
Diamond wire cutting has become an essential method for precision cutting in various industries, including stone, metal, ceramics, and advanced composites. However, achieving smooth cuts without vibrations can be challenging. Vibration in diamond wire cutting can cause poor cut quality, increased wear on the wire, and longer processing times, which is particularly problematic when dealing with high-value or delicate materials.
In this article, we will explore the main factors contributing to vibration in diamond wire cutting and provide actionable solutions to minimize these issues, ensuring high-quality cuts and longer tool life.
Factors Causing Vibration in Diamond Wire Cutting
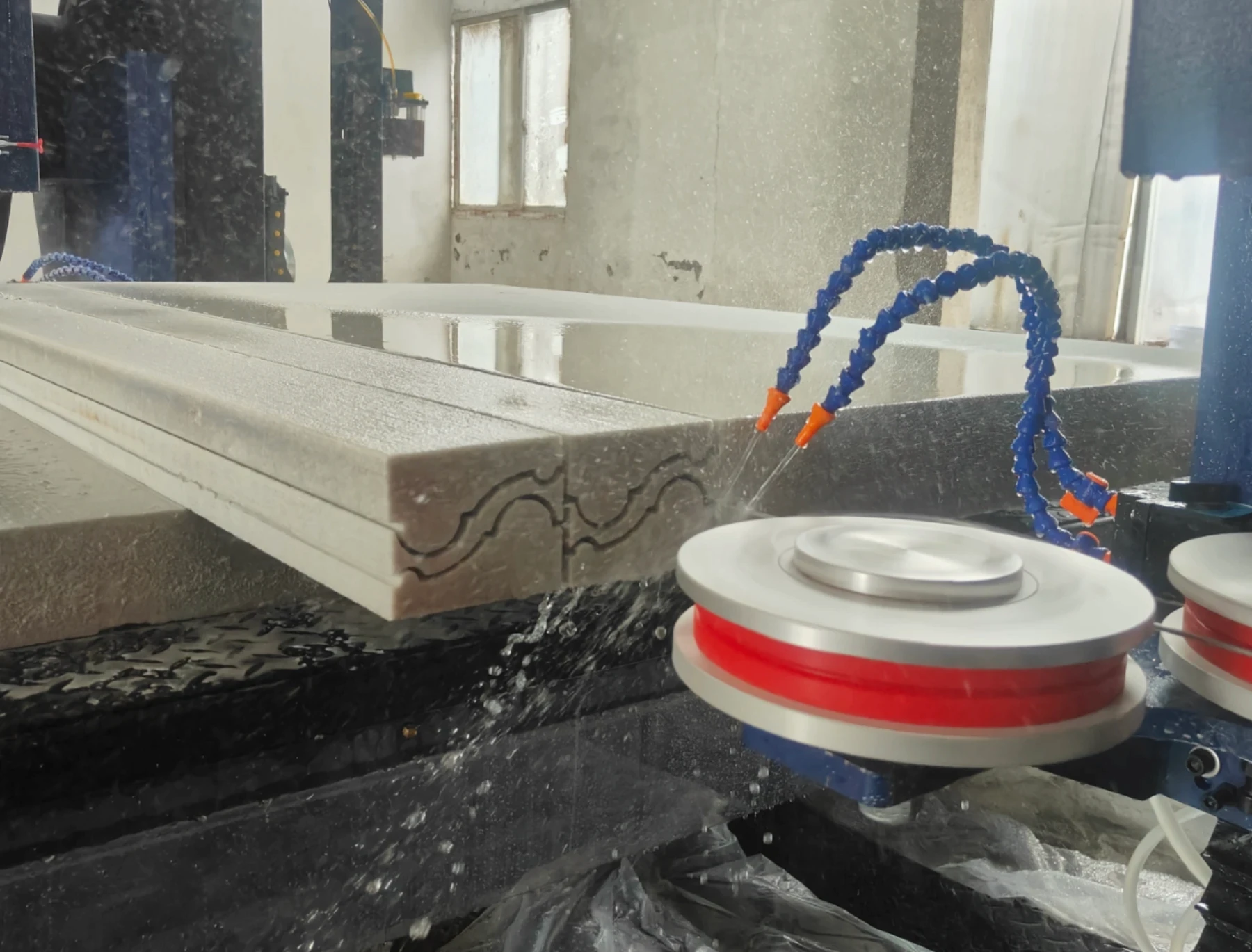
1. Inconsistent Tension on the Diamond Wire
One of the most common causes of vibration is inconsistent tension along the diamond wire. If the tension is too high, the wire becomes overly taut, leading to excessive force and vibration. Alternatively, insufficient tension results in an uncontrolled wire that oscillates unpredictably, causing uneven cuts.
