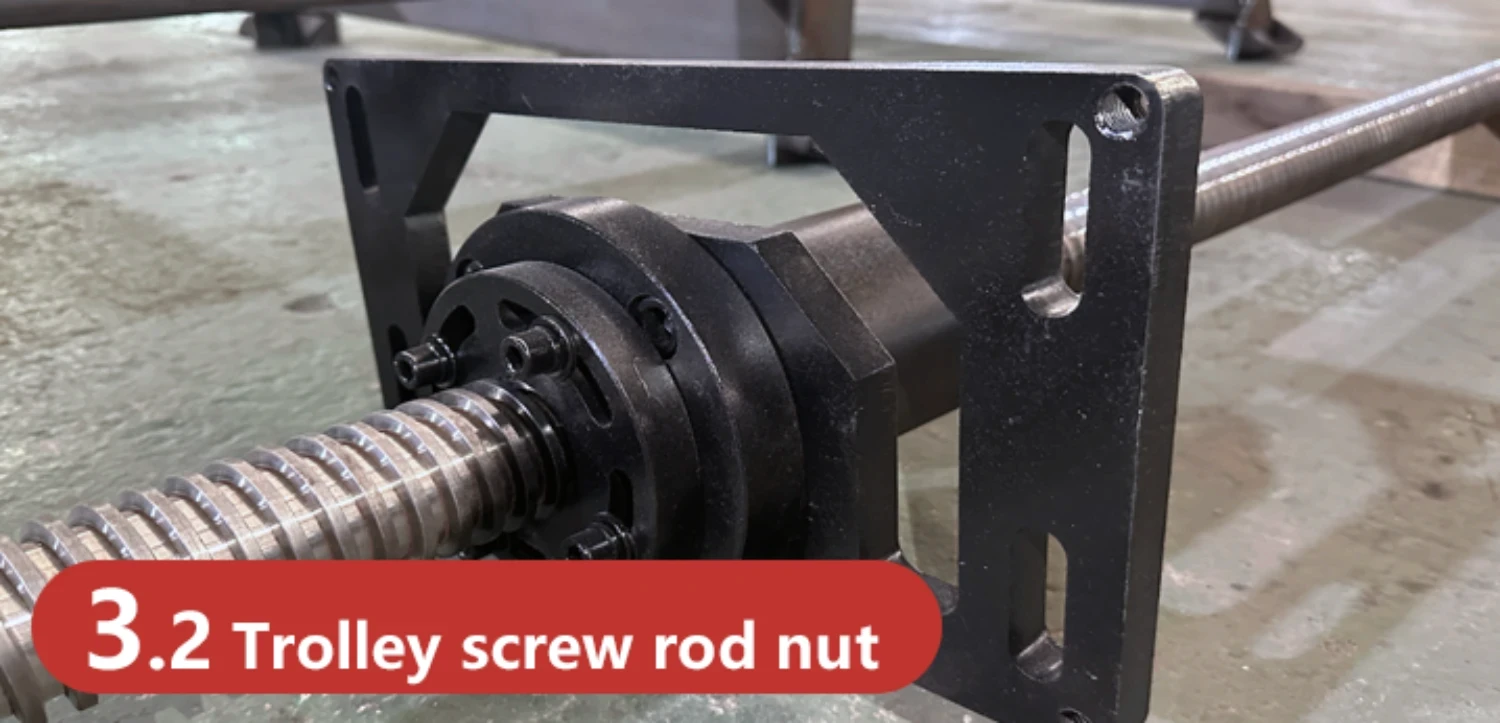
Maintenance frequency:1 week~1 month
Maintenance method:
Rust removal、grease adding
Maintenance reason(Detailed description):During the operation of the bevel gear seat, the continuous consumption of engine oil or the mixing of impurities in enginee oil will lead to a decrease in lubrication degree and an increase in gap deviation, which is likely to cause gear teeth hitting.
3.3 trolley decelerator
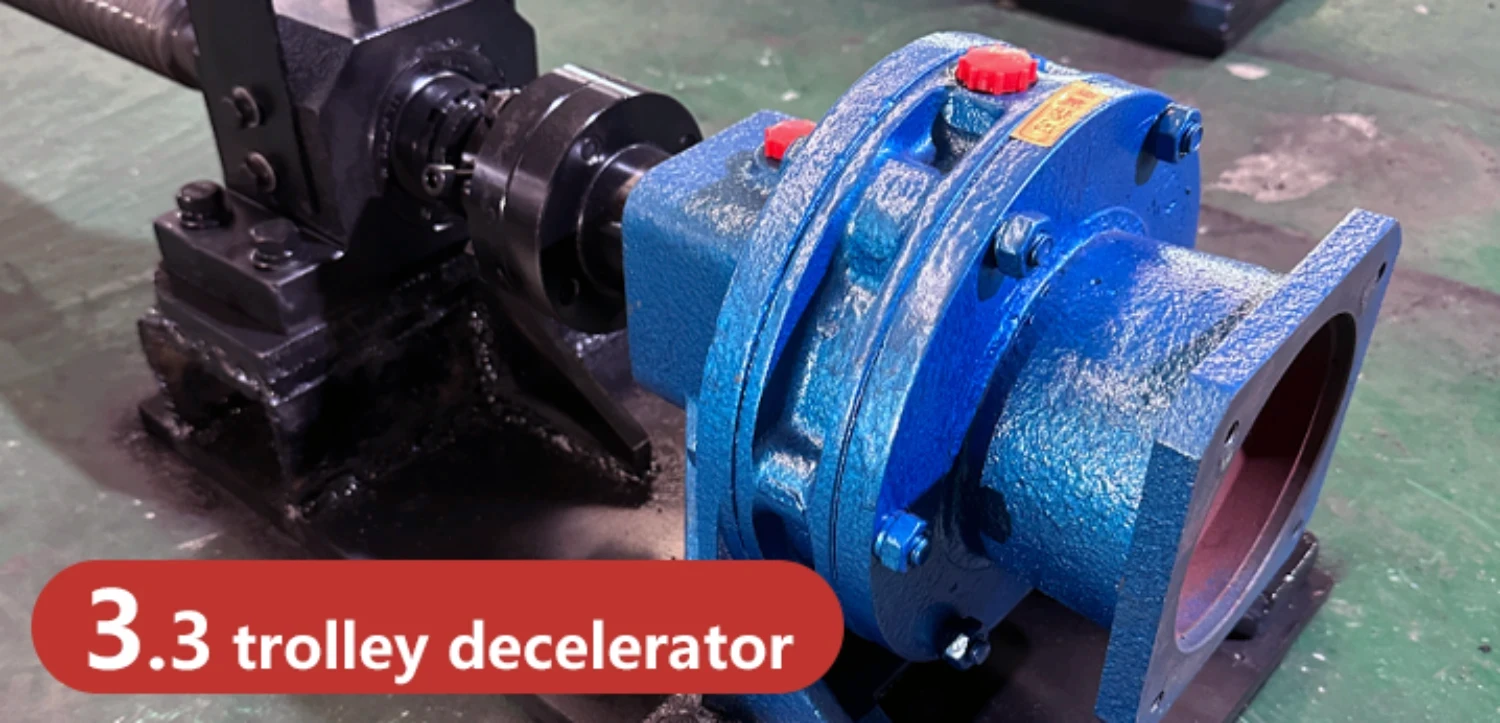
Maintenance frequency:3 months
Maintenance method:
Engine oil adding
Maintenance reason(Detailed description):When the decelerator is running, it may continue to consume engine oil or suffer impurity pollution or oil deterioration, which reduces lubrication degree, furthermore it will causes problems of gear teeth hitting and inaccurate running.
