
The Ceramic Foam Cutting Challenge in Building Materials Industry
Ceramic foam has become an essential material in the building materials industry due to its exceptional thermal insulation, soundproofing, and fire resistance properties.
The way ceramic foam is cut significantly impacts both its structural integrity and functional properties, making the cutting method a critical factor in the final product quality and performance.
⚙️Limitations of Traditional Cutting Methods
Bridge Saws Critical Issues | Edge Grinding Machine Drawbacks |
---|---|
![]() | ![]() |
|
|
CNC Diamond Wire Saw: Superior Ceramic Foam Cutting Machine
DINOSAW's diamond wire saw technology delivers precision cutting for ceramic foam with minimal material loss, solving critical production challenges in the building materials industry.
Inqury for a DINOSAW CNC Ceramic Foam Cutting Machine→
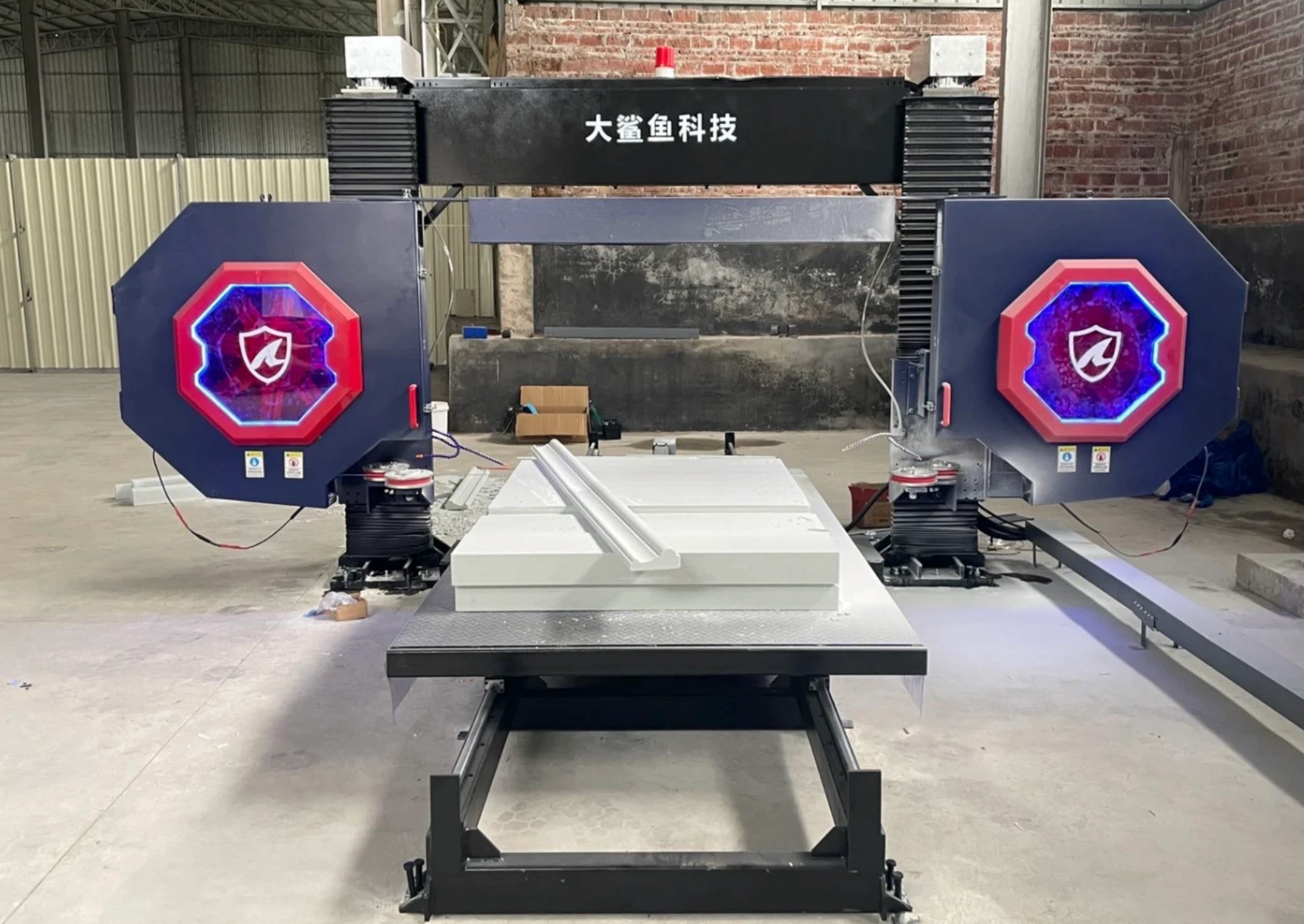
Working Principle
CNC wire saw cutting technology fundamentally differs from traditional methods:
A thin, flexible diamond wire impregnated with industrial diamond particles serves as the cutting element
Computer numerical control (CNC) technology guides the wire with high precision
The wire saw removes only the minimal amount of material necessary to create the cut
Controlled wire tension and cutting speed ensure optimal surface finish
Multi-axis movement enables complex three-dimensional cutting patterns
This technology reduces material waste by up to 80% while improving cutting precision and surface quality.