Possible Symptoms:
Visible wave patterns in the cut surface.
Increased wear on both the diamond wire and the workpiece.
Difficulty in achieving precise cuts.
Solution:
Proper wire tension should be calibrated before starting the cut. A reliable tension control system, especially one with automatic adjustments, will ensure the wire remains at optimal tension throughout the cutting process. Regular tension checks and adjustments during cutting can help maintain smooth operation and reduce vibrations.
2. Misalignment of the Wire Saw Machine
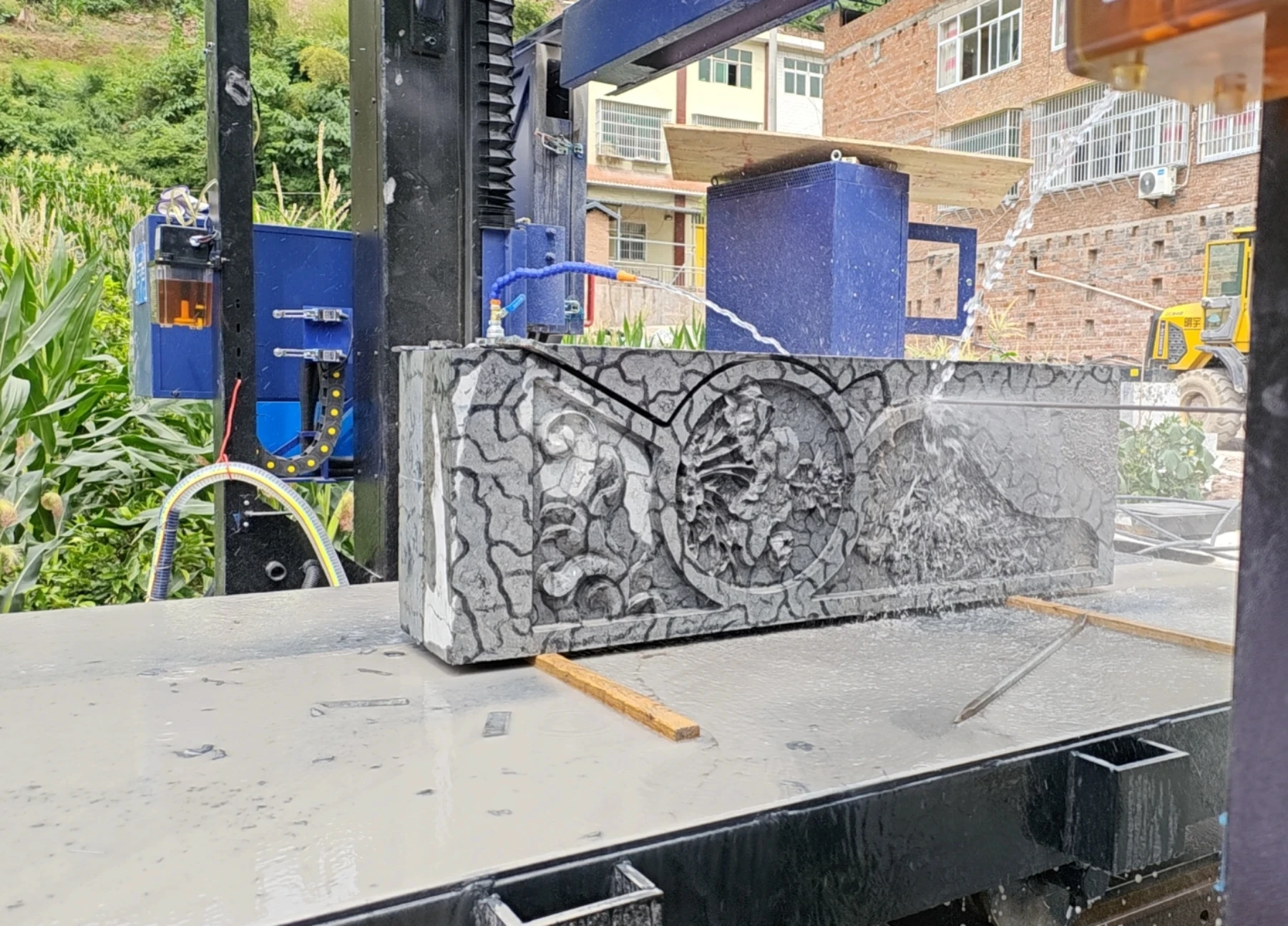
Misalignment of the wire saw machine can lead to uneven contact between the wire and the material, which generates vibrations during cutting. This misalignment can be caused by improper installation, machine wear, or poor maintenance practices.