3.4 Gear plate (rotary trolley)
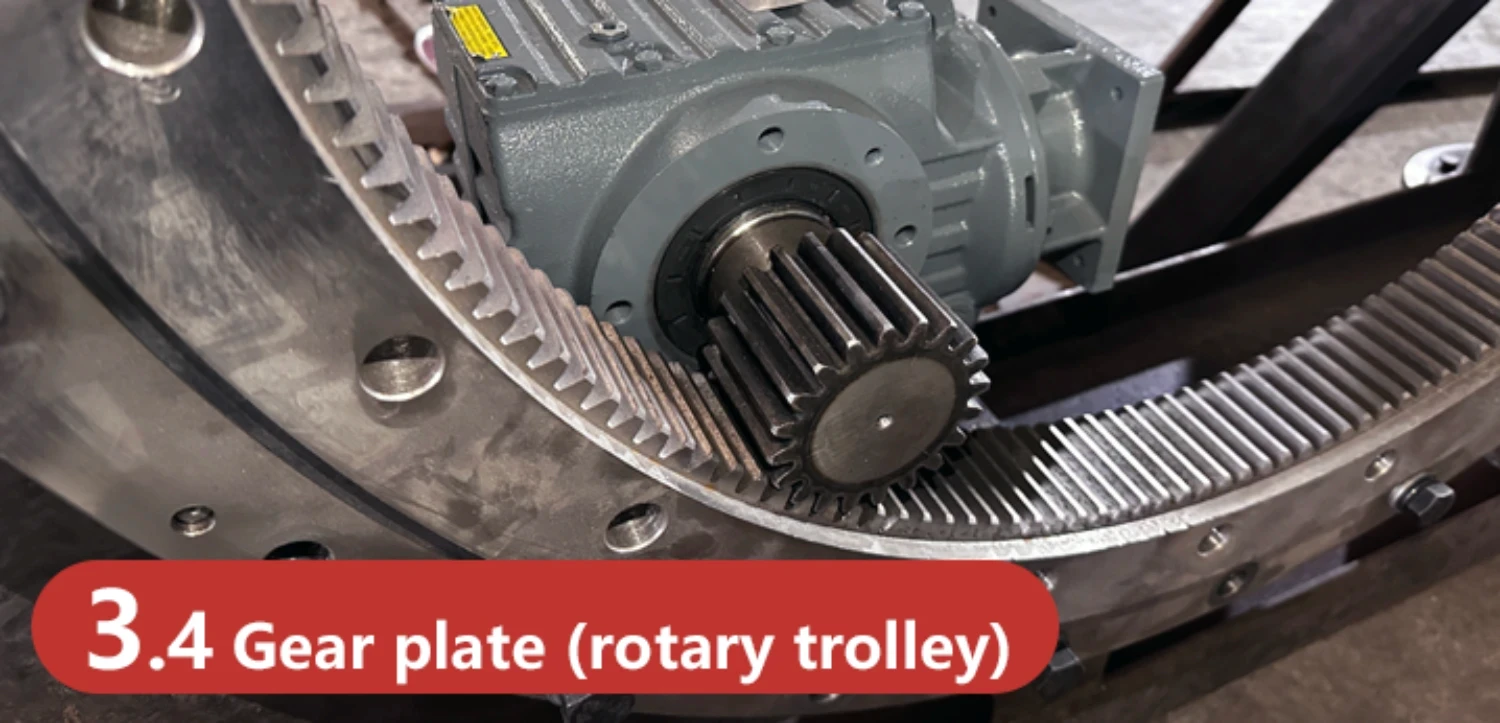
Maintenance frequency:3~6 months
Maintenance method:
Grease adding
Maintenance reason(Detailed description):During gear plate running, continuous consumption of grease or impurities are mixed in the grease will result in lubrication degree decreased. This will increase the motor load on whoel machine when the trolley is running, and cause the trolley to stuck in severe cases.