Key Benefits for Ceramic Foam Profiling
Our wire saw machines directly address manufacturers' most critical challenges:
🎯Precision | ⚡Efficiency | ♻️Material Savings |
---|---|---|
±1mm cutting accuracy ensures perfect fit for construction applications with critical tolerances. | Higher throughput with 1000mm/min c utting speed and reduced setup times. | Minimizes material waste by up to 80% and enables repurposing of cut-off edges through optimal layout planning, significantly reducing production costs. |
🔧Design Freedom | 👆Easy Operation | 💰Low Maintenance |
Create complex shapes and intricate designs impossible with traditional methods for innovative architectural applications. | Intuitive interface requires minimal training, reducing labor costs and specialized skill requirements.Supporting CADs import directly. | Lower maintenance costs with easy-to-replace diamond wire saws and longer service intervals. |
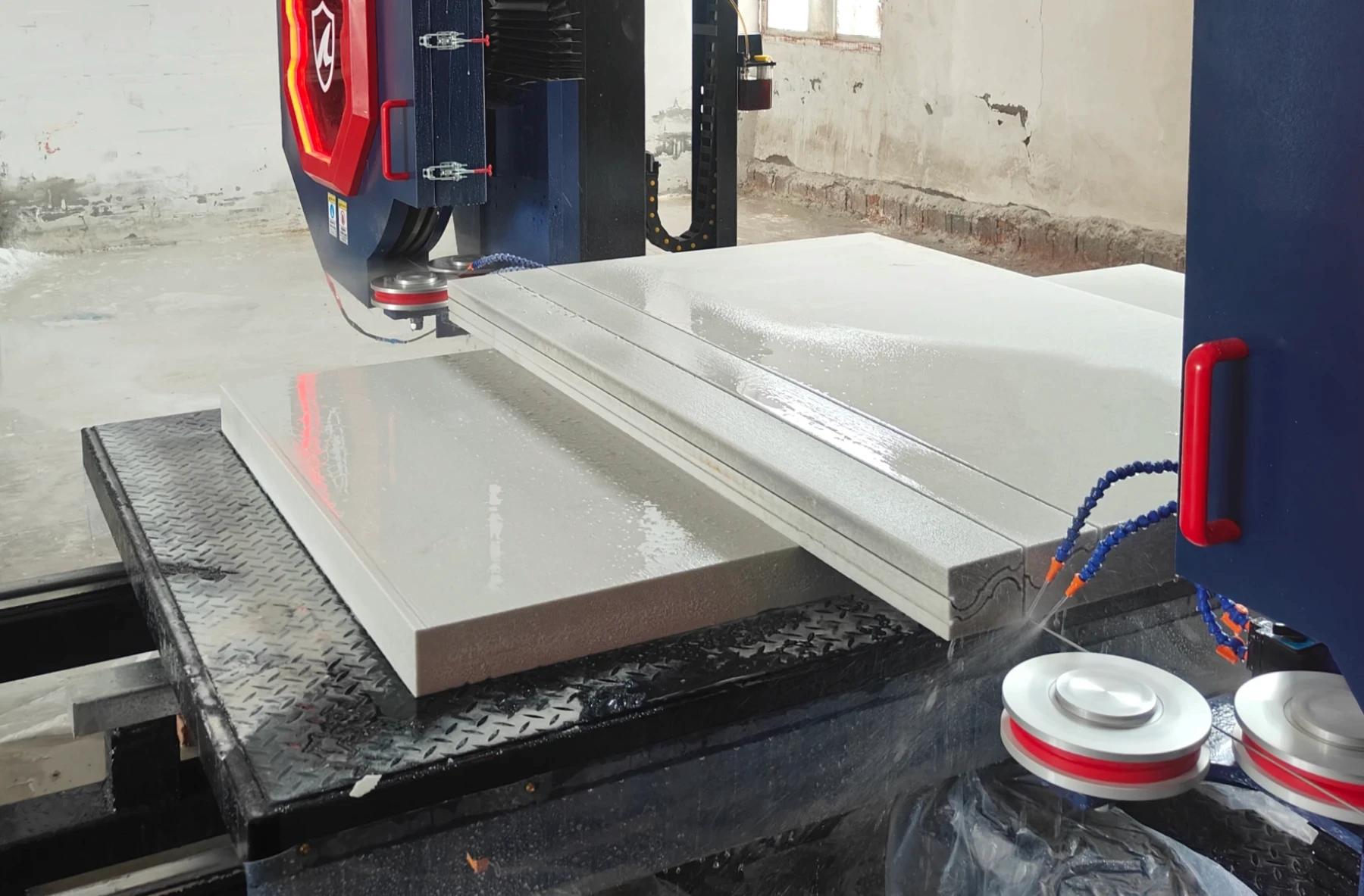
Essential Applications in the Building Materials Industry
Our diamond wire saw cutting machines enable precise fabrication of ceramic foam components for various building material applications:
Thermal Insulation Products | Architectural Elements |
---|---|
Create perfectly sized thermal insulation components for:
The low weight property of foamed ceramics offers significant advantages in reducing building dead loads while providing exceptional thermal insulation performance with precise cutting tolerances. | Fabricate precise decorative and functional elements:
Diamond wire saw cutting enables limitless design possibilities for complex geometries in modern architecture, allowing foamed ceramics to be used in premium applications for shopping malls, villas, hotels, and conference rooms. |
If you're looking to enhance your ceramic foam production efficiency and quality, DINOSAW is ready to help with a customized assessment of your specific needs.
View more ceramic foam cutting cases with DINOSAW CNC machines
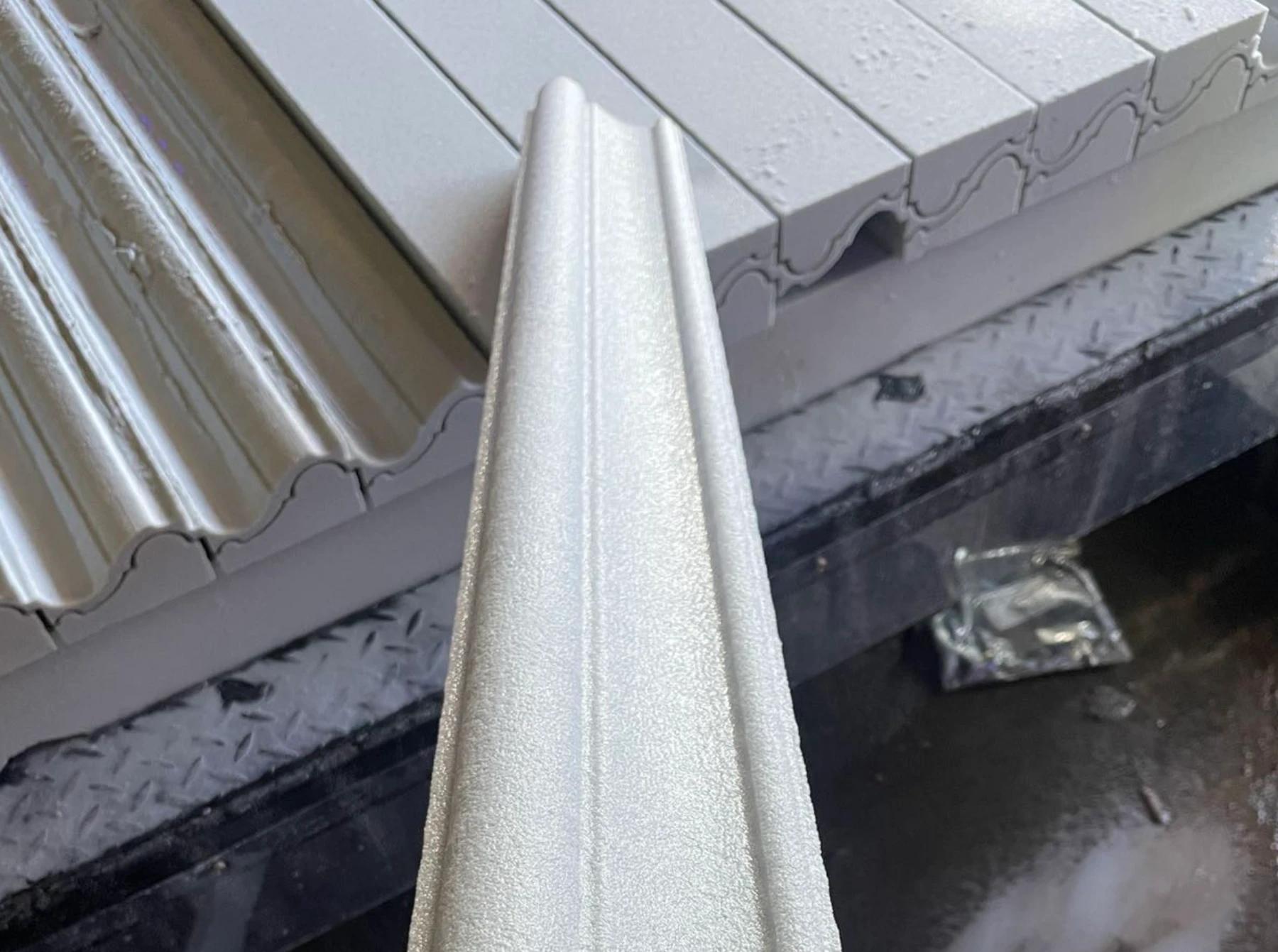
Frequently Asked Questions About Ceramic Foam Cutting
Get answers to common questions about our diamond wire saw machines for ceramic foam applications:
What materials can CNC diamond wire saw machines cut?
CNC diamond wire saw machines can effectively cut a wide range of materials beyond ceramic foam, including EPS (Expanded Polystyrene), concrete, various stone, steel, semiconductor materials, graphite, and more.
How thick can ceramic foam blocks be for cutting?
Our standard CNC wire saw models can cut ceramic foam blocks up to 1200mm in thickness, while our industrial-grade machines can handle blocks up to 2400mm thick. Custom configurations are available for specialized requirements.
Does DINOSAW provide training for operators?
Yes, comprehensive operator training is included with every machine purchase. Our technical team provides both on-site training during installation and ongoing remote support. Most operators can become proficient with the basic functions within 3 hours and master advanced features within 1-3 days.
Conclusion: The Future of Ceramic Foam Processing
The building materials industry continues to evolve with increasing demands for higher performance ceramic foam components. Advanced cutting technologies have become a critical factor in meeting these market requirements while maintaining economic viability.
Diamond wire saw technology represents a significant advancement in ceramic foam processing by addressing the fundamental challenges of material preservation, dimensional accuracy, and production efficiency. The benefits extend beyond direct cost savings to enable new design possibilities and market opportunities.
As sustainability and resource efficiency become increasingly important, manufacturers who adopt cutting-edge processing technologies gain both competitive and environmental advantages. The future belongs to those who can maximize material utilization while delivering the highest quality ceramic foam components to the market.