Possible Symptoms:
Irregular cuts with rough edges.
Increased noise from the cutting machine.
Visible damage or wear on the diamond wire.
Solution:
Proper alignment of the machine is essential for vibration-free cutting. Routine maintenance and calibration of the wire saw, along with checking all components for wear or misalignment, will prevent this issue. If necessary, realign the equipment or replace damaged parts to restore stability.
3. Incorrect Cutting Speed
The cutting speed must be carefully controlled to avoid excessive vibration. Cutting at too high a speed can generate heat and cause the wire to vibrate. On the other hand, cutting too slowly increases friction and reduces efficiency, leading to more vibration.
Possible Symptoms:
Increased wear on the wire.
High friction and excessive heat generation.
Vibration and noise during cutting.
Solution:
Adjust the cutting speed according to the material and wire type. Softer materials may allow for faster cutting speeds, but harder materials, such as metal or stone, often require slower speeds to reduce vibration and prevent wire overheating. Fine-tune the speed for optimal results and material preservation.
4. Poor Quality or Worn Diamond Wire
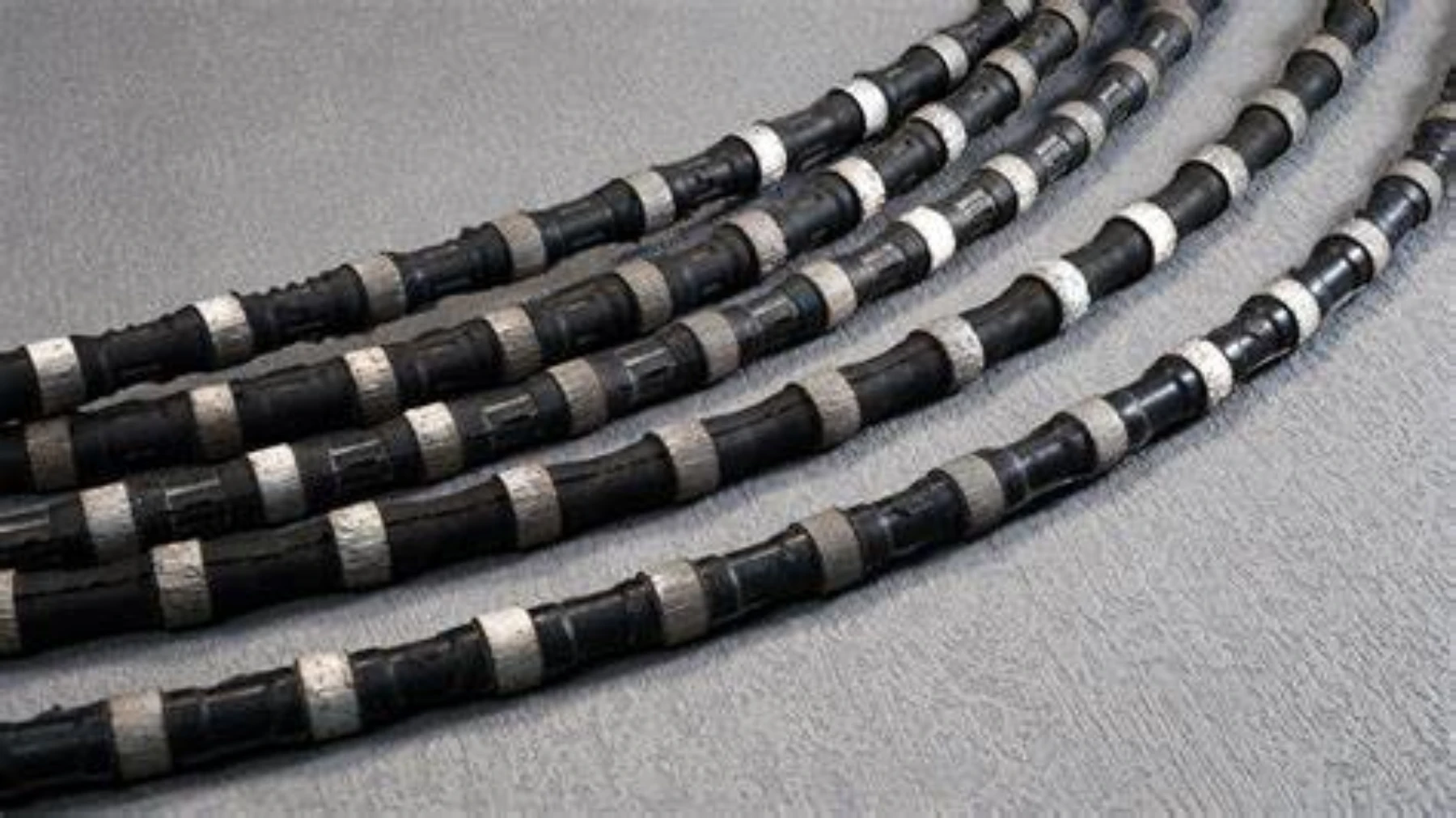
The condition of the diamond wire is a critical factor in preventing vibration. Worn-out wires or those with uneven diamond grit distribution can lead to inconsistent cutting forces, which increase vibrations.
Possible Symptoms:
Poor surface finish on the workpiece.
Uneven cutting performance.
Frequent need for wire replacements.
Solution:
Inspect the diamond wire for signs of wear, including visible damage or uneven grit. Regularly replace old or worn wires with high-quality alternatives to ensure consistent cutting performance. Storing and maintaining the wire properly will also extend its lifespan.
5. Incorrect Support or Rigidity of the Workpiece
The rigidity and support of the workpiece are crucial in minimizing vibrations during the cutting process. If the workpiece is not securely clamped or is unstable, it can move during cutting, causing vibrations that affect both the wire and the cut quality.
Possible Symptoms:
Movement of the workpiece during cutting.
Distortion in the cut geometry.
Excessive vibration and noise.
Solution:
Ensure the workpiece is securely fastened using rigid clamps and supports. Use vibration-damping materials or fixtures to absorb any potential vibrations during the cutting process. A stable workpiece will reduce the risk of errors and improve cutting precision.
Solutions for Effective Vibration Control
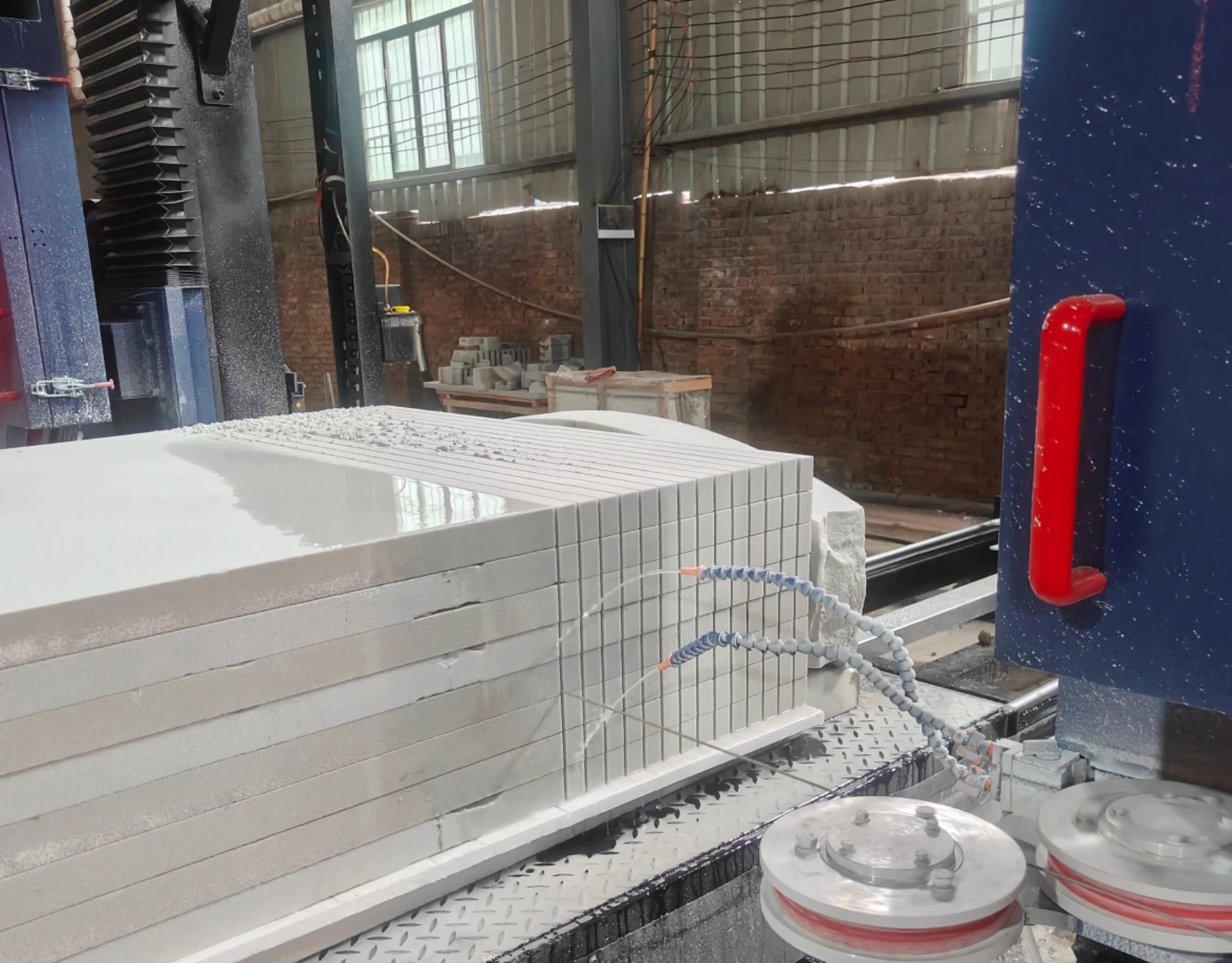
Proper Tension Control System
DINOSAW's diamond wire saw machines are equipped with advanced automatic tensioning systems that dynamically adjust wire tension to maintain optimal cutting conditions throughout the process. This ensures a consistent, vibration-free operation, minimizing wear on the wire and enhancing the precision of cuts.
Additionally, DINOSAW integrates real-time sensors that monitor the wire's tension and performance. These sensors provide immediate feedback to the system, allowing for automatic adjustments to keep the cutting process stable, reducing any potential vibrations caused by inconsistent tension.