Wire Saw Machine Maintenance area 4. Square box
4.1 Stand column box rail
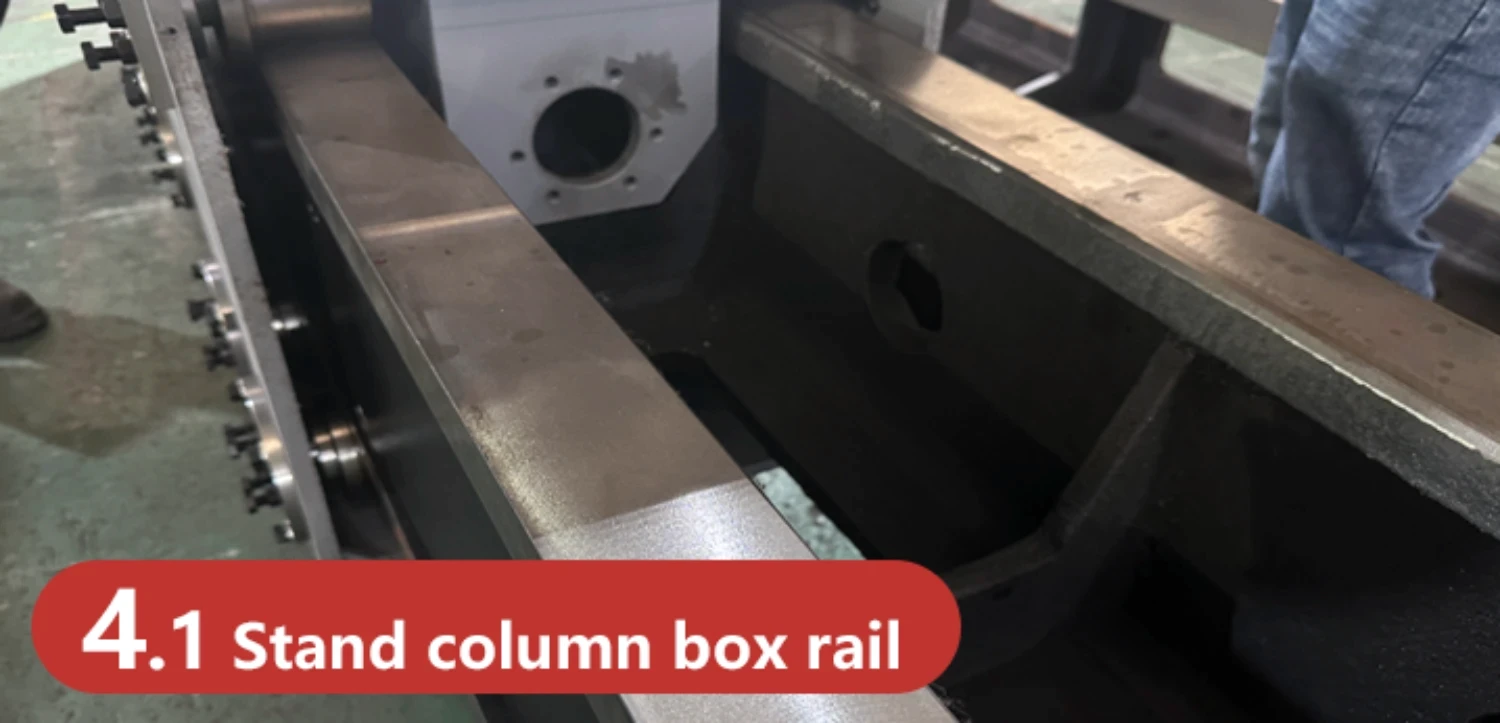
Maintenance frequency:3~6 months
Maintenance method:Rail mud clean
Maintenance reason(Detailed description):The cutting distance between the rail surface of the driving/driveAn box and the stone is close, thus dust is easy to adhere to. When running up and down, the friction increases, thereby increasing the motor load on whole machine.
4.2 Linear guide wheel / rail plate guide wheel
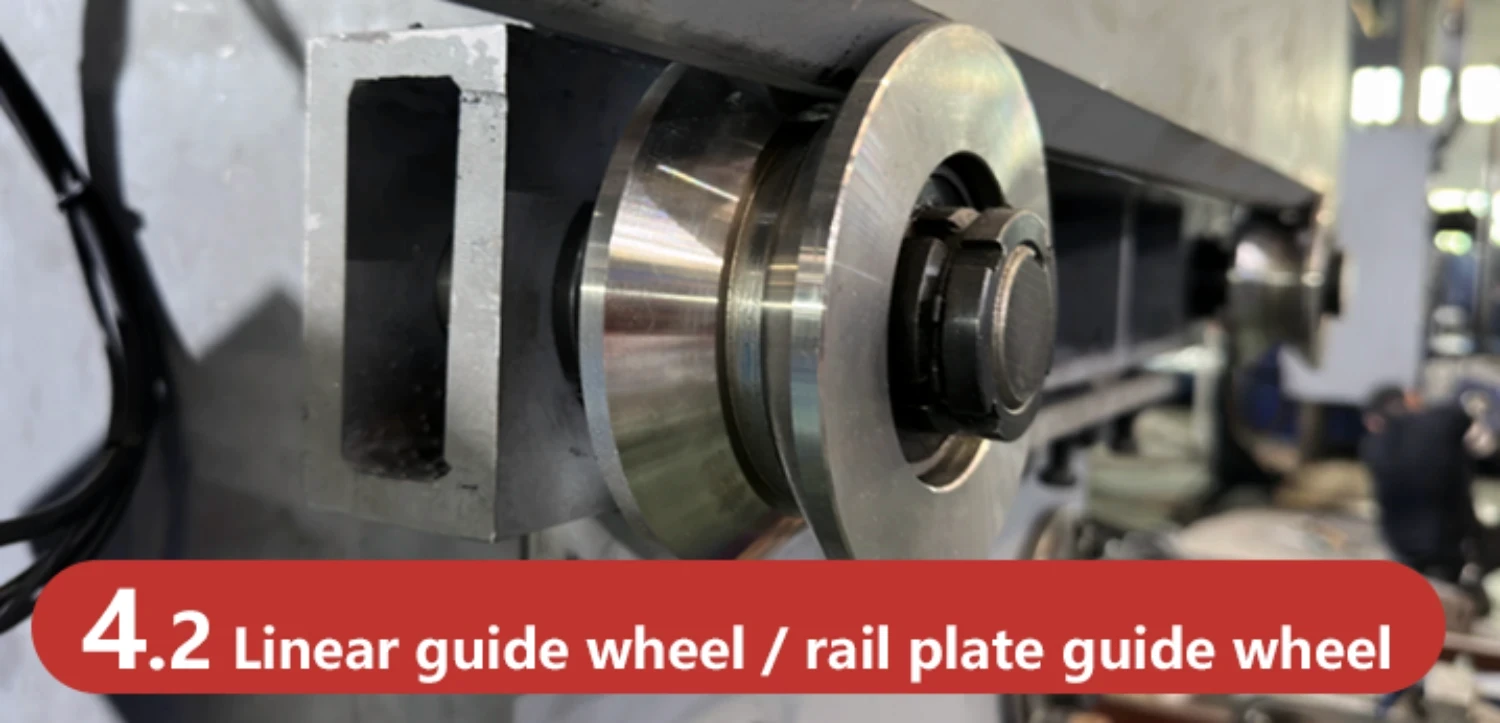
Maintenance frequency:1 months
Maintenance method:Clean mud、grease adding
Maintenance reason(Detailed description):The linear guide wheel and the rail plate guide wheel control the left and right movement of the flywheel. Continuous consumption of grease or adhering of dust will cause the flywheel to have inaccurate pressure on diamond ropes, which will affect the cutting accuracy.