Upgrade your ceramic foam Production with DINOSAW
Related Products
CNC Engraving Machine for foamed ceramic
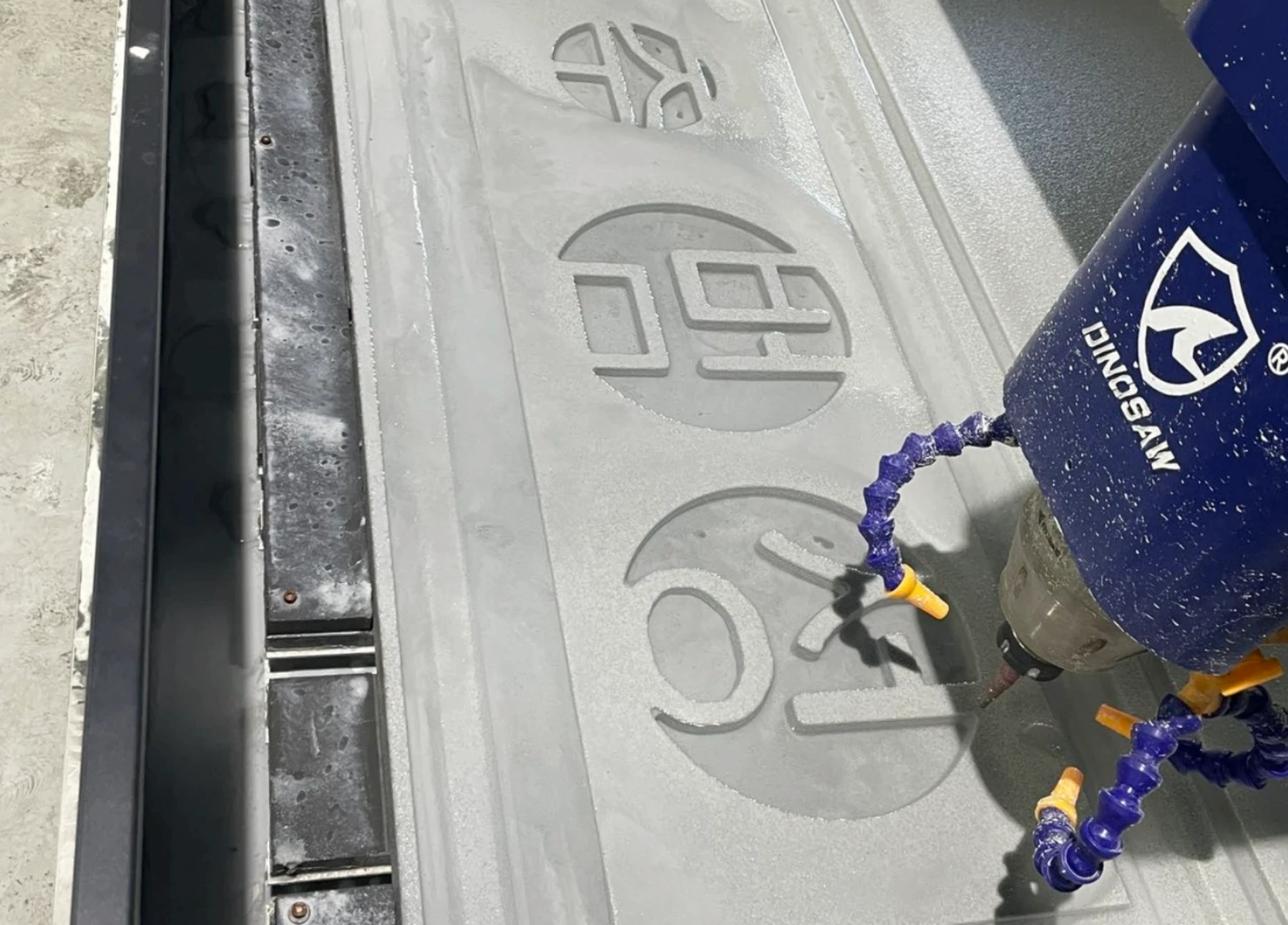
Splitting Machine for thin slabs splitting