Regular Maintenance and Alignment
To avoid issues stemming from misalignment, DINOSAW provides comprehensive user manuals and maintenance guides to assist customers in correctly setting up and maintaining their wire saw machines. Regular maintenance and alignment checks based on the guidelines provided will ensure the equipment performs at its best and helps prevent vibration-related issues from affecting cutting performance.
Optimal Cutting Parameters
DINOSAW offers specialized diamond wire formulations tailored for different materials. These custom wire compositions strike the perfect balance between sharpness and durability, maximizing cutting efficiency and extending the life of the wire. The right choice of wire ensures smoother cuts, even when working with challenging materials, while minimizing vibrations during the cutting process.
High-Quality Diamond Wire
DINOSAW delivers high-performance diamond wire saws that are engineered for different materials, whether it’s hard stone, metal, ceramics, or composites. By offering the right diamond wire for each application, DINOSAW ensures that the cutting process remains stable and vibration-free, achieving cleaner cuts and reducing the wear and tear on the wire.
Enhanced Support Structure for the Workpiece
DINOSAW machines feature a cast-structure design that provides greater stability and rigidity. This robust structure reduces vibrations during the cutting process, ensuring that both the machine and workpiece remain steady. This translates to smoother, more accurate cuts and a longer lifespan for both the machine and the wire.