4.3 Flywheel flange
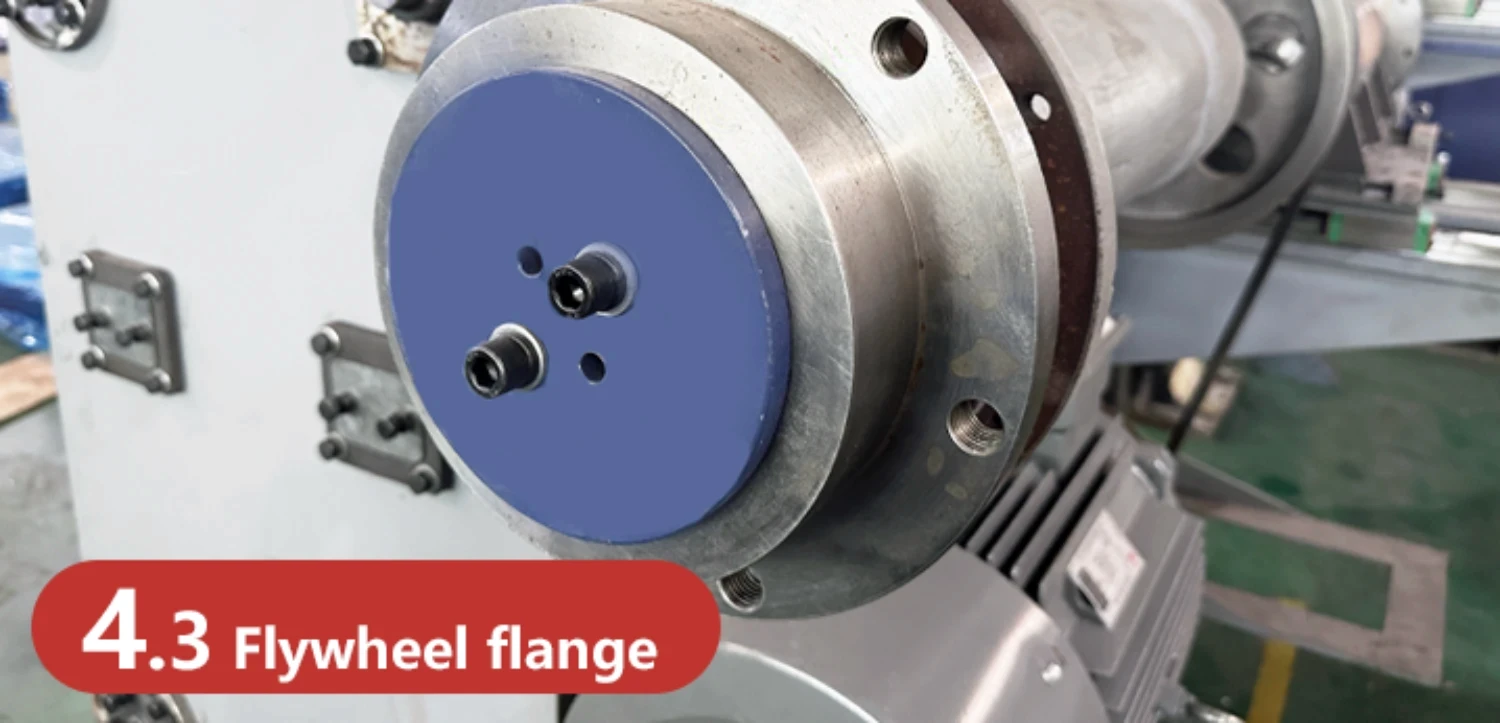
Maintenance frequency:3~6 months
Maintenance method:When change rubber strips remove rust from flange, change screw
Maintenance reason(Detailed description):During the rotation of diamond ropes, water may be thrown on flywheel flange, causing the screws on the flange to rust. Rusty screws will jam the flywheel, which may cause the flywheel not to run normally, and even cause it to fall off in severe cases. When the flywheel is suffocated, if the rubber strip needs to be replaced, it can only be removed violently, which may cause serious damage.
4.4 Flying wheel
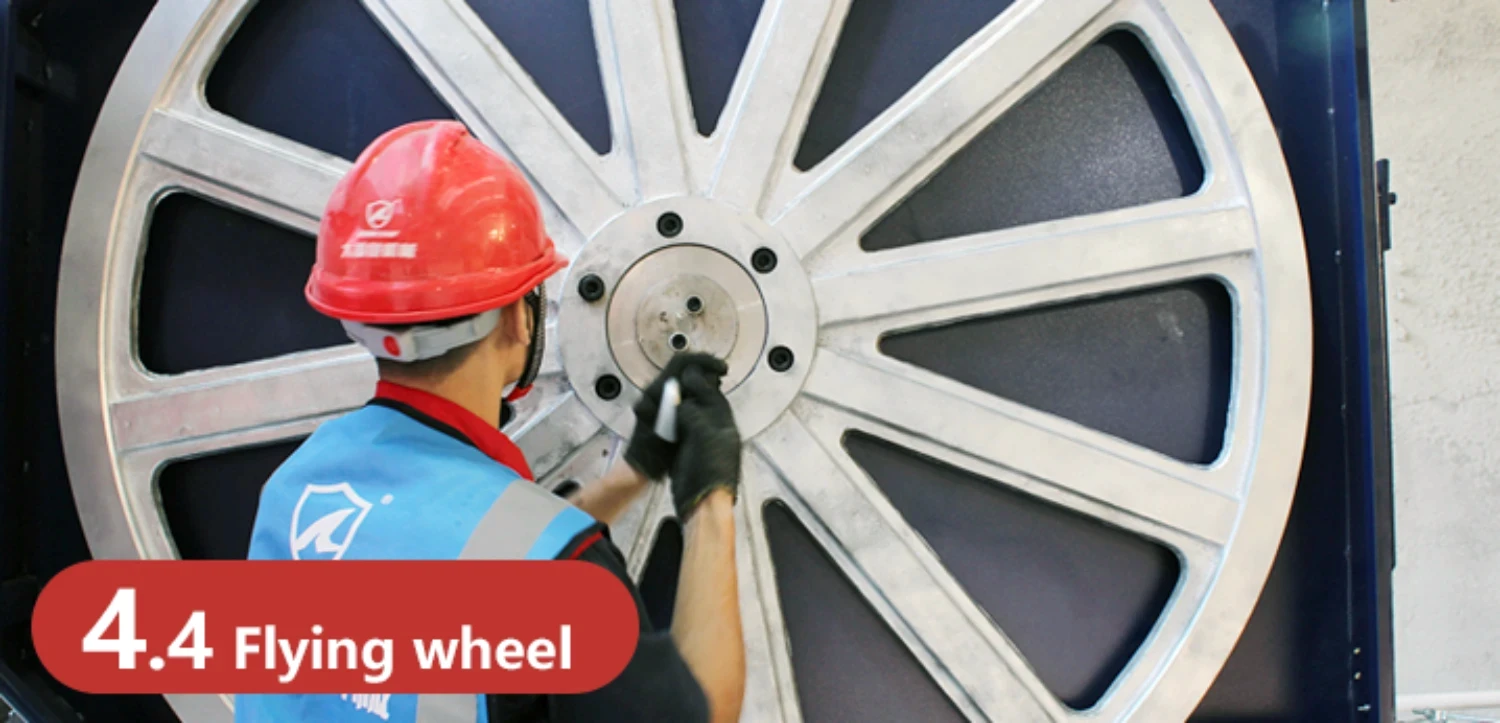
Maintenance frequency:1 week~1 month
Maintenance method:Marl removal
Maintenance reason(Detailed description):When the flywheel is running the diamond wires, the wires might throw lime on flywheel surface, and the long-term adhesion will cause the lime to harden. This hardening will destroy flywheel balance and cause machine to shake.
Wire Saw Machine Maintenance area 5. Hydraulic station
5.1 Oil pipe
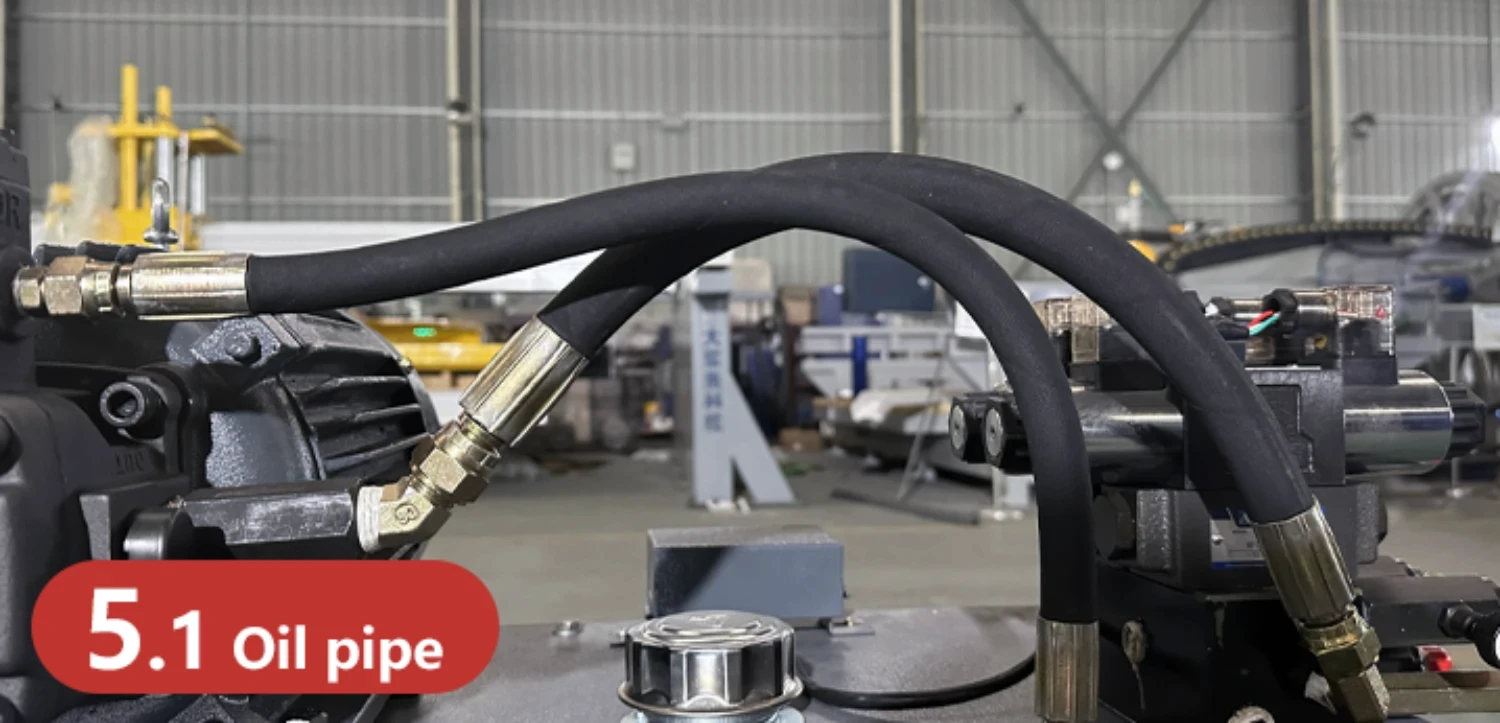
Maintenance frequency:3~6 months
Maintenance method:Oil leakage detect
Maintenance reason(Detailed description):The oil pipe might be damaged and leak oil in an unenclosed environment, causing the pipe to lose pressure. This can loosen the diamond wire saw and ultimately lead to the lacking of precision in the cutting process.