Conclusion
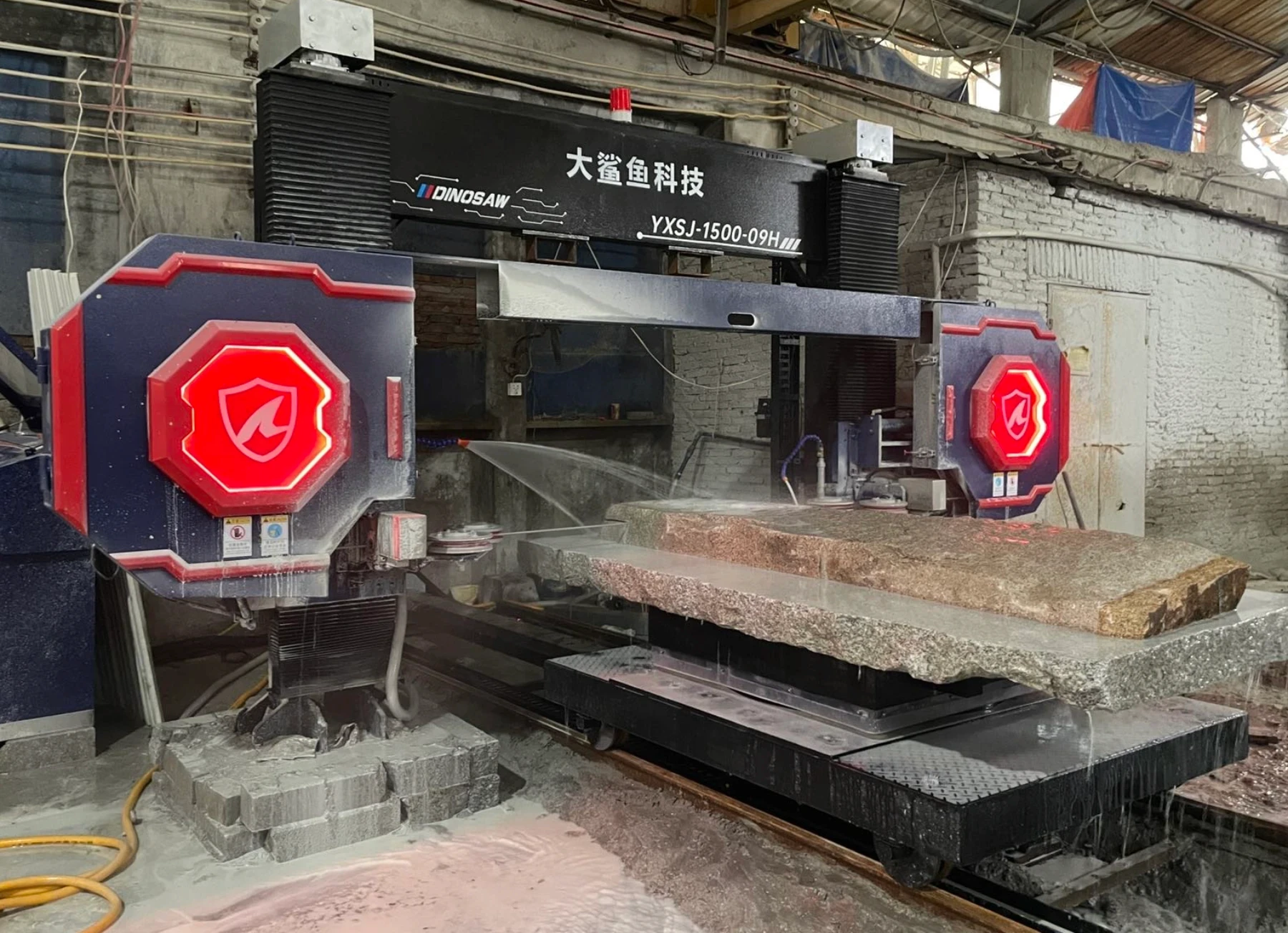
Vibration during diamond wire cutting is a common issue that affects cut quality and processing efficiency. However, by identifying the key factors that cause vibration and implementing the right solutions, you can significantly improve your cutting performance, reduce tool wear, and extend the lifespan of your wire.
At DINOSAW, we specialize in providing high-quality diamond wire saws that address these issues, delivering smooth, precise cuts with minimal vibration. If you want to improve the efficiency and accuracy of your cutting processes, contact us today to learn more about our advanced wire saw machines.