5.2 Hydraulic components
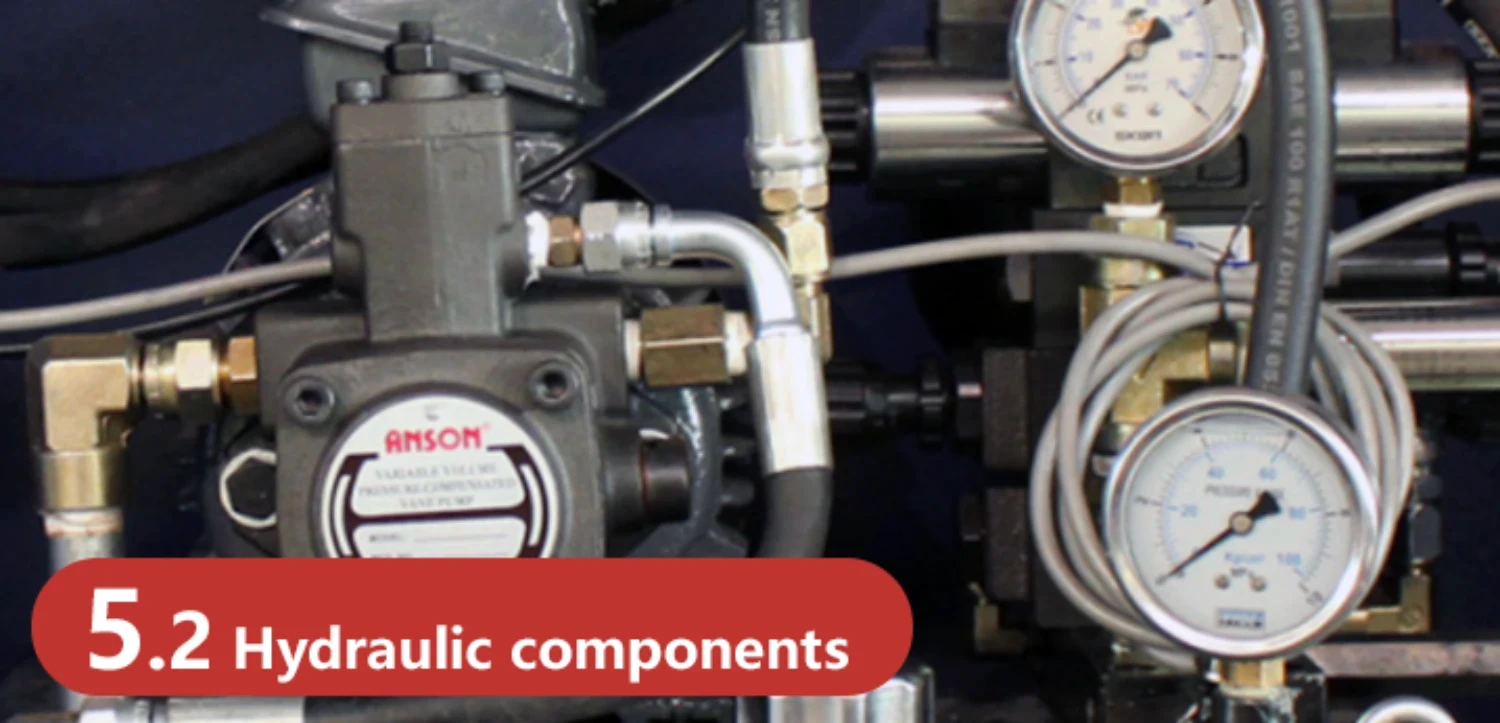
Maintenance frequency:3~6 months
Maintenance method:Pressure adjustment, marl removal, grease adding
Maintenance reason(Detailed description):If the hydraulic components are used for too long, it may causes abnormal pressure or accumulate dust and increase friction. This can loose the diamond wire saw and ultimately lead to the lacking of precision in the cutting process
5.3 Oil box
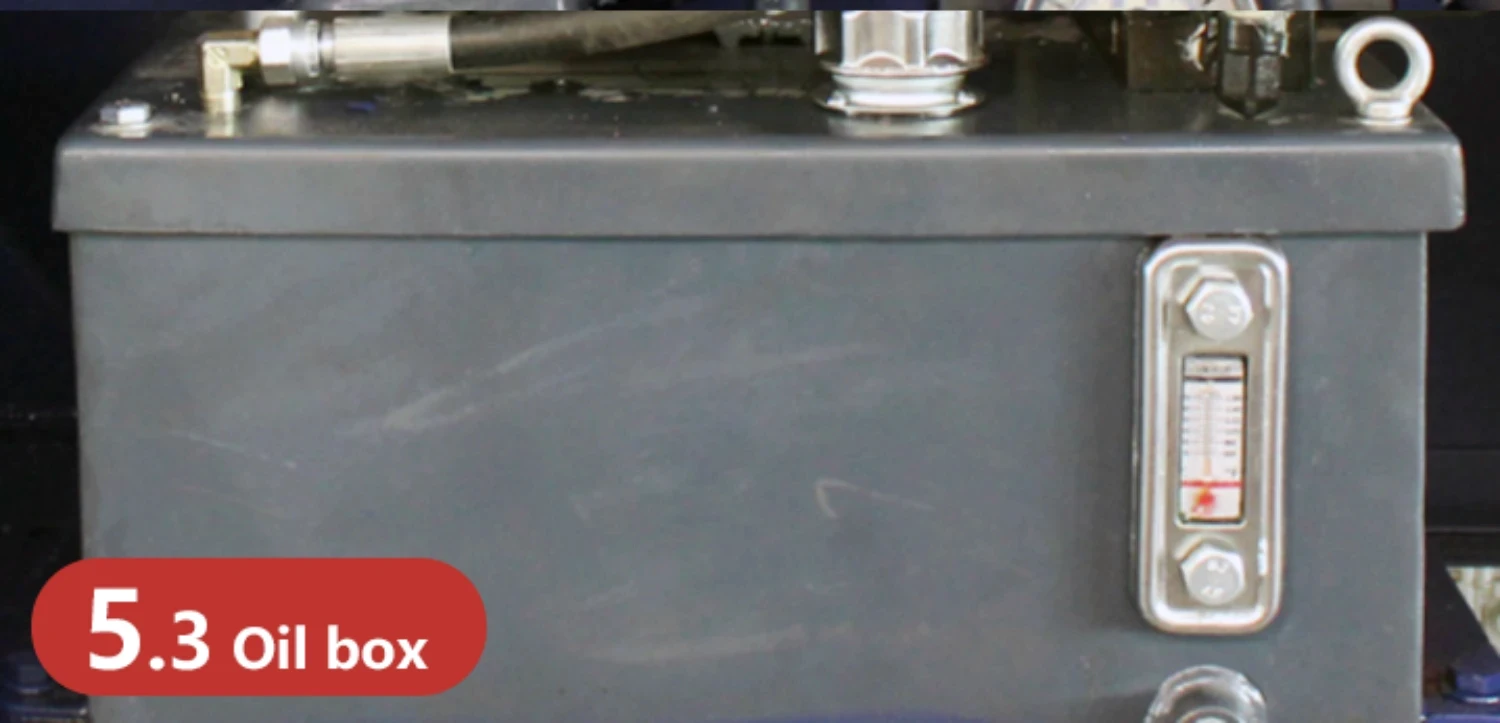
Maintenance frequency:1 year
Maintenance method:Clean and change hydraulic oil
Maintenance reason(Detailed description):Long-term use of hydraulic oil is prone to pollution, aging and dilution, resulting in the failure of hydraulic system to work normally, which in turn affects the stability of hydraulic pressure and reduces the cutting accuracy.
Wire Saw Machine Maintenance area 6. Electric control
6.1 Electric cabinet
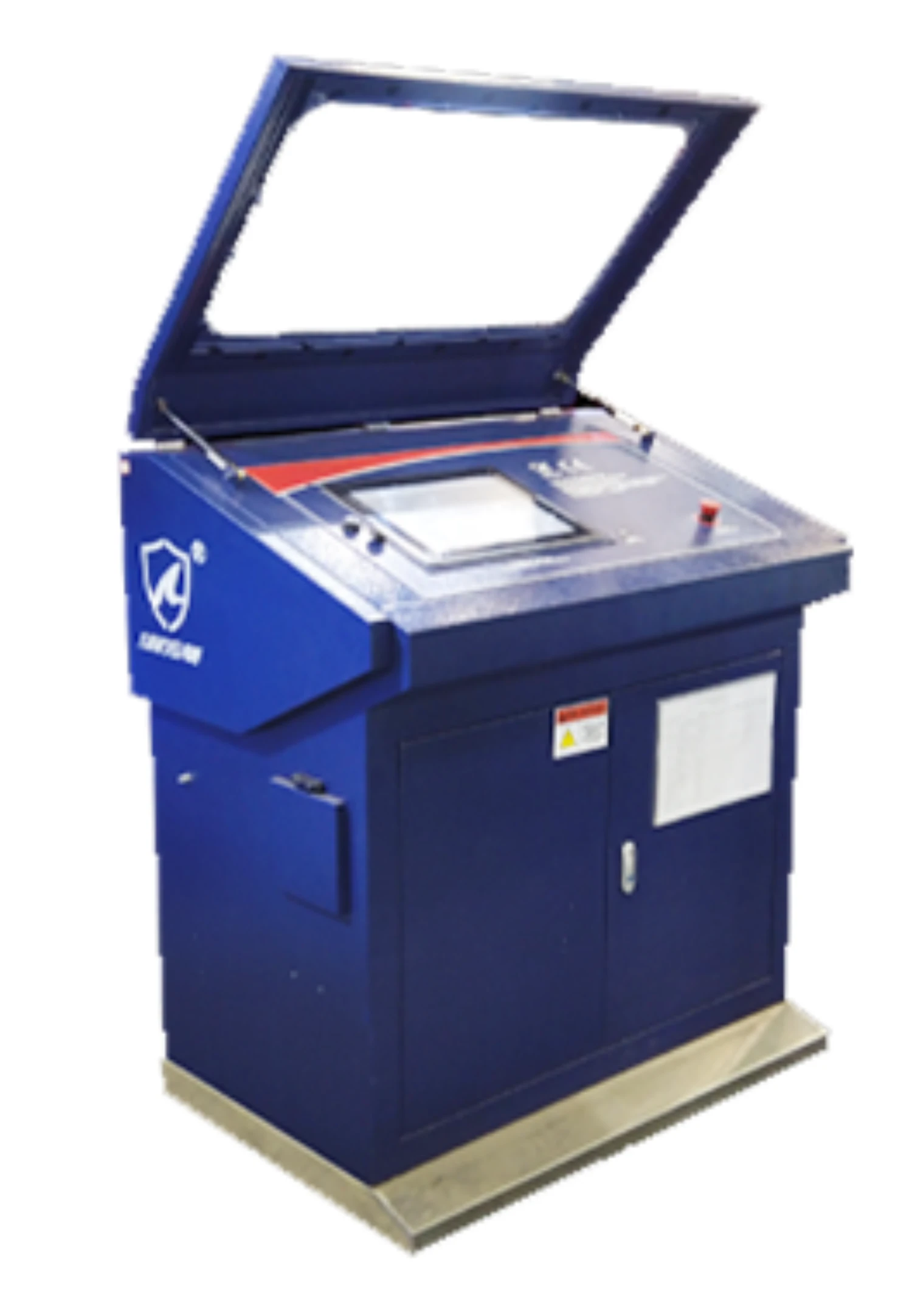
Maintenance frequency:1 week~1 month
Maintenance method:Dust clean
Maintenance reason(Detailed description):If the electric cabinet is opened for too long, it is easy to accumulate dust and generate static electricity when it encounters water vapor, resulting in circuit damage. In severe cases, it may cause the internal components of the electric cabinet to stall, hinder heat dissipation, and even burn components, resulting in greater losses.
6.2 Computer
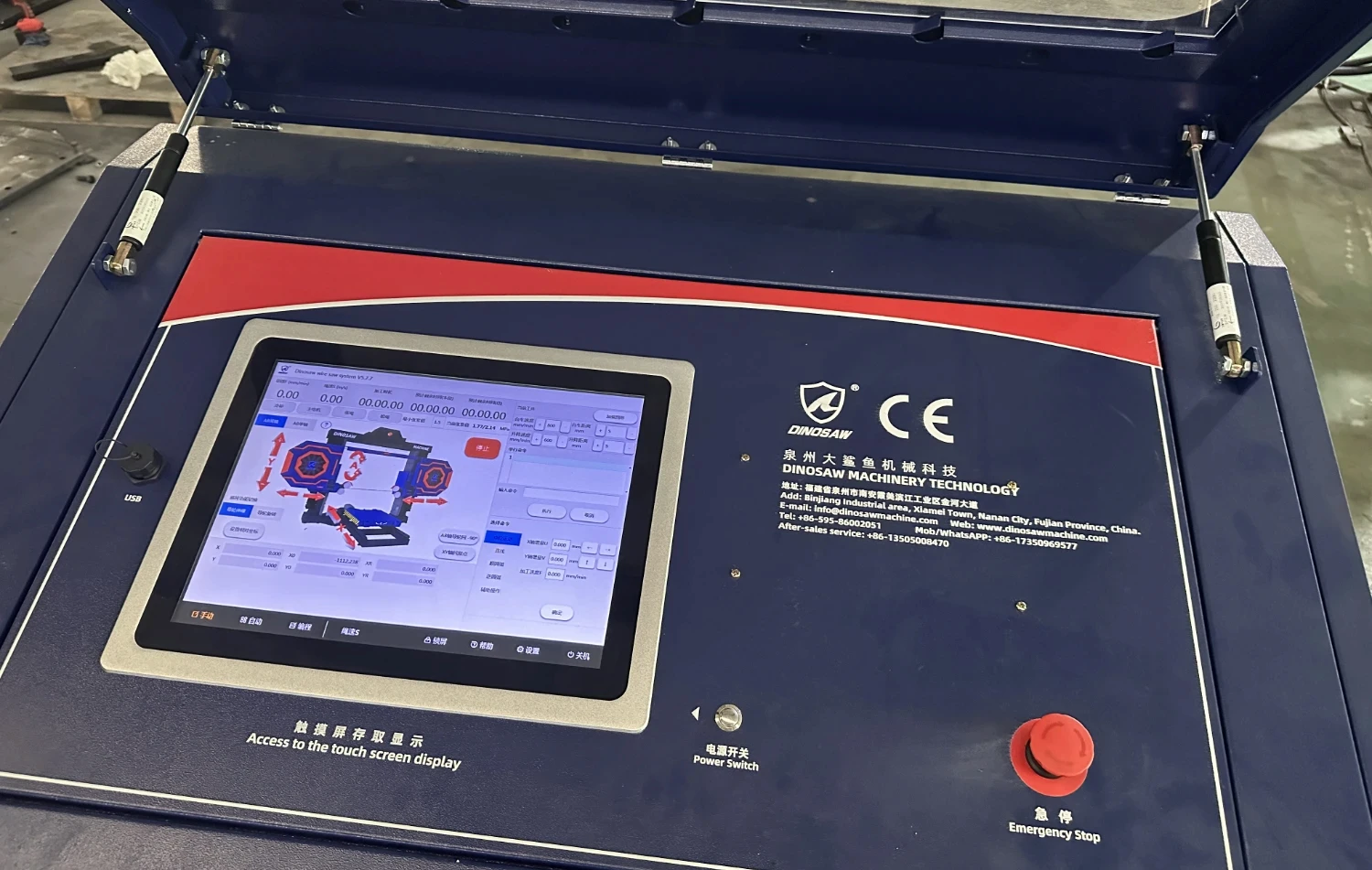
Maintenance frequency:1 month
Maintenance method:X/Y axis distance detect, data adjustment
Maintenance reason(Detailed description):If the electric cabinet is opened for too long, it is easy to accumulate dust and generate static electricity when it encounters water vapor, resulting in circuit damage. In severe cases, it may cause the internal components of the electric cabinet to stall, hinder heat dissipation, and even burn components, resulting in greater losses.
6.3 Limit switch
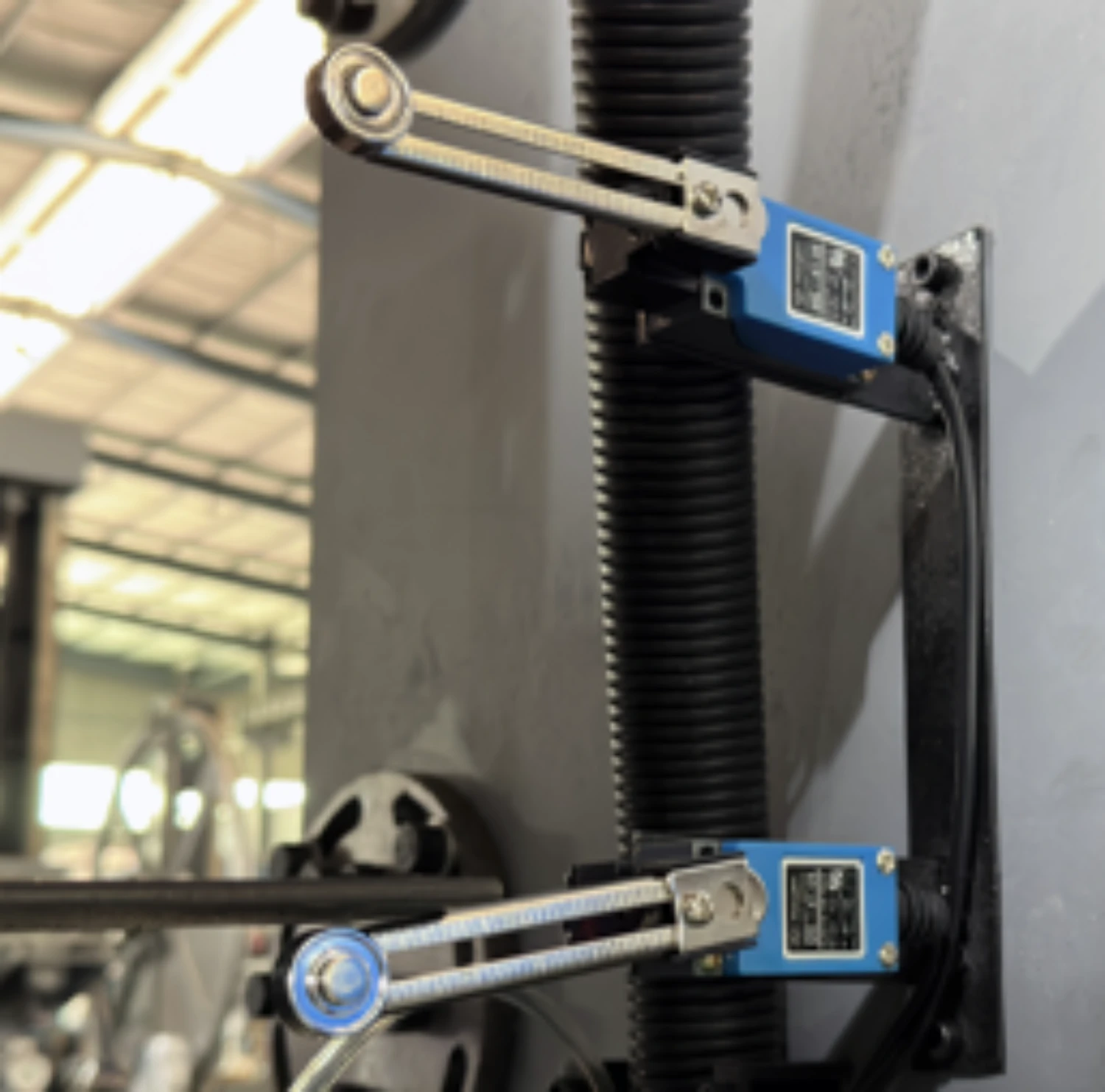
Maintenance frequency:1 month
Maintenance method:Limit switch function test
Maintenance reason(Detailed description):During machine daily operation, factors such as irregular operation, collision, dust accumulation, corrosion, friction, etc. will damage the limit switch. At this time, the trolley may exceed the travel range, causing equipment collision and screw rod jamming, resulting in heavy losses.